Category: Uncategorised
Oktava ML19 recording acoustic guitar
Lustraphone VR53 magnets (again)
AKG DX11 microphone… with reverb!
You can easily imagine the product development meeting at AKG back in nineteensixtysomething…
Or something like that. It is certainly true that AKG made some great microphones (too many to list) and a lot of nasty ones (also too many to list). The AKG BX10 and BX20 spring reverbs have become studio classics. And so if any company was well positioned to make a microphone with a built in reverb, it had to be AKG. The result is the AGK BX11, which is a battery powered dynamic microphone with a built in single spring reverb and a battery powered circuit which uses five germanium transistors to amplify the signal and drive the reverb spring.
![]() |
AKG DX11 echo microphone |
There are some major shortcomings to this design. It is impossible to use this as a hand held microphone because the spring just rattles around. The microphone capsule is not great quality, battery life is short and the germanium transistor circuit is noisy. And although the microphone element is certainly not of hi-fi quality, and the spring is ‘boingy’ rather than lush, none of that matters because it is quirky and fun and offers something unique.
![]() |
AKG DX11 capsule and circuit board |
The owner of this one had enquired about converting the mic to run on phantom power, but that was not trivial because the circuit has a positive ground, and I also had doubts over whether we could supply sufficient current with phantom. The output of the microphone of the DX11 is unbalanced 15K ohms or unbalanced 200 ohms.
![]() |
AKG DX11 spring reverb |
I added a small Neutrik 10:1 transformer to drop the unbalanced 15K output down to a balanced 150 ohms*, which makes it a bit more compatible with mic preamps and mixers, and wired to a normal balanced XLR output. The transformer fitted in neatly in the cavity behind the capsule. (*You could use a 1;1 transformer from the 200 ohm output).
![]() |
DX11 circuit hacks – Click on the image to see a bigger version. |
After a bit of initial testing, I came to the conclusion that reverb is better than the microphone, and so, after a discussion with the owner, we decided to fit a line input to the reverb circuit. The microphone capsule itself has a measured output of 250 ohms, so it was easy to hack into the circuit at that point, via a switched mini-jack socket. Now one can run other things into the reverb, such as a better dynamic or ribbon mic, a quiet line input or a guitar via a DI box.
Here is a picture of Adam from Extinct Audio test-driving the DX11 reverb (on the bench) with a Jazzmaster guitar…
I hope to share some sound clips soon.
Further reading
Review of Extinct Audio microphones – Amazona.de
This week we had a couple of nice reviews of the Extinct Audio family of ribbons microphones. I was involved in the design of these microphones and the start up of the business and it is nice to see them gaining some traction. This review was published on the German language site Amazona. You can read the original version here, which contains lots of useful sound clips and pictures. Below is an English translation.
TEST: EXTINCT AUDIO BM9 VIKING UND BLACK OPS, BÄNDCHENMIKROFONE
There are Englishmen that every child knows. Harry, Charles and William are currently the talk of the town, Ringo, Paul, George and John have written music history. Away from the limelight, there are four Brits, Stewart, Adam, Paul and Ant, who handcraft fine ribbon microphones in their small microphone forge Extinct Audio. Our author Raphael Tschernuth took a closer look at these fine British mics.
Ribbon mics have enjoyed unbroken popularity over the past two decades. While they were almost extinct until the early 1990s, they have been celebrating a resurgence at least since the Royer 121 and digital recording. The name Extinct Audio is an allusion to the fact that this type of microphone had almost disappeared from the face of the earth and was considered extinct. An old “Snake Stone” fossil, a local legend, serves as the company logo for the young English company.
Extinct Audio was founded by none other than Stewart Tavener of Xaudia.com, one of the reference addresses when it comes to ribbon microphone repair. In 2007 Stewart started to offer his service for ribbon microphones and since then the order book is bursting at the seams.
Some of you might be familiar with the microphone blog of Xaudia Elektrik, where you can find a lot of information about long gone microphone models of all kinds (links in the box below).
Since the founding of Xaudia, Stewart has had well over 10,000 ribbon microphones on his desk for repair. He knows them all – from great RCA classics to fancy designs from Italy or Denmark to modern China replicas. His experience over the last few years has finally led him to not only repair microphones, but to develop independent designs and bring ribbon microphones to the market himself.
Together with his friends Adam and Ant, he started Extinct Audio, with the goal of offering handmade ribbon microphones at a reasonable price. Stewart and Adam are musicians themselves and know how tough life can be with this profession. But not only did they want the mics to be affordable, they also wanted them to be responsibly made from local resources and meet the highest quality standards.
In fact, the company that builds the bodies is located just a few miles from the Extinct Audio workshop. The transformers required for a ribbon microphone are of their own manufacture. The wooden boxes of the microphones are made by a company that otherwise mainly produces wooden boxes for high-quality whiskey bottles. And yet the English somehow manage to keep the price in the €900 range, while other mics, such as the 121 from Royer or the Coles 4038, have seen huge price increases, especially in recent years.
The underlying design of the two Extinct Audio microphones under review is based on the Bang & Olufsen BM3 which was developed in Denmark in the late 50s. This microphone was at the time one of the smallest ribbon microphones, its form factor was only made possible by the development of an ever stronger magnetic materials.
Perhaps some of you are familiar with the really thick ribbon microphones from the 1930s, such as the Siemens M25 or the BBC Marconi, each weighing in at over 4 kilos. The high weight and the high mass were necessary at that time, because there were no magnetic alloys with which strong magnetic fields could be realized in a space-saving way, as today with modern neodymium variants.
The BM3 from Bang & Olufsen was a revolution in the 1950s and was and was an inspiration for the Royer R121 in the 90s. The newly available neodymium magnet materials helped the Royer 121 achieve tremendous output. The Extinct Audio BM9 is also based on the concept of the BM3, even keeping the BM naming for “ribbon microphone.”
The BM9, nicknamed “Viking,” is a general-purpose ribbon microphone with a pure figure-of-eight characteristic. In terms of sound, it is clearly in the tradition of legendary ribbons such as the RCA 44 BX, Melodium 42b, etc. Its full-bodied bass range paired with brilliant highs gives voices and instruments an inimitable “Bigger Than Life Sound”. The proximity effect is, as typical for this type of microphone, very pronounced and therefore a little distance to the sound source is recommended.
No less than the great John Williams used various BM9s for the recording of his soundtrack to Star Wars for the orchestral recordings. And this for a production that can afford any microphone imaginable. This could almost be called an accolade for Extinct Audio (not to be overlooked from about 30 seconds on):
The Black Ops, on the other hand, is recommended for all applications where the microphone is to be positioned close to the sound source. It is particularly well protected against wind and air currents, and its specially adapted transformer ensures a well-balanced sound even at a very close distance from the sound source.
This allows the Black Ops to be positioned directly next to a guitar amp or snare drum, for example, without having to equalize the bass range by using an EQ. Like the BM9, the treble imaging is incredibly detailed and smooth for a ribbon microphone. The Black Ops was designed for harsh live use; among others, the English band Foals relied on various Black Ops for their recent live tours.
The “classic” BM9 Viking uses a 1.8 µ thick ribbon, the Black Ops uses a slightly thicker 2.5 µ. For comparison: the thread of a Spider’s web is about 6µ thick, a human hair even 50µ. Therefore, one should be as careful as possible with this type of microphone.
The frequency range of both mics is between 30 Hz – 15 kHz and sonically the foreground and rear are absolutely identical. While the BM9 has an impedance of 300 ohms, the Black Ops has an impedance of 250 ohms – in practice this is irrelevant, as both mics with these values will harmonize perfectly with current preamps. The sensitivity of the BM9 is 2.23 mV/Pa, a high value that does not demand too much from the microphone preamp. Thus, the BM9 delivers a higher signal than many a moving coil candidate. Nevertheless, it should be mentioned at this point that ribbon mics often benefit sonically from stand-alone, external preamps. For entry-level or mid-range audio interfaces, an inline amplifier is a good choice, and the market is now teeming with them. Alternatively, one can also fall back on an active variant.
While testing the two mics described above, the manufacturer posted on Instagram that development of the active variant was complete. Without further ado, I made an effort to get hold of one of the first series models for the test and I was sent the first available stereo set. The active circuit increases the output signal by about 22 dB of noise-free gain. This significantly relieves the preamp and the recorded signal is comparable to that of condenser microphones. We will also consider this model in the practical test.
Extinct Audio offers manufacturing character par excellence with its microphones. When unpacking the microphones, the testers can’t help but be amazed at how much love and attention to detail has gone into the work.
The wooden cases are, as already mentioned, not cheap barware from the Far East, but extremely solid and excellently crafted. They offer perfect protection for one or two microphones. A serial number is emblazoned on a metal plaque on the outside, and inside the casket a signed certificate provides information about the day on which the microphone was manufactured and which employee took care of which production steps. The microphones themselves are beyond reproach in terms of workmanship.
This is pure perfection, without compromise. Metal workmanship and are excellent, logo and metal gauze perfectly attached, all edges rounded, the serial number engraved on the back – that’s how it should be. With their 355 grams, the Black Ops and BM9 feel good in the hand and radiate their very high value. Due to their light weight, they can be securely positioned even with simple microphone stands and are easy to set up. A screw-in mount was also included with the review sample, but ordinary medium-sized microphone clamps can also be used.
If there is one application that one immediately associates with the Royer 121, it is the miking of a guitar amp. This ribbon mic has earned legendary status since its introduction in the late nineties. Compared to many classic ribbon mics, it delivers a somewhat thinned-out bass image and can be positioned relatively close to the amp. With an old, venerable Coles 4038, for example, the immense proximity effect would absolutely require the use of a high-pass filter. So with ribbon mics, it’s always a matter of finding the sweet spot and using it profitably in your work.
In the following audio sample, you can first hear the mentioned Coles 4038 at a distance of only 13 centimeters. The recording is much too bass-heavy due to the proximity effect. After applying a high pass filter (100 Hz, 24 dB/oct) the tide turns and the sound suddenly becomes usable, possessing a “creaminess” typical of ribbons:
In comparison, you can hear the sound of the Shure SM57 dynamic moving coil microphone, which is considered the “industry standard” for amp recording. This is much more “grainy” and garish to work.
In terms of sound, the Extinct Audio BM9 Viking ribbon microphone is on the “classic” side of power. Similar to the Coles 4038, it therefore requires the use of a high-pass filter to deliver a balanced signal at a distance of only 13 centimeters:
The Extinct Audio Black Ops, on the other hand, does not require an additional filter, since the bass increase was compensated for by the transformer used. As a reference, you will also hear the Royer 121 afterwards, unprocessed at a distance of 13 centimeters from the speaker. Again, an HP filter would suit the signal well. With Black Ops, on the other hand, the signal is immediately “mix-ready”.
The different proximity has a direct impact on the use. Positioning all microphones at the same distance in front of a sound source would therefore be extremely bad for a meaningful test report, since every microphone deals differently with the bass boost and has its own sweet spot. The BM9 is full-bodied, with the Royer 121 the proximity effect is somewhat reduced and with the Black Ops it is somewhat less than with the Royer. On the acoustic guitar I therefore decide on three different distances
Extinct Audio Black Ops: Distance 30 centimetres
Royer 121: distance 40 centimetres
Extinct Audio BM9 Viking: distance 50 centimeters
Many thanks at this point to the really impressive singer/songwriter Fabian Holland, who recorded the acoustic guitar for this test.
The test shows that the Extinct microphones can easily compete with the Royer 121 in terms of sound quality. This is impressive when you consider the price difference of almost 1000 €. Ribbon microphones are also excellent for imaging percussive instruments. One reason for this lies in the natural mapping of the transients, which are mapped very quickly and vividly.
In the following example you hear the drummer Achim Färber. The BM9 stands a few meters away from the drums. It is a mono recording without any effects. The Black Ops was positioned on the snare, also without any change in signal:
During the test period, the Black Ops has become one of my favorite microphones for the snare drum. The figure-8 characteristic makes it excellent for masking out adjacent toms or hi-hats. The strong attenuation on the 90- or 180-degree axis can be used excellently.
Last but not least, here’s a short sample I recorded myself with two BM9s as overheads and a subkick. As before: no EQ, no compressor… nüschte, as the Berliner says.
During the test period, I had the chance to use the Extinct Audio Mics on many other sound sources. They delivered excellent results on cello, as a stereo Blumlein set on piano, or on vocals with soft S sounds. The stereo pair was also perfectly matched before delivery, and the two measurement curves were absolutely identical.
By the way, the active version sounds exactly like a passive BM9, only louder. Sure, you could also loop in an inline preamp like the Fethead, but that makes the construction a bit unwieldy on the one hand, and on the other hand the shielding falls by the wayside. Unfortunately, inline preamps are prone to turning cell phone radiation into audible tones. When the network builds up, beeping and whistling can therefore be picked up unintentionally. The active version is well shielded in this respect and does not transfer any noise to the audio signal. And by the way, it looks much better…
Final Thoughts
Chapeau! The small microphone workshop Extinct Audio, delivers with the BM9 Viking and the Black Ops two ribbon microphones that leave nothing to be desired. The workmanship was done by hand with great attention to detail, the materials used are high quality, locally “sourced” and guarantee a long life. Each microphone is individually measured before delivery and stereo pairs as well as active +48 variants are also available. The latter brings the already high output to the level of a condenser microphone. Sonically, the BM9 is in the tradition of legendary ribbon microphones, while the Black Ops is predestined for close miking. Both reproduce percussive instruments with tangy transients, deliver vocals with smooth S-sounds, and are predestined for a wide range of applications and sound sources. In addition, they possess a remarkable top end for microphones of this type. Combined with a very good price/performance ratio, this leaves an unclouded picture that clearly stands out from many Asian competitors due to the high quality.
+
Excellent workmanship
Very good stereo matching, measured values
High output
Very versatile
Great, classic ribbon sound (BM9)
Balanced sound when positioned close to the sound source (Black Ops)
Durable design, handcrafted, made from local resources
Reslo Microphone Documents
![]() |
Reslo PR ribbon microphone |
Here are a bunch of scanned information sheets published by Reslosound for various dynamic and ribbon microphones in their range.
Reslo RB information sheet
Reslo CD information sheet
Reslo VMC information sheet
Reslo CR information sheet
Reslo PR information sheet
Beyer M500. A.K.A. Why does my microphone sound like a kazoo?
OK, this might be a little bit controversial: the M500 is my least favourite ribbon microphone from Beyerdynamic. This is for a number of reasons. I’ll list them.
- The transformer rolls off a lot of bass. More so than an M260.80.
- The grill has a dense cloth screen which also reduces the bass response.
- The internal baffle has a plastic plate in front of the ribbon which robs yet more bass and causes other problems, as I will explain in a moment.
![]() |
Beyer M500 and a Kazoo. Can you tell the difference? |
These three points are all intentional parts of the design. The M500 was intended as a vocal microphone and designed to be used at point blank range. The severe bass cut compensates for the proximity of the ribbon, and the extra screening and baffle protect the ribbon from plosives and other blasts of air. So to some extent you have to take your hat off to Beyer and say ‘chapeau‘ for making a ribbon that can compete with an SM58.
But that’s my point really. Ribbon mics naturally have a big rich proximity effect, which is one of the things that we love about them. In the M500 a lot of work has gone into removing that sound. To my mind, the M500 is good for one job only (close up vocals), and there are other microphones that do that job better. If you like to chew your microphone then you might as well use an SM58 (or better still a Beta 58), and use a ribbon for those places where it excels.
These microphones are no longer made but change hands on eBay and Reverb at inflated prices. I think the biggest issue with them is expectations. Some buyers expect them to sound close to, say, an M260, and are disappointed when they don’t. In particular they sound very thin when used on instruments at a normal recording distance. At Xaudia we often get asked to modify these mics to have more bass and have more of a classic ribbon sound.
The motor and ribbon are more or less the same between the two mics, but everything else is different. It is possible to get a better bass response from the M500 by swapping out the transformer for a full range model*, which helps a lot. But the mic can still sound odd because of what is in front of the ribbon.
So let’s get back to that baffle that I mentioned in item number 3. Here at Xaudia we call this the ‘Kazoo Flap‘. Let’s take a look at it.
![]() |
The M500 “Kazoo Flap”. This bit of perspex causes trouble. |
You can see that there is a flat piece of clear plastic in front of the ribbon. The problem here is that is can vibrate and come loose over time. I often see these come unstuck at one end and it can vibrate like the reed on a clarinet or saxaophone. It sounds like a kazoo solo has been added to every recording!
Luckily it easy to fix. The baffle can be re-glued or removed completely. I often do the latter and replace it with some fresh acoustic fabric and steel mesh.
![]() |
M500 baffle modifications. |
Swapping the transformers and the baffle gets the M500 as close to an M260 as it can be. The grill construction and the acoustic chamber behind the ribbon are different between the two microphones so they can never be quite the same, but the changes improve the bass response by huge amount and, to my ears, make it sound like a proper ribbon microphone.
![]() |
Beyer M500 – designed for close up use on vocals. |
* We make a suitable full range transformer that will fit inside an M500.
AGA-Baltic T2 ribbon microphone
Xaudia has been running for about 15 years and we get a lot of repair work which now seems routine. We see hundreds of Reslos, B&O mics and Beyers in particular. When I started out, everything was new but it is now a rare occurrence to see a ribbon microphone that I have not worked on before. Sometimes I think I have seen it all and then something new comes along. These moments are exciting and a new challenge is always appreciated.
![]() |
AGA-Baltic T2 Ribbon Microphone |
This rare Swedish beauty came in for repair recently. Not only had I never worked one one before, I had never even heard of it! This was made by AGA-Baltic, who (according to Swedish Wikipedia) came into existence in 1928 after a merger between AB-Baltic and AGA companies. They made some rather elegant radio sets and, later, TV equipment. They clearly made microphones too.
![]() |
Motor and transformer assembly from AGA microphone |
From the magnet and transformer technology, I would date this as an early 1930s microphone. The motor comprises two large steel pole pieces sandwiched between four large horseshoe magnets, and it uses a massive toroidal transformer to raise the output voltage and impedance to 30 ohms. The holes around the ribbon are most likely designed to increase the high frequency response of the microphone. The only comparably sized toroidal transformer that I have seen is in the Siemens / Telefunken M201, which dates back to around 1928. Transformer technology got smaller quickly!
![]() |
AGA motor after corrosion removed |
The magnets in this microphone have held their field well and I measured about 2500 Gauss in the ribbon gap, which is fairly respectable for a microphone of this age. For reference, a good Melodium 42B would measure about 3000 Gauss. However, the whole motor assembly was corroded, so I stripped it down, treated with Rust-Off and then re-painted to prevent further corrosion. Everything else was cleaned and new grill cloth and mesh fitted. With old microphones that have been out of service for decades it is often best to do a complete rebuild.
![]() |
AGA hardware parts being cleaned. |
With a new ribbon in place the sound was weak and disappointing. The old toroidal transformer has not aged well and the transmission of high frequencies in particular was attenuated giving a dark woolly tone with a lot of noise. It also seemed to be a good aerial for picking up hum too.
Impedance matching didn’t help so we were faced with the dilemma of keeping it all original or switching out the transformer and having a useful working microphone, but potentially losing some of the value to collectors.
![]() |
AGA Baltic T2 – Half way back to working condition. |
This situation is always a difficult choice, but after consultation with the owner we decided that the microphone should be a working studio tool, and the most sympathetic repair would be to fit a new transformer from a Coles 4038. This replacement is also a toroidal transformer so we keep the ‘toroidal sound’, if there is one*. (*There probably isn’t.) The old transformer will of course be returned to the owner and can be re-installed in the future for collectors value.
And the results were good! The new transformers has a much better high end response, lower noise floor and does not pick up hum. The microphone is quite useable and still sounds very much like a vintage ribbon microphone. A well designed transformer should be there for impedance matching purposes and should not be contributing too much to the sound anyway.
![]() |
Restored AGA-Baltic ribbon microphone |
I wonder what other rare and unusual microphones are out there waiting for me? Surprises and challenges are welcome!
Further Reading. There is not much information on the internet about these microphones but this does get mentioned briefly at the AGA museum.
Decca Ribbon Tweeters part 2
Last week I posted about repairing some vintage Decca London ribbon tweeters. I was confident that I had done a good job but was unable to do listening tests in context as I only had the tweeters to play with. These are now back with Andy, their owner, who kindly sent in his impressions and some photos. Overall I think we have done a good job and it’s a nice feeling to have helped get these back up and running.
![]() |
Decca Volt speaker with ribbon tweeter |
“The [new] ribbon sounds smooth, crisp and clear with no tizz or distortion. I ran it for a while at different volumes and with different music and it sounds excellent with everything I gave it. It is very close in sound to the original in the other speaker with the soundstage being in the middle and correct. I had to try hard to notice a difference, Bob Marley’s Is This Love has some high frequency cow bell drum noises and you could hear they were slightly crisper and louder from the new ribbon. The crossover point in the Volt’s is about 1200hz so any imbalance between the two tweeters is easily heard as the singer tends to move off centre.
![]() |
New ribbon installation at Xaudia |
“I think the differences could be classed as being between an old and new ribbon the sound from them is so close. I assume as the new ribbon breaks in it will soften in sound a bit. I am tempted to switch the other new ribbon in as well.
![]() |
Andy’s impressive hi-fi setup. |
“Considering the lack of info on the ribbons I thought getting a close match sonically was not good but it’s turned out to be very close indeed. It is a huge relief to know that if a ribbon gets damaged again I can get help.
“I am not sure but you might get a lot of interest, when I was trying to find someone to repair my ribbons I came across a huge amount of forum posts on the same issue dating back about 5 years. Nobody had managed to find anyone so in theory there are a lot of ribbons to repair out there.”
Thanks to Andy Mcgregor.
STC 4136 revisited
![]() |
STC 4136 microphone |
A long time ago I posted about the STC 4136 condenser microphone and how to modify it to work on standard 48V phantom power, using a small circuit built on perfboard.
![]() |
|
|
I had another opportunity to work on one of these microphones. This one was a challenge as it had no circuit inside at all, just the capsule and bodywork, although that also gave free scope to start from scratch.
![]() |
|
|
Space is tight in this microphone, but with a careful layout and small components everything will fit neatly. My solution for this one was to fit a small KM84 circuit and Neutrik NTE10/3 transformer. This transformer performs well, does not break the bank, and can be squeezed into tiny spaces where nothing else will go.
![]() |
New circuit board and transformer |
This time I commissioned a printed circuit board rather than working on perfboard, which does save time and look more professional. The board will be useful for other projects too – I have a handful of other small microphones which would benefit from updated, lower noise circuits.
![]() |
Made in England |
Thanks to Robert at Russell Technologies for the board layout and advice.
Decca Ribbon Tweeters part 1
![]() |
Decca London ribbon tweeters with huge transformers. |
![]() |
The horn of a Decca ribbon tweeter |
![]() |
Brass mess behind the horn, |
![]() |
These have large, powerful magnets |
![]() |
Old ribbon (left) and new one waiting to be soldered. |
The ribbon material in these speakers is stiffer and thicker than one would use in a microphone. The thickest foil I had in stock is 6.5 micrometer thick, supplied by Advent Research Materials, so that is what is going into these. That is about three to four times thicker than would be used in a microphone. The gap is 10mm and I cut the ribbons at 8.6mm, based on measuring a ‘good’ ribbon. Corrugating is routine, but the challenge here is making the electrical connection from the ribbon to the mounts. There are no ribbon clamps but I can see traces of old solder.
![]() |
New ribbon in position. |
![]() |
New ribbon as seen through the horn. |
Further reading.
Reslo Beebs in Recording Magazine
Producer Marc Urselli has written a nice article about his love of ribbon microphones in the October 2022 edition of Recording Magazine.
He discusses several vintage models in his collection, including RCA KU3, Coles, Melodium 42Bs and a nice mention of our upgraded Reslo Beeb ribbon microphones. Here are Marc’s words about the Reslos.
Syncron AU7a phantom power PCBs
Twelve years since first writing about the Syncron AU7a, I can finally offer a neat phantom power conversion. I converted a few of these in the past by hacking the original board or even building a tube circuit, but this is a better, tidier approach. A big thank you to Robert at Russell Technologies for designing boards and a better circuit from my sketches.
![]() |
My Syncron AU7a converted for phantom power |
The Syncron AU7a was one of the earliest transistorised condenser microphones, and was also sold as the Fairchild F-22. It ran on four mercury batteries, which had a tendency to leak after a few decades and are now obsolete. Conversion to run on phantom power seems sensible, but the original circuit used a P-channel JFET and positive ground, which are not compatible with modern phantom power supplies. A new circuit and a new PCB will make things a lot simpler.
![]() |
Syncron AU7a – circuit for P48 operation |
We tried to stay close to the original philosophy, with a single transistor circuit which re-uses the Syncron transformer (above). The Syncron microphones that I have worked on did not use a source resistor bypass cap, but I had much better results with one in place. Dan Zellerman kindly supplied a version of the schematic which shows a 470 pF bypass cap, which was absent from my microphones.
![]() |
New circuit board for Syncron AU7a |
![]() |
Transformer side of the circuit board. |
Some of the clearance is tight and care should be taken to avoid shorting to the ring that surrounds the circuit. And at some point that ring needs to be soldered to ground to ensure good shielding. I used an 80 watt iron on the outside of the ring and fed the solder in from inside. Any flux residue and other crud should be cleaned from the board when all the soldering is done. A drop of glue between the ring and board would also be sensible – be sure to keep the glue away from the high impedance components.
![]() |
New AU7a circuit in place awaiting clean-up. |
The capsule can now carefully be put back in position and connected to the circuit, followed by reassembly of the rest of the microphone. This updated Syncron AU7a sounds very nice and with the new circuit it has a useable output level and the signal to noise is good. The output impedance is approximately 200 ohms with the transformer secondary windings wired in series or 50 ohms if wired in parallel.
![]() |
Inside the AU7a with the new circuit board. |
![]() |
Syncron (green) and Sony C48 (blue) responses compared. |
I can convert your microphone on request. Please get in touch.
Sony Condenser Microphone Evolution – C37, C38, C48 and friends
Sony made a series of excellent large diaphragm condenser microphones, some of which have become studio classics. The earliest production model was the C37A, a tube microphone which may or may not have been used by Frank Sinatra – he has certainly been pictured with one – and it was definitely used to record the voices of Bugs Bunny and Daffy Duck. It has become sufficiently iconic for at least two clones to appear, made by Mojave and Tonelux.
![]() |
On test – Sony C37p, C38b, C48 and C450 |
The C37P is the FET version of the C37, and is claimed to be one of the earliest production transistorised condenser microphones, although that honour is generally given to the Syncron AU7a. The C37p was followed by the C37Fet, and the C38 models. All of these microphones feature an unusual capsule design with an internal vent, which could be moved with a screwdriver from the rear of the microphone, changing the pattern from cardioid to omnidirectional. A very similar capsule is now made by Josephson Engineering, which is used in some of their own models and also rumoured to be supplied to other brands.
![]() |
Sony C37 capsule – front |
![]() |
Sony C37 capsule – rear view |
The later C48 and C800 models use a different dual sided capsule with centre terminals, which looks similar to those used widely by Neumann (and almost everyone else.) The C48 is a versatile microphone with three available patterns, bass cut and pad switches.
Both the C38 and C48 models can run on 9V batteries and use a DC converter inside the microphone to generate the polarisation voltage for the capsule. These converters are tricky to repair when they fail.
Sam Inglis & I recently had an opportunity to compare a few Sony condenser microphones to see how they had evolved over time. On the day of testing we had access to a pair of C37p, one C38b, a C48 and a C450. In addition we looked at a Josephson C705 for comparison.
By comparing the microphones we hope to discover how these Sony LDC mics compare and are the new ones better than the old ones (or vice versa)? Does the capsule hold the key to the Sony sound, if there is indeed such a thing? And are the new capsules from Josephson good copies of the old Sony C37/C38 capsules?
As usual, the frequency sweeps are good for comparison purposes but are run in a small booth and should not be considered absolute measurements. The reference microphone is omnidirectional, which can cause a few inaccuracies when testing cardioid transducers. The dip around 12K is an artefact. Measurements were made at 30 cm distance from a concentric speaker. Measurements were made with a swept sine measurement and recorded using Fuzzmeasure Pro.
1. Comparison of C37p, C38b and C48
![]() |
Comparison of C37p (lowest), C38(middle) and C48 (top) |
As one would expect, the major change between models is the increasing output level (and signal to noise). The C37p is a very early transistorised microphone and transistor technology changed rapidly in those early years. It has a nice sounding bass proximity boost, and the mic is equipped with four EQ settings marked M, M1, V1 and V2 to compensate. (M is the unfiltered output). The two C37s that we tested were very close, which is reassuring.
I own a C38b which I use it for my own recordings, and my perception is of a warm sounding microphone, without a harsh or hyped top end. I was surprised to see that it has a bit more of a top end lift than its predecessor. It carries the M, M1, V1 and V2 settings through from the C37 and also adds a high cut switch. The M1 position acts as a high pass filter whereas the ‘V’ or vocal positions are more like a long shallow shelf.
![]() |
C38b filter – M (red), M1 (blue) and V1 (green) |
And the C48 is louder again. This is a more conventional multi-pattern microphone with electronic switching between cardioid, omni and figure-8. It also has bass cut and pad switches which are accessible via a sprung panel on the rear of the microphone.
In my experience the C48 is a top quality recording tool and makes a good alternative to a U87 – I know a few engineers who prefer it to the Neumann. Barkley McKay at Valleywood Studios said “one of the reasons I like the 48 is it’s gentle roll off before 16k – it’s a little like an enhanced ribbon.“
2. C48 vs C450
![]() |
Sony C450 capsule, front. |
The C450 is a less well known model which looks a lot like the C48 but with some cheesy 1980s stickers applied. However, the C450 has a smaller capsule, around 24mm diameter, and runs on a single 1.5V battery. We have not discussed or measured the C500 here because I don’t have access to one, but I have a hunch that this is a similar size to the capsule in that model. Can anyone confirm that or share a picture of their C500?
![]() |
Sony C450 capsule – rear |
The C450 has an average output level around 11 dB lower than the C48, but is significantly brighter at the top end. It is equipped with high pass filter and -10dB pad switches, although you won’t need the pad very often! The noise level is also a bit disappointing. It probably has a role on the right sound source but I haven’t found it yet.
![]() |
Frequency sweeps of C48 (top) and C450 (bottom) |
3. Does the Josephson C705 sound like a better C37?
![]() |
Josephson C705 in the testing booth at Xaudia |
The Josephson C705 is an excellent microphone with a reassuringly solid feel, and does indeed sound much like a good C37p, albeit 12 dB louder and with an even better improvement in signal to noise. It is a transformerless circuit and is cardioid only (like a lot of C37 and C38 once the capsule becomes stuck!). It lacks the high pass filter options of the Sony microphones. The C705 it is not trying to be a clone or tribute in any kind of cosmetic sense. I admire Josephson because they do their own thing and try to make the best products they can. In this case they have done some clever things with the grill and acoustic environment around the capsule, moving the vertical support struts further back out of the way of the cardioid capsule. At around £2500 this is not a cheap option, but is a professional recording tool which will get you close to the Sony C37 sound.
![]() |
Sony C37p (purple) and Josephson C705 (green) |
One final thought – Whilst doing some background reading for this post, I found that the older Sony mics were not highly regarded on internet forums back in the early 2000s, compared to Neumann and AKG. Here is a certain Mr K,.H.’s informed opinion..
“I never liked the C37A all that much, and would put it into the category “Post War Japan makes good” (as in their tiny late 1950s sports cars patterned after Fiats.) The C37A always struck me as a poor cousin of a ….?? Neumann mic: pretty poor craftsmanship, akin to what the Russians did in the 1970s; not much personality, pretty bad tube choice, cathode follower circuit with its associated gain and dynamic problems, etc… …and then Sony went downhill from there with its FET mics… so I think.”
I disagree. And the first thing I will do when I die and go to heaven or hell or Valhalla will be to march up to Frank Sinatra and ask him if he really did use a C37a!
Electrovoice PL10
The Electrovoice PL10 is a cardioid dynamic microphone which looks very much like a cut down version of the popular RE20. It has no transformer or filter circuit but it still sounds excellent. These omissions presumably kept the price down.
Just like the RE20, the foam that holds the capsule in place can cause trouble. Over time this can degrade into a sticky pulp and then the capsule becomes loose and rattles around and may eventually destroy itself. This microphone needs new foam and a good clean right away!
The microphone body is in three parts – grill, body and base – which are screwed together and some kind of glue applied. I had to heat the threads and apply more force that I would like to break the glue and get the microphone apart. That was the hard part of the job, and once opened it is easy to remove the foam with a bit of isopropyl alcohol. As always, care must be taken around the diaphragm to avoid damage. The metal parts went into the ultrasonic bath and cleaned up nicely.
Once back together, the PL10 is an excellent sounding dynamic microphone. The PL10 should be a cheap alternative to an RE20, but in fact they are scarce, and prices on eBay and Reverb may be higher than an RE20, which is a bit daft.
Here are some comparison frequency sweeps of the two mics conducted at around 25cm from the source (as usual take with a pinch of salt.)
![]() |
Frequency sweeps for RE20 (red) & PL10 (blue) |
AKG D99c manual
Here is the German language manual for the AKG D99c, also known as Harry.
An English translation courtesy of Google…
Our first artificial heads for experimental stereo listening were made in 1949
The Physics Institute of the University of Budapest conducted experimental tests. Many years of well-founded knowledge of the physical and physiological relationships of human hearing and the experience as a specialist company for electroacoustics have enabled us to make a noteworthy contribution to the artificial head stereo microphone, which has become current again, with the series production of a recording head within a short time.
The interest of a large circle of committed tape fans and serious amateurs in an inexpensive one, which has recently been aroused by many press reports and extremely positively rated AKG demonstrations among trade visitors. We can now match the artificial head for stereo recordings with the AKG D99c stereo recording head, which is available now.
The material structure of the head and shape of the ear cups, in conjunction with a simplified but acoustically effective simulation of the ear canals in connection with the two special dynamic transducer systems integrated in the head, are tailored to an optimal recording [which is] analogous to human hearing.
When listening through high-quality headphones – regardless of whether closed or open earphones are used – the listener experiences an intensive acoustic sense of space that cannot be achieved when recording with two individual microphones.
The artificial head as a physical structure itself is above all a prerequisite for the natural occurrence of the factors that determine the spatial impression, such as the difference in intensity, the difference in transit time and the frequency-dependent shadowing effect from one ear to the other.
The AKG D99c stereo recording head, with its optimally designed frequency response (it must be viewed with different criteria than usual microphones), always ensures consistent objective recording properties and can be used as a “double”, so to speak, where you need to keep your own head free for directing.
The stereo artificial head recording is particularly interesting where moving sound events are involved. For example, playing, singing children, lively design of radio plays or reports; also outdoors, for example with passing cars, noises in the background and much more.
A further aspect: when recording conferences, it is easily possible for the listening recording clerk to concentrate on a specific speaker and to record his words due to the acoustic-spatial localisation. The spatially lively playback effect of the AKG stereo recording head D99c can be achieved with any AKG stereo headphones of your choice, regardless of whether the recording comes to the listener live via an amplifier or, as a tape recording, is listened to afterwards.
Technical specifications:
Frequency Range: 50-12500Hz
Sensitivity: 2.0mV/Pa = 0.20mV/ubar/channel
Impedance: 600 ohms per channel
Channel deviation: <3 dB for the entire transmission range
Optimum recording height by using an AKG floor stand.
Harry the Head – modification to condenser mics
The AKG D99C is a binaural dummy head microphone, often known as ‘Harry the Head’ or just plain Harry. Like me, Harry was born in the 1970s and still looks good for his age, albeit with a slightly fuzzy finish (which presumably is to reduce reflections). Inside his head there are two rather basic dynamic microphone which point upwards towards the vents in his ears.Harry may look good but many of his kind sound disappointing and the sensitivity is low. My own D99C sounded particularly poor with a lack of low end response and a sort of crunchy mid range.
![]() |
Harry the Head, or AKG99C to his friends |
And so here is an easy way to improve the sound and sensitivity – fitting two small omnidirectional condenser mics inside will make Harry much more useable. What is more, this modification is completely reversible. You can go back to the former crunchy lo-fi tones or retain the vintage value for a collector in the future.
![]() |
Audio Technica ES945. Remove the grills and mounting nuts |
![]() |
Microphones, cable and aluminium strain relief |
Carefully peel off the base of the head, using a scalpel if needed to remove the glue. You can see two screws that secure the cable strain relief. Undo these. Remove the two circlips which hold the microphones in place. Then pull out the whole assembly of cables and two dynamic microphones.
![]() |
End view of the AKG dynamic mics. |
Undo the three small screws that hold the grill of the boundary mic in place and remove the grill. Also take of the big nut and rubber mounts if they are still attached. The mic is a little too narrow in diameter and I put a layer of heat string around it, but you could use some tape here. This stops the mic from rattling and moving around.
Then fit the cables and push the microphones into the holes in the head. You will notice that the mics are at 90 degrees to the ear-holes.
![]() |
New mic with shrink sleeve and XLR cable attached. |
The next thing to note is that the position of the microphones is critical to the sound. If you push them too deep past the ear vents then the microphone is essentially blocked and sounds tinny and horrible. But too gar below the vent it will sound hollow. I placed them by ear (sorry for the pun), listening as I moved the mics up and down, and settling for an optimum position. just below the ear vent.
![]() |
Approximate position of the microphone inside Harry’s head. |
Once the mics are in position, thread the cables through the channels in the bottom of the head. You can replace the cable clamp if you wish, although that will require unsoldering the cables. (I used a hacksaw here to liberate the cables!). Then stick the base of the mic back on and the job is done. Now it is time to go out and record something.
![]() |
Routing of the XLR wires under Harry |
Personally I think that the AKG D99c, with it’s cubist styling, is the best looking binaural head microphone, although the Neumann KU100 at £6800 GBP must surely be a better microphone!
Whether binaural recordings sound better or worse than spaced pairs or every other kind of stereo recording is a discussion for another day.
* I am sure that other models of boundary mics would work here just as well or better. I can imagine using a couple of Oktava MK012s with omni capsules, or even a pair of 451s if you want to stay with the AKG brand. Perhaps we should consider Harry to be a microphone holder, rather than just a microphone.
Here is the German language manual for Harry, along with a translation (by google, sorry).
You can read more about Harry at Vintage Microphone World.
Update 26 August – this post has been called ‘Sacrilege’ by Heinbach… “I call sacrilege. The grainy tone of Harry is part of its Charm.”
Xaudia Active Dynamic Microphone (ADM)
The ADM is my take on the ‘Speaker as microphone’ concept. You may have come across this idea elsewhere, in certain vintage microphones, perhaps using a larger speaker as a sub-mic for kick drum, or in some boutique models, some of which are a bit low fi, but can be surprisingly good.
A small speaker and a dynamic moving coil microphone operate on the same principles, with the differences being in the details such as mass of the coil and diaphragm. Ideally a speaker should be robust and handle some power, whereas a microphone element might be as light and sensitive as possible. Headphone speakers are generally small and light and can make decent microphones. One classic example is the Beyer M380 which uses the same element as (older) DT770 headphones.
The ADM uses a genuine new-old-stock Sennheiser headphone speaker which sounds very nice when reversed and used as a microphone. Like the Beyer M380, this has a figure-8 pickup which means that it also has a decent proximity effect and good side-rejection. The impedance of this speaker is a little higher than most microphones, and so I have fitted a phantom powered balanced buffer circuit to lower the impedance, reduce the noise floor and increase the common mode rejection, as well as increasing the output level. Overall it works very nicely.
I have a limited supply of parts and so this will inevitably be a limited run.
Further details and sound clips to follow soon. Available from September 2022 at £199 plus postage.
Calrec 6-series Microphone Upgrades
These Calrec small diaphragm condenser microphones have been kicking around in the workshop for several years. They sound nice but the noise floor was always too high to be of much use, and they also need a specific power supply rather than standard 48V phantom. And they are difficult to service because the high impedance section of the circuit board is potted in what looks like epoxy resin – including an electrolytic capacitor. If anything goes bad in there then it is near impossible to replace.
![]() |
Top – New circuit board with spring and locking ring.. |
Swapping the motor in Beyer ribbon microphone.
Beyer sell replacement motors which allow repair of some of their microphones although the cost in the uk is rather high. Swapping the motor is a bit fiddly but can be done with patience and care. This is more or less how I do it, although the models do vary a bit and you may need to improvise.
![]() |
Beyer M160 motor with rounded edges (left). |
First note that Beyer motors may have round or square edges at the rear of the magnets. For many microphones this won’t matter, but the M160 grill will only accept motors with rounded magnets. In the picture above it looks rather crude like it was rasped down with a file! It is probably possible to make a square edged motor fit an M160 but the magnetic filings would surely wreck the ribbon,
Also worth mentioning is that Beyer M160 and 130 have two ribbons whereas M260s have a single ribbon.
To exchange the motor, first one needs to remove the socket and unsolder the connector and transformer. The socket may be glued, screwed and/or pinned in place. Remove the screws or pin. If the socket does not slide out then it is glued and will need heating until the glue fails. Do this at your own risk!
Then unsolder the socket, remove any rubber grommets and unsolder and remove the transformer.
![]() |
Beyer M260 with socket and transformer removed |
The next job is to pull the motor through the acoustic labyrinth but keep in mind that you will need to reverse the process in a few minutes. I usually solder an extra piece of wire into the end of the motor leads which will let me pull the new motor wires back into place.
![]() |
Remember to solder on a guide wire before you remove the motor |
Once this is done you can pull the motor out and then unsolder, leaving the new wire in place.
![]() |
Pull the motor and guide wire through the body |
Unsolder the old motor and then reverse the process. Solder the new motor wires onto the guide wire, pull through the labyrinth and then unsolder. That parts is easier said than done because you are pulling some stiff wires around a bend that you can’t see. Reattach the transformer and socket.
The only job left to do is to check the polarity of everything. Beyer do not always colour code their wires so you have to guess. Compare the microphone to a good modern mic. If your repaired Beyer is out of phase then simply reverse the wires at the XLR or din plug.
As a final warning, I have found that Beyerdynamic parts vary a lot and they do love to glue stuff together – why spend money on a screw or two when a tube of glue will do? Be prepared for a certain amount of frustration and keep the swear-box to hand.
Synchron / Vega S10 Microphones
The Syncron Corporation are generally credited with launching the first transistorised capacitor microphone back in 1964 – the AU-7a, which was priced at $169.50 USD. In their own marketing, the manufacturer claimed to have built “the first microphone to successfully employ the Field Effect Transistor.” At the time, competitors such as Neumann were selling microphones with tube circuits such as the KM64 and U67 which required a separate power supply. The Syncron mics ran on batteries which saved lugging around an extra box and cable. I know we all love and revere the old Neumann tube microphones, but few would argue that they take longer to set up and warm up than a solid state mic.
![]() |
Syncron-Vega S10 microphons |
Following the AU7a, Syncron launched their second and final microphone, which was a rather nice small diaphragm condenser known as the S-10. By this time, the brand was owned by ‘Vega Electronics Corporation’ and had the address on their documents had moved from Connecticut to Santa Clara in California. The price for new microphones was $260.
I was sent three S-10 microphones to clean, service and convert to phantom power for a customer. These mics were badged ‘Vega’./ Like the AU7As, they were designed to run on two obsolete batteries, and so being able to run on standard +48V would be make them much more useable.
![]() |
Vega S-10 original circuit and transformer, |
The mics were a bit of a mess. They had been stored damp at some point and showed corrosion inside and out. I wanted to be sympathetic to the original simple circuit They are a one-transistor circuit with an output transformer, much like a Neumann KM84, and so for the phantom conversion I decided to re-build with a KM84 style circuit, keeping the original transformers.
With a bit of improvisation I was able to rebuild the circuits using circuit boards from Russell Technologies, utilising the space freed by removing the batteries to house the phantom circuit and the transformer. The circuit boards were originally designed as an upgrade for the AKG C480B, and uses a smaller transformer than the Vega. To accommodate the larger transformer I hacked off the end of the board and wired the transformer directly.
![]() |
PCB from Russell Technologies – rear |
![]() |
S-10 with new PCB and transformer in place. |
These microphones used a 4-pin XLR output. The fourth pin was used to make a connection to the battery within the plug of the connecting cable, which means that the batteries would not go flat so long as the microphone was unplugged between sessions. I swapped these for standard 3 pin XLRs of course.
![]() |
Is four better than three? No. |
Although we started with three microphones, one capsule was bad and one transformer was open circuit, so we have two nice condenser microphones, which are well balanced and sound good. The sound is a little less bright and a touch warmer than a KM84. I liked these microphones and was sorry to see them go home.
![]() |
Syncron-Vega S-10 microphones |
Update.
Jason at Crunch studios kindly shared the photo below and sound clip of his Vega S-10 in action.
![]() |
Recording drums with the S-10 at Crunch Studios |
Sound clip of the S10 in action:
You can read more about Syncron microphones at the Coutant website.
Testing the Sennheiser MD409 family
I recently had the opportunity to test a bunch of Sennheiser MD409 and related microphones. These small dynamic microphones command eye-watering prices because they were used by a couple of famous rock bands in the 1970s.
![]() |
Devices under test – five MD409s, BF509, MD609 and another. |
The prices seem high for such a simple device – the microphone consists only of two grills, stem with an XLR socket, frame, and capsule, along with some foam and a couple of screws to hold everything in place. There are no transformers in these microphones, and the output runs straight from the capsule to the XLR socket.
Inside the MD409. Photos by Lester Smith at Abbey Road. |
All of those parts except from the capsule are also found in the current e609 model, which is not revered in the same way and can be found new or used for less than the price of a Shure SM57 .
So the magic must be in that capsule…. right? Similar looking capsules were used in various other Sennheiser and re-branded models, although there can be subtle differences especially in the baffle at the front and the vents in the rear. The 402/3 capsule is often mentioned in internet chat rooms as a close alternative, and so I tested one for comparison, wired into the body of a similar looking Chinese mic.
![]() |
Sennheiser 402/3 capsule |
For the test I had access to five MD409-U3s, one BF509 and one e609, as well as a 403/3 capsule in a replica body.
The questions I wanted to ask are as follows….
Firstly, do MD409s age well and remain consistent? In other words, if we have a conversation about “the 409 sound”, are we even talking about the same sound?
Secondly, is the BF509 really the same microphone?
And thirdly, (for those of us without deep pockets), how close can you get with either an e609 or a reportedly similar alternative like the 402/3 capsule?
Tests were performed in the booth at Extinct Audio, with a swept sine wave method. Here’s what we found.
![]() |
1. Frequency sweeps of five MD409-U3 microphones. |
1. The MD409s are very consistent. We tested five used MD409s and four of them were very close to each other, with a fifth mic showing just a little less bass. The signature sound of these capsules is a 5dB presence bump in the 100 to 200 Hz region, with a dip below 100Hz.
![]() |
2 & 3. MD409, BF509 and e609 microphones compared. |
2. The BF509 sounds similar and the sweep and falls within the range of the five MD409 that we tested.
3. The e609 is another nice microphone but is a little different to its predecessors. It also has a low end bump, a bit broader than the MD409, and has a broad lift around 5KHz. The top end rolls off a bit earlier than the older mics, which you may notice if you haven’t stood in front of a guitar amp for a couple of decades. Your dog will know.
![]() |
4. MD409 compared with a 402/3 capsule |
4. The 402/3 capsule tested lacks the low end bump but shows a very flat response. It is nice but not the same.
In summary, the MD409s were consistent and the BF509 seems to be the same microphone. The e609 is a little different, but with a touch of EQ it makes a good substitute for those who can’t afford the current vintage prices, or who don’t want to take their precious artefact on tour.
Thanks to Sam Inglis for help with this article.
We have a Reverb store!
We have opened a store on Reverb.com for Extinct Audio parts and accessories.
The motivation behind this is the recent changes to import laws from the UK into Europe.
For orders of new goods under €150, we can ship direct without any additional taxes to be paid on import to the EU. The customer still pays the tax but it is collected by Reverb at the point of sale. This means that there are no unexpected bills to pay when you receive the order. Consequently we would encourage our friends in the EU to buy accessories though our Reverb store.
The store sells our thread adapters, transform boxes and splitters.
This only works for lower value orders and so the shop will just be for parts and accessories. If you wish to order Extinct Audio microphones then you will still need to either buy direct from the Extinct Audio web shop, or from one of our international dealers.
Beyer M30 – a super-rare early ribbon microphone
To the best of my knowledge, this M30 is the earliest production model Beyer ribbon microphone. (Do please send me a message if you know of an earlier one). Here it is pictured with a modern M160 for scale.
This microphone came in for repair with most of the original piston ribbon in place. The first thing that leaps out is that, from the outset, Beyer went in their own direction for corrugating the ribbon.
I have heard a couple of suggestions about why this may be. Pistonic ribbons are in theory more efficient as the ribbon moves through the magnetic flux in a flat manner although my own measurements suggest that it only gives a couple of dB at best. Perhaps the most convincing one was Wes Dooley’s suggestion that they were circumventing RCA patents for the more common wiggly ribbons.
The magnetic circuit itself is a work of art, bringing the field from the large block magnet to the sides of the ribbon through four arms. The body of the microphone is chromed brass with one of the most substantial grills that I have ever seen. And the output transformer is a large toroidal type similar to those found in the earliest Oktava microphones and also old Siemens M201 ribbon mics.
I have talked to a lot of customers about this subject and there is a roughly equal split on which type of ribbon sounds ‘better’, with some preferring RCA style and others insisting that pistonic is best. The reader can make their own mind up about that! However, from a technical perspective, I have the equipment to make the wiggly ribbons but not the pistons.
From a historical perpective, it was nice to see the old ribbon. But it was somewhat damaged, a little corroded and stuck to the side of the motor. I took lots of photos and asked Marco, the owner, if he wanted a museum piece or a working microphone. It can be hard to make these decisions but we went ahead and repaired the microphone, which sounds rather lovely with a new ribbon in place.
Thanks to Marco at Vintage Microphone World for sharing his insight, microphones and recordings. His book ‘Witnesses of Words‘ is well worth checking out.
Update 31 July 2022
Thanks to Raphael and Carsten at Echoschall in Germany for sharing this page from an old Beyer catalog. The page shows that the M30 was priced at 700 Deutschmarks which was a lot of money at the time. There was also an M31, which I have never seen. The term “Geschwindigkeitsmikrofon” translates as “velocity microphone“.
B&O BM5 stereo collet repair
This is a really common problem with B&O stereo microphones. They snap in half! At the time of writing I have over ten broken BM5s in my inventory and some repairs for customers, and so clearly something needs to be done.
The rotating mechanisms were (usually*) made from plastic. With time and use, the plastic parts become brittle and the teeth break away. First the mic becomes wobbly and then can break away completely. These parts are also make the top part of the microphone difficult to service because it can be impossible to remove the collet without causing further damage.
And so I commissioned some replacement collets and can now offer repairs for this problem.
The replacement part is machined from brass and won’t break easily. There is some re-wiring to be done. The BM5 used a 9 pin socket which was not easy to replicate. And so we simply run the wires through a hole in the collet and solder together. The socket can get oxidised and noisy anyway, and there is no real need to remove the top part in general use.
Using a brass collet has the additional benefit of making a good electrical contact between the top and bottom mic, which means better grounding.**
Here is the repaired rotating mechanism which should be good for another few decades of use.
Notes.
* Some later BM5s used a different design with steel parts. B&O clearly realised that they had a problem.
Yuchain Wang, musicial and producer from New Taipei City in Taiwan, shared this cover version of Joni Mitchell’s ‘A case of you‘.
The vocals were recorded using an upgraded Lustraphone VR53 ribbon microphone. I fitted the microphone with new ribbon and magnets. The Lustraphones are a bit notorious for having a weak output signal and a very dark tone, but the changes make a big improvement to their usability.
You can read more about the magnet upgrades in a previous post.
Andrew Cadie – Down Where the Drunkards Roll
Melodium 42B replacement magnets
![]() |
Eleven Melodium 42Bs in for service at Xaudia |
![]() |
Replacement magnet assembly for Melodium 42B ribbon microphones |
The horseshoe type magnets found in some of these mics tend to hold their field well and rarely fail. However, I have occasionally encountered examples where the magnets have cracked and lost some of their strength. This may happen if the mounting screws are overtightened or the microphone has been abused.
Around half of the 42Bs use block magnets with a carrier bar to complete the magnetic loop. These are more prone to losing their field especially if they are removed from the microphone for some reason. It is hard to predict how these will behave. Luckily we can measure them and see if they are up to scratch. A healthy microphone should show above 3000 Gauss in the ribbon gap to give good signal to noise performance.
In this example, the field is down to around 2400 Gauss, which is at about 80% of where it should be. That amounts to 2dB loss of output – not yet a disaster but may be heading that way. With the new assembly in place we measure around 6000 Gauss, which is up + 6dB on a ‘good’ stock Melodium 42B.
*Magnet failure is rare. A bad ribbon is the most common cause of a weak signal in these microphones, and would be worthwhile testing the ribbon before embarking on any kind of magnet service.
Sennheiser MD409 foam failure
This seems to be a common issue with old Sennheiser MD409 and similar microphones.
![]() |
Sennheiser MD409 foam failure |
The capsule is held in place by a block of polyurethane foam, which slowly decomposes over the decades, especially if the microphone has been in use in a sweaty rock venue.
![]() |
Sennheiser MD409 new foam |
If left for too long, that capsule will rattle around and there is a risk of more serious damage. the foam can also become sticky and contaminate the capsule diaphragm. If things have not gone too far, it is an easy job to cut some new foam, clean the grills and then the mic is ready for another shift in the studio.
![]() |
MD409 pair with new foam cleaned and ready to rock |
Lustraphone VR53 upgrade
It has been a long time since my last blog post!
This is mainly because the launch of Extinct Audio took up much more of my time and energy than I had ever imagined. But I have missed this blog and will be posting a bit more often in the coming weeks and months. Thanks for your support.
![]() |
Lustraphone VR53 ribbon microphone |
This week I have been working on a few Lustraphone VR53 ribbon microphones. I have never been very enthusiastic about these mics because generally they have a weak output and can sound dark and flabby. Replacing the ribbons and transformers will get the mic so far, but they never quite get up to the performance of other British ribbon mics like the Reslos and Grampians. Which is a shame because they have a unique vintage design and look as though they should be good!
Part of the problem is the magnetic circuit. The two horseshoe magnets provide the field which is conducted (rather inefficiently) around a steel structure to the ribbon. This gives a field around 1500 to 2000 gauss. (For comparison, the field in a healthy Reslo would typically be around 4000 gauss.)
![]() |
Milling the pole pieces to make room for new magnets. |
The steel pole structure is the limiting factor here and so swapping the horseshoe magnets gives only marginal improvements. For this upgrade I made a decision to mill out the pole pieces and fit some strong magnets right next to the ribbon.
The difference is impressive, bringing the field across the ribbon to 6000 gauss, which should provide about +9 to +12dB increase in output voltage. With a new ribbon fitted. the output and signal to noise were improved overall by 20dB. Now it can give the other microphones a good run for their money.
![]() |
Before and after… new magnets and ribbons. |
As an aside, the stock 200 ohm transformer in this example is actually pretty good and don’t need to be replaced. The 30 ohm and high impedance models are not very well suited to a modern studio and in those cases it is worth swapping them out for a more sensible tranny.
You can read my earlier post about the Lustraphone VR53 microphones here.
Xaudia XM10 ribbon microphone (discontinued)
I occasionally get asked about the discontinued XM10 model, usually when one comes up on the second hand market, and so here is a little bit about them. I don’t have any sound clips of the XM10 and it was never sent out for review.
The XM10 was intended to be our budget offering, with the ribbons and transformers made and fitted here at Xaudia, and the bodies made overseas. The transformer is the same as in the BM9, and the ribbon is a little narrower. It has a big bottom end with a large proximity effect,
In the end we only produced a small run of perhaps 20 of the XM10 in 2017 to 2018.
They were excellent at the price point, but in a way not very different from, say, a fully upgraded SE ribbon or something of that class, We won’t do another run as all of our resources were funnelled into starting Extinct Audio as a new business and producing the BM9 family of microphones.
David Broad’s LEM ribbon microphone
I re-built this old LEM ribbon microphone for David, with improved magnets, new ribbon and a medium impedance transformer. You can hear the results on David’s videos.
Reslo Beeb drum recordings by Joe Montague
It’s always great to see and hear how our customers use the microphones we send out.
Joe Montague was kind enough to share these recordings and video of our Reslo Beebs in action. The microphones were set up as a stereo pair in front of the kit.
The recording in the video/sound clips is just the Beebs, no other mics at all, and just a touch of EQ and compression. It is an impressive result from just two microphones. Of course, you need a good kit as well as good microphones, and being a great drummer helps too!
Here are some further sound clips from Joe.
Drum groove 1
Drum groove 2
Drum groove 3
Drum groove 4
Drum groove 5
BM9 Ribbon microphones from Extinct Audio
I haven’t had much time to blog this year, which has been partly due to working hard on a new project. Finally, after years of fixing, testing, upgrading and procrastinating…. Adam and I finally launched our own brand of ribbon microphones.
Introducing the BM9 from Extinct Audio. I have been heavily involved in all stages of the design and manufacture of this baby. It is a general purpose ribbon microphone with a true figure-8 pattern, low noise and a big proximity effect. The aim was to produce an excellent blend of vintage sound and modern utility.
https://xaudia.com/SoundClips/BM9_SmallAcousticStereo.mp3
Electric Guitar
https://xaudia.com/SoundClips/BM9_GretschStrum.wav
https://xaudia.com/SoundClips/BM9_FramusElectric_Vibrato.wav
https://xaudia.com/SoundClips/BM9_FramusElectric_Clean.wav
https://xaudia.com/SoundClips/BM9_FramusElectric_Chorus.wav
Drums
https://xaudia.com/SoundClips/BM9_Drums_OveheadsOnly.wav
https://xaudia.com/SoundClips/BM9_Drums_OveheadsOnly_RollingFloorTom.wav
Update – there are now many much better recordings over at the recordings pages of the Extinct website. But these were the first recordings that Adam and I made with the first production microphones, so let’s leave them here for a little bit of history.
Oktava MK18 vs Russell Technologies Mod
![]() |
Oktava MK18 |
A pair of Oktava MK18 condenser mics have been knocking about the workshop for a few years. Both mics had similar faults, with weird inconsistent dropouts especially when changing patterns. I suspected leakage somewhere but could not track it down. The capsules seemed OK but the mics were unusable as they were, so I put them to one side and waited for inspiration to strike
The MK18 is an ancestor of the MK219, so when I came across some circuit boards from Russell Technologies designed for the MK 219, it looked like the perfect opportunity to revisit and rehabilitate these microphones.
![]() |
Oktava MK219 PCB from Russell Technologies |
The boards are nice quality and arrived with full instructions, which makes assembly very easy – or at least it would be with the intended MK219. In the case of the MK18 there is some hacking to be done.
![]() |
Inside the MK18 – the PCB is smaller than that of the MK219 |
The capsule mount in the MK18 is longer than that in the MK219, so it needed to be chopped, milled and drilled to fit the board. The MK18 also has a 5 pin DIN output, which was drilled out on the lathe with a 19mm bit to make room for an XLR socket.
That done, I discovered that I had lost, sold or binned the original transformers. However, I found a pair of spare BV107s (from Neumann KM84s), which fitted nicely.
![]() |
MK18 with Russell Technologies mod |
I omitted the pad and high pass control switches. And I went for cardioid pattern, using just one side of the MK18s double sided capsule, although it would be easy to wire both sides of the capsule in parallel to have an omni pickup.*
Against the popular tide, I also added a layer of fine stainless mesh, to keep dirt and damp air away from the capsule. These mics are bright enough, so I am happy to risk losing a fraction at the top end.
![]() |
Modified MK18s – ready for overhead action |
The result is good. I like the sound and I think they would make a nice pair of overheads or stereo instrument mics.
*Or even figure-8. I will let the reader think about that one. 😉
More microphone impulse response files!
A bunch of new vintage microphone impulse response files have been uploaded to the MicIRP blog.
These include an RCA KU3a, Gaumont-Kalee 1492 and a bunch of other ribbons, plus some trashy dynamics for fun.
Thes files are for use with convolution reverb plug-ins such as those found in Logic and Pro-tools. I have been using AudioThing’s Fog convolver, which works well.
Melodium 42B nuts and washers now in stock
![]() |
Melodium 42B mounting set |
These replica parts secure the yoke mount to the body of the microphone, and frequently go missing.
![]() |
Meldoium 42B mounting washers |
Please get in touch for more details and prices.
![]() |
Melodium 42B thumb wheels |
Inside a Beyer M130
Reslo Beebs in action with Layla Lane
Pop duo Layla Lane kindly shared their video of their cover of ‘In My Life’ by the Beatles, which which extensively used a Reslo RB microphone with Xaudia’s ‘Beeb’ upgrades.
The guitar, piano and all the vocals were recorded with the Beeb connected into an Ampex 350 preamp and Urei 1176 compressor. You can read more details about the recording at their youtube page.
Layla Lane are Heday Ikumo and Valerie Stern, who together have written music for Coca-Cola and Mello Yello commercials, recorded a song for the Ashton Kutcher film Killers, toured Japan, and produced/wrote songs for big Japanese artists such as Sunplaza Nakano-kun and Yoko Oginome.
Ribbon Mics in Action: Tidal Love by Nothing Places
Thanks to Oswaldo Terrones, who works in Madrid and Barcelona in Spain, for sharing the album Tidal Love by alternative rockers Nothing Places.
Oswaldo made extensive use of ribbon microphones for the recordings, using a B&O BM5 stereo set for the drum room mics, an RCA 74B for guitar cabinets, Coles 4038 as the overhead and Beyer 160s on the lead guitars, percussion, etc. The music itself defies description, but you can listen for yourself at their bandcamp page.
The album was released on Spanish indie label Foehn Records, which champions new artists and “the less traditional facets of pop, rock and electronics.”
Having myself once tried (and failed) to run a little record label, I have the utmost respect for those who have the tireless enthusiasm to make it work!
Witnesses of Words by Marco C. van der Hoeven. (Book Review)
This beautiful book arrived in the post last week. There aren’t enough good books about the history of microphones, so it was a pleasant surprise to discover that Marco van der Hoeven had written this wonderful volume. Marco is a musician, engineer and historian, and he has a very impressive collection of microphones too.
But Marco’s book is much more than a history of the microphones themselves – it is also a potted history of the 20th Century, as witnessed by the microphones of the era. Whenever and wherever a crowd was rallied, a war started or a peace brokered, there was a man or a women addressing the public – with a microphone and some kind of PA system.
A large part of the first half of the book shows how microphones were used by some of history’s heroes and villains – scientists and singers, actors and astronauts, dictators and comedians alike are shown with the current technology.
Marco identifies who used which microphone, and gives little discourses about them and why they did so. Perhaps many readers may already know that Hitler favoured the Neumann bottle-shaped microphones, but here you can also find the microphones used by Mahatma Gandhi, Margaret Thatcher and Marilyn Monroe, amongst many others.
And often the choice of equipment would have made a political statement: for example, Charles de Gaulle is shown addressing a liberated crowd through a Melodium 42B. It was very important for the new leader of a country recently freed from occupation during WW2, to be pictured with a French microphone.
The book is rich in detail, anecdotes and Marco’s unique perspective, showing his passion for the history of recording and broadcast, and a wider view of its global context.
All the microphones shown are part of his own impressive collection, which includes everything from rare examples that would be at home in a museum, through recording studio and broadcast classics, to numerous small, cheap microphones that might have been used for amateur radio, taxi ranks and tape recorders.
This reminds us that most people who needed to communicate did not always need a Neumann or AKG recording classic, and had probably never even heard of them!
The latter pages of the book show numerous, diverse examples, along with various microphone-related paraphernalia such as advertising documents, stamps, toys and record sleeves. It is the combination of the social, historical and technical perspectives that makes this book unique. And it would make a great Christmas present for the microphone lover in your life!
Witnesses of Words is available for €27.95 from WitnessesOfWords.com
Microphones of the Month: Toshiba type A vs RCA PB144 / 44A
![]() |
Toshiba A (left) and RCA PB144 ribbon microphones |
The microphone on the left is generally know in internet-land as the Toshiba ‘Type A’, although it is labelled SN-1631. It is a very close copy of the RCA 44A and its relatives. I have been informed by a Japanese expert that this was made under license by RCA, most likely in the post-WW2 era. Having looked carefully at the Type A and compared it to my own RCA PB144 (right), I have no reason to doubt this assertion.
The mics look similar outside – my PB 144 has a film set style hanger mounting, whist the Toshiba has a simple cast yoke, and the grill hole size differs.
Inside the microphones there are many similarities and few differences. Both use three large horseshoe magnets to provide the magnetic field, and and the ribbon dimensions are very close.
Is the MB301 Cardioid ribbon microphone a Beyer in disguise?
I recently had the opportunity to service a pair of MB301 cardioid ribbon microphones. I had always understood these to be rebranded Beyer M260s with a custom grill, but this is not the case.
The MB301 does use a Beyer pistonic ribbon, but the motor is completely different. The Beyer M260 uses four glued rectangular magnets to make the motor, but the MB301 employs a single large cast ferrous horseshoe magnet. In this respect it looks more like an RCA BK5 or Oktava ML19.
![]() |
MB301 (left) and Beyer M260 (right) |
I think it more likely that the magnet is taken from the Beyer M320 / M360 models, with different pole pieces, although I have not had the chance to compare these on the bench at the same time. Either way, the MB301 is a microphone in its own right, and not a copy of something else.
Despite the ugly oversized grill, they sound pretty good with plenty of top end and bass, and the big magnets give a stronger output signal than the early M260s.
Beebs in action: Aria ca Spira by Cordasicula
Thanks to Saro Tribastone for sharing his band Cordasicula‘s new album Aria ca Spira.
Cordasicula come from south-east Sicily and are inspired by the traditional music of their own island, as well as the southern Italian regions of Calabria, Campania and Puglia.
Saro explained to me that “all these styles, mainly defined by their rhythm, are coming from those areas where 2500 years ago we had Greek people living there, globally known as Magna Grecia (Big Greece).” Their songs are a mixture of original compositions with some traditional tunes, and collectively they have a beautiful, haunting and slightly melancholic quality.
Many of the instruments were recorded with one of our customised Reslo ‘Beeb’ ribbon microphones. The Beeb was used to record the Greek Tzouras, violin, cello, double bass and Battente guitar for the album. For those who like technical details, they were tracked through a DAV BG1 preamp and Mytek Stereo 192 ADC converter. It is nice to hear the Beeb working so well with these traditional acoustic instruments. Here is a photo of the Pier Paolo Alberghini playing double bass, with the Beeb microphone up close to the sound hole.
Marilena Fede’s voice was recorded with an AKG C414B, again using a DAV BG1 preamplifier.
Saro has kindly allowed us to share the Spotify playlist for the album, which should appear below.
Beebs in Action: Majetone calfskin drum heads
I have said many times before that we have fantastic, creative customers, and it is always nice when someone takes the time to share what they are doing. Sometimes their stories are amazing!
Here’s a video clip of James playing his drums and skins, recorded using two of our Reslo ‘Beeb’ microphones as top & side mics in a Glyn Johns arrangement, along with a CAD M179 in cardioid in front of the kick drum.
I think these really do sound fantastic, with a classic yet contemporary tone. I could imagine these sliding very easily into a mix without need for much processing.
Melodium RM6 XLR conversion
Like many old connectors, it is hard to find good quality used Melodium connectors, so here is a nice simple XLR upgrade for a Melodium RM6.
I removed the base of the microphone and cut off the old connector on the lathe. Then I turned a Neutrik XLR socket to fit into its place.
Solder three wires back in place and this RM6 is now ready to record music!
MOTM – Unknown French Broadcast microphone
The Microphone of the Month column has been sadly neglected this year, simply because a record number of mics came in for repair, and it has been a challenge to keep up. But some rare and fascinating microphones have passed through the workshop this summer, amongst them this broadcasting beauty from France.
I don’t know the make or model of this one and it has no markings or badges on the outside or within, but it looks fantastic. The body is made of two cast metal grills, with a cast yoke.
The motor is nicely machined and uses four large wide U-shaped magnets to provide the field through custom pole pieces.
One quirk of the design is that the magnets must be removed to fit the new ribbon. This takes an extra couple of minutes, and on the plus side this means that one’s tools are not pulled by the magnets. Care must be taken to get the magnet polarity right when putting it all back together.
Replacement yoke mount for Western Electric RA-1142
Here is a replacement mount that we made for a Western Electric RA-1142 ribbon microphone.
It consists of a folded steel yoke mated to a brass barrel, threaded for 5/8″ mic stands. The mount works well in practice and looks similar to the original.
Many thanks to Cicely and Darrel at Gearbox Records for the photograph.
If King Midas had a microphone…
Good BBC-Marconi Type-A ribbon microphones are scarce, and perhaps one reason is that too many were decommissioned, mounted and given away as gifts or ornaments, for retirement, achievement and occasionally as trophies.
Melodium 42B Yokes
Xaudia has commissioned a small number of replica yokes for Melodium 42B ribbon microphones.
![]() |
Melodium 42B with new brass yoke |
These are cast from solid brass, using the original 42B yoke as the template. If your Melodium has a cracked or missing yoke, then you need one of these!
![]() |
Melodium 42B yoke |
Stereophonic Star Girl!: Katy Bødtger with her BM3.
Here is an advertisement for B&O equipment, including the BM3 ribbon microphone, which appeared in the Danish publication Se og Hør (See and Hear), 11 December 1959.
Xaudia mount-a-mic in Sound-on-Sound
Our mount-a-mic adapters received a nice review in Sound-on-Sound magazine this month. These little gadgets are designed to make it easy to mount any mic with an XLR fitting. You can read the full article here.
Reslo RV in action – Jose Estragos
Here’s a new video of our friend Jose Estragos from Spain, using his Reslo RVs in his song ‘Buscandote’.
Enjoy!
Repairing an STC 4033 with a cracked casting
The STC 4033 cardioid microphone was a stalwart of British broadcasting and an early solution to the the challenge of making a cardioid directional mic. The 4033 contains both dynamic and ribbon elements, and in cardioid mode the microphone blends the two transducers together via a capacitor and inductor – you can read more about the filter and switching circuit at the wonderful Coutant.org website. The mics are still quite popular with some recording engineers, but of course there are no spare parts available after half a century or so.
![]() |
Omni and Figure 8 suming to a cardioid pattern – from SOS website |
I was recently asked to repair a 4033 with a cracked bottom bell, which is made from some kind of zinc alloy. When I took the microphone apart it became clear that the casting had collapsed into several pieces, only held in place by the rest of the microphone. The job looks like a challenge, and we like a challenge.
It isn’t clear how this became so damaged but it is possible that the alloy itself was at fault. Zinc Pest is a notorious cause of failure caused by impurities in zinc alloys, particularly those from the 1930s and 1940s. Like this one.
The alloy is pretty much impossible to solder or weld back together, and I don’t believe that any glue would be strong enough to hold when the mic is bolted back together. A new part is required but impossible to find, so we need to make one, or at least persuade somebody else to make it. Metal casting requires specialist skills and equipment, so I asked Abbey Casting to copy a good part from another 4033, and they did a fantastic job to produce this part in bronze.
The raw casting needs various holes drilling and tapping, but with a little work we have a perfect fit.
The 4033 is not the easiest thing to work on – everything is tightly packaged and the transformer is set in wax into the stem of the mic, so I had to use a hot air gun to dismantle it. Whilst the mic is apart it makes sense to replace that Hunts capacitor* with a nice NOS Mullard, and re-solder all the old joints to lower noise and improve future reliability.
With the new part in place I can put it all back together again. The casting could be painted or powder-coated to match, but in this case the owner prefers to see the bronze. These are 50 ohm microphones and work nicely with our impedance matching transformer boxes.
Thanks to Liam at ToeRag Studios & Richard at Abbey Casting.
MOTM – Tannoy Ribbon Microphones Part 2. Cardioid ribbons
The internal design of these two microphones is very simple, with a huge heavy horseshoe magnet providing both the magnetic field and creating an internal cavity to help control the pattern. The ribbon pole pieces are simple rectangular steel plates screwed into position.
There is a layer of felt behind the ribbon. I also expected to see the cavity behind the ribbon stuffed with horse-hair or cotton wadding, but in this example it was completely empty. There is a small transformer in the base of the microphone – in this example the output impedance was 2000 ohms, but I’m sure that other output options would have been available.
Despite the size, the output level is rather low.
The motor inside this mic is reminiscent of that from the STC 4104 lip microphone. It uses the same base and connector as the MD422 and MR425 models.
Update March 8th 2015
Tannoy were developing directional ribbon microphones from the mid 1930s onwards. I have never seen this model on the bench, but this sketch appears in Wireless world in September 1937:
Tannoy and the Houses of Parliament
Update March 8th 2015
Thanks to one of our readers for sending in a link to this announcement in Tape Recording magazine (1962, issue 5). This adds to the Houses of Parliament microphone debate.
The article announces two new ‘Slendalyne’ ribbon microphones from Tannoy – a cardioid and a bidirectional version. Yet the cardioid version looks very much like the brass-barrel mic that was supposedly installed into the Houses of Parliament 11 years earlier! This sentence is particularly intriguing: ‘Although they have manufactured microphones for internal use before, this company has never made their instruments available to the public before‘. The statement is not quite true as their earlier models were widely available. But this implies that these specific models had previously been supplied to select customers, and became available widely from 1962 onwards.
Thanks to Tom McCluskie, Jamie Neale of Real World Studios, and Marco van der Hoeven of Vintage Mic World, and everyone else for sharing information and photographs of their microphones.
Tannoy Ribbon Microphones Part 1
Introduction
Update 8th March 2015
Several kind and knowledgable readers have sent in links and articles with dates and model numbers. I have added these where possible. Thanks to all!
Type 1
The BBC technical team reviewed this mic in 1947 and applied their usual exacting standards, rejecting the mic for broadcast use. But as usual the benchmark mic for comparison was the BBC Marconi AX model, which cost many times more, and in fact these mics can sound warm and rich, with an overtly vintage tone.
The Type 1 mic was succeeded by the type 2 or “Pitchfork” model, which is much smaller and has a completely new motor design. This model seems to date from the early 1950s and was available in different colours with different mounting options.
Most of these models have a 600 ohm output, and give a full well balanced sound. This is my favourite figure-8 Tannoy, partly because this was the first Tannoy mic that I owned, but also because it has a good response and a very usable signal / noise output.
The type 2 motor is simple but nicely made, with two tapered magnets either side of the ribbon, and the adjustable pole pieces allow one to set the ribbon tension.
Update – this model has been identified as the MR425, and it was briefly mentioned in Wireless World in May 1952:
The magnets in these mics are made from a ceramic material which allows a smaller, lighter microphone than its predecessors.
Update: This microphone has been identified as the Tannoy Slendalyne model which appeared in Wireless world in June 1962:
In my next post I will describe Tannoy’s cardioid ribbon mics.
Stay tuned!
Very early tube ribbon microphone inspired by the RCA PB17
Ev of Vashion Island sent in these pictures of his wonderful tube ribbon microphone and has kindly agreed to share the photographs and description on this blog. The mic is a little bit of a mystery as it appears to be similar to an early Marconi design and the RCA PB17, yet has no maker’s mark and is different in many details.
The mic is clearly influenced by Harry Olsen’s design as described in his 1932 patent and the magnetic field for the ribbon is provided by an electromagnet, which is very rare and only usually found in the very earliest ribbon mics; this approach became redundant very quickly as strong permanent magnets became available.
As I have not inspected this microphone myself I will use Ev’s description and photographs – Ev’s comments are in italics:
“The outside diameter of the cylinder is 4.75 inches or 210mm. The cylinder is aluminum. the top end cap and plate are machined aluminum. The hemispherical bottom cap is also machined aluminum.
The yoke mount is steel flatbar (I believe the PB17 yoke mount is made of cast metal).
There are three transformers including the one for the electromagnet.
Instead of having three UX864 tubes it uses two unknown tubes, one has 5 pins with a wire attached to the top, and the other is 6 pins.
The resistors are made by Morrill, Germany. The transformers and capacitors have no makers marks that I can see. Whoever made this microphone obviously knew what they were doing. I wonder if this was a prototype made by RCA, or perhaps it is European (because of the German resistors)?
The bell…. is definitely cast aluminum. The inside plate at the connector end of the mic is also cast. The acorn nuts at the connector end fit a 7/16″ SAE wrench perfectly and the bolts with the wing nuts are US threads.
Note the tiny piece of threaded stainless steel pipe bolted to the plate (to the left of the connector in the picture). I thought it might be a jack, but I think it is only a pipe. There is what appears to be a ground wire soldered to it inside the mic.
The number 13 etched beneath the bottom right connector blade corresponds with the number imprinted on the connector itself inside the mic.”
Reslo Beebs in action… again
Here are the Beebs in action as drum overheads, and for recording a string section…
He was using them to record the French band Watine at a country house in Sussex, working out of this amazing airstream mobile studio supplied by Yellow Fish.
We will link to the music as soon as it is published.
Mic of the Month – Shure 508 Stratoliner
Here is our first Microphone of the Month for 2015. This Shure Stratoliner looks like a Zeppelin airship or perhaps Flash Gordon’s space ship. But is it a crystal, ribbon or dynamic microphone?
I had always thought that the Shure Stratoliner series were crystal microphones, and indeed the 708 model does have a crystal element. But although this 508C uses the same body, it is quite a different microphone inside.
This one says ‘dynamic’ on the label but it is really a rather strange ribbon microphone. Here is the business end of the mic with some kind of flat ribbon in place, possibly made from kitchen foil.
Once we remove the ribbon and clean the motor, we can see a series of slots right behind the ribbon. These make an acoustic cavity and help to control the directional pattern.
The motor design is quite basic, with two cylinder magnets behind the ribbon, covered in felt. The transformer is mounted behind the magnets.
This construction and slots behind the ribbon also do odd things to the frequency response. Here is the published response chart from the Shure 508a user manual:
Even the published chart is pretty bumpy, and it seems that Shure were willing to sacrifice fidelity for directionality. And the mic does sounds peaky – definitely one for the vintage / special effects shelf in your microphone locker.
HMV 2350 ribbon microphone documents
These HMV and EMI ribbon microphones show up quite often for repair. The models are identical, just branded differently, and very often they come complete with wooden box, which survives decades in a damp shed or attic better than cardboard.
It is rare to find any paperwork with these but I was lucky enough to come across an HMV 2350 complete with brochure and manual
The manual confirms that they were designed to drive a 20 ohm line. I have found that most of these mics measure around 15 ohms and have really low output. A suitable matching transformer makes a big difference to the usability of these microphones.
PS, some of you might recognise this mic from Marvel’s Captain America movie – it was used by Howard Stark in the scene where Steve gets his treatment!
Review of the Reslo RB by F.C. Judd
Here is a scanned review of the Reslo RB miniature ribbon microphone,
The review is written by Fred C. Judd, who was an early champion of both electronic music and DIY audio electronics. You can hear and buy some of Judd’s creations at this bandcamp page.
This article arrived with a microphone but I am unsure which magazine it was originally published in. Perhaps “Amateur Tape Recording”, of which he was technical editor. If you know more, please let me know.
Shure Unidyne 545 transformer bypass switch mod.
I have read a few posts on internet forums wherein the transformer is removed from Shure mics such as the SM57. This will inevitably reduce the output level and also reduce the impedance to that of the capsule alone, and will of course remove any chance of overloading the transformer! Which means that the result is a quiet mic with low output, perfect for putting close to a drum head.
One of my regular customers asked about making this into a switchable feature. Well why not? With a double-pole double-throw switch it should be possible. The only challenge was finding a switch small enough. In the end, after trying several brands, I found that a spare switch for a Fender Jaguar would fit… but only just!
Firstly the capsule needs to be removed, unsoldered and new wires attached to the capsule. I also ran new wires to the XLR socket to be safe. The mic is filled with quite a lot of sticky brown gunk so that slows down the work.
The trick is to fit the switch from the outside of the microphone, and so the wires need to be fed out through the switch slot. It looks a mess in this state, so they are trimmed back to roughly equal length and soldered to the switch, and it all goes back together. I marked the transformer position with an X. (‘Trans’ in Latin can mean ‘cross’ or ‘across’, and X is a cross!).
Here is my sketch of the circuit, with the capsule on the left and the XLR on the right. Note that the black and white transformer wires are a high impedance winding and are not used in this circuit. Transformer wire colours may vary for other models and examples, and need to be checked before starting work.
The final job is to check the polarity of the mic against a known reference. If it is out of phase then the wires need to be swapped either at the capsule or the XLR socket.
With the transformer bypassed, the mic measures around 15 ohms at 1 Khz. The transformer brings this up to 200 ohms, and increases the output level by 10 to 12 dB. but also introduces a little bass cut. The plot below shows the difference the transformer makes. I am uncertain if the bump at around 800 Hz is real.
With the transformer bypassed, the mic can be placed close to loud sources and there is also a bass proximity effect, so the mic sounds really nice and fat!
Thanks to Lee Mouatt.
Oktava ML16 Manual
2-Track Mind’s Tannoy mic restoration
Here is a nice article by Seth at the 2-Track Mind blog, describing how he restored a very early Tannoy ribbon microphone. Seth went to great lengths, building his own corrugator and refinishing the mic, and the results look great. I played a tiny role here and was able to supply a little brass mount so that he could put it on a stand.
The mic itself is quite unusual, and the motor assembly (above) is different to most of the other Type 1 Tannoy ribbon mics that I have seen. Below is the more usual look of these mics inside, with a large cylindrical magnet and simple flat pole pieces:
Syncron AU7A schematic (again)
Many thanks to Dan Zellman, a former Syncron employee, who sent in this schematic for the AU7A condenser microphone. This was the ‘last issue’ diagram.
![]() |
Syncron AU7A factory schematic |
Mount-a-Mic assembly instructions
![]() |
1. Make sure you have all the parts. |
![]() |
2. Strip and prepare the cable ends ready for soldering. Push through the Mount-a-Mic adapter |
![]() |
3. Solder the female XLR connector. We recommend connecting the barrel lug to pin 1. |
![]() |
4. Fit the plastic strain-relief |
![]() |
5. Slide the metal barrel over the plastic parts |
![]() |
6. Slowly screw the barrel into the adapter, allowing the cable to rotate freely as you go. |
![]() |
7. Fit your choice of connector to the other end, and enjoy! |
Mount-A-Mic adapters from Xaudia
![]() |
Xaudia – Mount-a-Mic assembled cable |
This simple yet cunning gizmo is designed to convert XLR plugs so that they can be screwed onto a 5/8” mic stand.
And a Neumann is no problem!
Here are some assembly instructions for those who wish to make their own cables.
New RCA thread adapters
We have been selling thread adapters for a while but the latest batch are a step up in quality. They are machined from solid brass and have a standard 3/8″ female thread that will fit most modern mic stands. They can also be supplied with 5/8″ on request.
It fits this RCA77B perfectly.
These fit the following microphones….
Most RCA 44, PB140, PB144, 74b, 77B, 77DX, MI-4010-A, BK-11.
Some (but not all) models of the RCA Varacoustic.
Sony C38, C48, FV300, Some C37s.
Many Aiwa, Toshiba and Matsushita ribbon mics
Syncron / Fairchild AU7a
Some older Amperite mics
Please ask about your microphone.
Electrovoice V2 revisited
These old Elctrovoice ribbon mics look great but sadly the sound rarely lives up to expectations.
I have worked on a few of these over the years and there are several things that let these microphones down – happily they can all be sorted out with a bit of thought.
![]() |
EV V2 clamp with through-ribbon bolt! |
Firstly, and perhaps most annoying are the ribbon clamps. EV used thin plastic clamps to insulate the ribbon from the body of the mic, and the ribbon is secured by a central screw that goes straight through the ribbon. The old EV ribbons are quite thick and were supplied with (even thicker) copper end terminals, so that they could just be screwed in place. One problem is that tightening the screw twists the ribbon, pulling it into the side walls of the motor. It also does not make very good electrical contact, especially with a new thin aluminium ribbon. And the clamps are flexible too so the ribbon is not held securely.
![]() |
New ribbon silver clamp |
A better solution is to make new stiff metal clamps. These could be made from plated brass but I tend to use solid sterling silver to avoid the need for a plating process. One clamp must still be insulated from the body of the microphone to avoid shorting out the ribbon.
![]() |
Rusty old magnet. |
The next problem is the weak magnetic field. Replacing the old magnet with a new neodynium one can boost the field around five-fold, which gives a corresponding increase in output. With stronger magnets the steel screws can jump into the ribbon gap and wreck a new ribbon, so it is best to swap the screws out to some brass or stainless ones.
![]() |
EV V2 transformer. |
The old transformers are not great and lack bass but that’s an easy thing to sort out! And finally the old plugs are getting hard to find so we can put an XLR on the rear.
![]() |
XLR fitted to EV ribbon mic |
Voila! With new clamps, ribbon and magnet we have a healthy signal with plenty of bottom end!
The world’s smallest ribbon mic?
Is this the world’s smallest ribbon microphone mechanism?
The tiny transformer is mounted at the other end of the microphone. The mic is clearly designed for close speech and the transformer has a very low inductance (35 µH at 1 kHz), which gives a bass roll off to compensate proximity effect.
Pimp my microphone!
Transformer boxes
They are available in a range of ratios, and our most popular model is the 50 Ω to 600 Ω box, which is ideal for Melodium 42B, STC 4033, and Western Electric / Altec 639 ‘birdcage’ microphones.
These can be supplied to order in almost any required ratio to match your microphone.
Melodium 42B XLR mod
A mount for an STC 4017 dynamic mic
A customer asked me to make a mount for his STC 4017 dynamic mic without modifying the microphone itself. Often these come with a handle or a threaded stud for mounting, but this one came with nothing at all.
My first thought was to make some kind of ring clamp, but that would require a large diameter brass tube and was starting to look quite expensive and bulky. So I came up with this…
It is simply a folded strip of aluminium screwed to a threaded brass cylinder. The bass of the cylinder is threaded to fit a 5/8″ mic stand. The mic slides into a slot in the aluminium and is held by its own ground clamp.
Some shrink sleeve ensures that the signal outputs are not shorted by the new mount.
Voila!
What’s inside a Beyerdynamic M260?
But what are those grey plastic tubes?
B&O BM3 ribbon mic – Black Viking edition!
The Black Viking is Xaudia’s latest take on the B&O BM3. The vikings came from Denmark and invaded our home town of York, so it seems a fitting name for the mic.
This one has new magnets, new ribbon, a 300 ohm output transformer and XLR output connector. Re-finished in a tough black powder-coating, it is ready for a few more decades of action.
More available soon!
MOTM Tannoy MD422 cardioid ribbon mic
Here is Tannoy’s cardioid ribbon microphone – the MD422.
![]() |
Tannoy MD422 ribbon mic, front |
Firstly, Tannoy lose a point for the name. ‘MD’ should surely mean “microphone dynamic” in any sensible society! Perhaps the D stands for “directional”? Who knows, but it puts them at odds with other the Sennheiser MD421, and it is just plain confusing.
![]() |
Tannoy MD422 ribbon mic, rear |
Whatever the D stands for, the mic itself has an industrial look, and this one is finished in a bronze-ish coloured paint. To the best of my knowledge this is the only cardioid ribbon model that Tannoy ever produced, and it uses an acoustic labyrinth to provide the necessary back pressure to the rear of the ribbon. The chamber is the black cylinder in the photo below.
![]() |
Tannoy MD422 ribbon mic, chamber |
![]() |
Tannoy MD422 inside, showing ribbon motor |
The MD422 was subject of a BBC technical report, which concluded:”..this microphone has nothing to commend it for use in the Television Service“. That assessment seems rather harsh, but at the time the Corporation’s selection criteria were flat, uncoloured responses and good signal/noise performance.
In the report, the bi-directional BBC-Marconi AXBT was used as a comparison, which was much more expensive, a different pattern, and therefore a tough benchmark. Cardioid (and non-directional) ribbon mics generally use an acoustic chamber on one side of the ribbon to apply pressure, and this damps the ribbon motion, reducing the output compared with its natural bi-directional response.
Drawing of the Tannoy MD422 from BBC technical document. |
Unlike my mic, the BBC’s example had a yoke mount rather than a fixed base, although there are mounting screw holes in the side of mine.
Despite my irritation with the model number, and the BBCs damning assessment, I like this microphone very much. It has a gentle warm tone. More importantly, it was an attempt at technical innovation, which is always to be celebrated.
Reslo MR1 manual
Here is a scan of a ‘manual’ from 1973 for the Reslo MR1 ribbon microphone, which was the successor to the popular RB model.
I say ‘manual’ – really it is just two sheets of printed A4.
The ultimate guide to ribbon mics – Music Tech mag.
Reslo Dynamic microphones
Reslo are of course best known for their ribbon microphones, particularly the RV and RV models, However, it should not be forgotten that over the decades they made many dynamic microphones, and even some condensers too.
![]() |
Reslo VMC with base station |
The earliest Reslo dynamics seem to be the VMC and VMC2, with the initals standing for Velocity Moving Coil. These had a big heavy permanent magnet and a paper diaphragm, and are really rather lo-fi devices. These two models are more or less the same inside, although the VMC was hard-wired, and the VMC2 had a new grill and an output plug.
![]() |
Reslo VMC2, with output connector. |
In the late 1960s Reslo made a range of more modern light hand-held dynamic mics. The UD1 used a Japanese-made capsule which sounds rather good, of comparable quality to the Shure mics of the era. I have seen transformerless 200 ohm models, and also a dual output 30 & 600 ohm version with a transformer in the body to convert the impedance.
![]() |
Reslo UD1 microphones |
The UD1 was apparently used by Bob Dylan at the 1969 Isle of Wight festival! Here is an advertisement scan from the Reslosound blogspot….
The advertising also mentions a high impedance model, although I haven’t come across one yet.
Some of the UD1 mics were hard-wired to the cable, and it was also supplied with a Reslo connector, and later a 3-pin din plug, with different impedance options available through the different pins. They are wired like this, with one side of the capsule and transformer primary wired to the output socket.
In addition to the UD1, there was a short stubby version that used the same components, and would often have been used with a gooseneck adapter. Pictured below is also a smaller dynamic mic for use with a tie clip.
These models appear to have been replaced in the 1970s by the Reslo Superstar range, which were essentially the UD1 with an updated body and grill. The Superstar was supplied with a DIN plug – I have converted this one to XLR.
![]() |
Reslo Superstar 80 dynamic mic. |
SJT, May 2014
Film Industries M5 dynamic microphone
Film Industries Ltd. are perhaps best known for their M8 ribbon microphone, but what about models M1 to M7? Well, here is 14.286 % of the answer: the M5 moving coil microphone.
This model was likely to be a competitor to the Reslosound VMC, and like the Reslo, the M5 features a paper diaphragm driving a moving coil in a magnetic field. The output is wired to a pair of screw terminals, for easy wiring without the need for a custom connector. It does not have a separate ground connection.
The large black rubber cylinder at the base is supposed to give some vibration damping, although perhaps not enough to make a major difference.
Although a 30 ohm mic, this one at least has a strong output, due to the large strong magnets.
And here’s a somewhat wiggly frequency sweep of the mic:
Reslo Beeb Commando!
Like all of our ‘Beeb’ mics, this features an upgraded 300 ohm output transformer, new ribbon and XLR socket. This special edition as well as a switchable high pass filter inductor to balance the proximity effect when used close to sources.
The custom camouflage colours makes it suitable for undercover operations, and even better for guitars and drums!
MOTM: Reslo NC-RB Lip microphone
Our Microphone of the Month for April is this rare oddball from Reslosound: the NC-RB.
This was Reslo’s attempt at a commentator’s lip microphone, and appears to be cobbled together from spare RB parts. The upper body and head are from an RB, but the head is rotated through 90 degrees and screwed to another chopped-down head. The lower body-stroke-handle is a straight aluminium tube with a switch which terminates in a normal Reslo output socket.
Inside the head is a rotated RB-style motor. The magnets face the speaker, to provide some pop protection for the ribbon at the rear.
Behind the ribbon I found this metal baffle, which should control the pickup pattern and tweak the frequency response. There is also fibre glass and felt wadding for more protection.
Overall it is a strange little mic. The ribbon runs horizontally, which is generally considered a bad plan as, if it sags, it will droop into the metal pole pieces. They must have been a way of producing a lip mic without the expense of re-tooling for a completely new design. I have only ever seen this one, although I know of a customer who owns another.
What does NC stand for? “Not a Coles”, perhaps?
RCA 77DX user manual
B&O BM5 and BM6 magnet upgrades
A while ago, I blogged about some magnet upgrades for the B&O BM3 and BM4 ribbon mics that greatly improve the signal-to-noise performance of the mics. We have similar magnet upgrades for the later BM5 and BM6 models.
Dirk at V76 Studios in Hamburg was kind enough to share some sound files of his BM5 stereo set, recorded before and after we fitted new magnets and ribbons. Here they are…
‘Blackbird’ recorded with his stock BM5, before the modifications
Download file
‘Blackbird’ recorded with the upgraded BM5, with new magnets and ribbons
These are Dirk’s impressions of his recordings…
“The difference is amazing. The mic sounds awesome now. It’s about 10-12 db louder (needing only 52 db for the front for finger picking now) and it has got much more treble and presence. Still it sounds smooth and wonderful rich, without losing the transients. This mic is killer for acoustic guitar now, and also as a room mic. I also compared it to my modified RB500 Mics (with cinemag 9888 Transformers) and the BM5 now has 6 db more output and is sounding so much better. Also the Beyer M130 doesn’t match it by far, IMHO.
“Both were recorded with the BM5 (60 degree angle pointing towards neck and bridge) into a TRP Ribbon Mic Pre direct into RME Converter into my DAW. No lowcut. The older recording would have been 10-12 db lower with the same TRP-Gain. For a better comparison, I choose to normalize both files. Still the new one sounds louder, brighter and more detailed. The noise floor of the older recording is clearly audible, and unnoticable with the new one – due to the 12 db more output of the mic.”
Update 21 Feb 2015.
Here are some comments from Andy at Superfly Studios in Nottinghamshire, UK, about his B&O BM5 with magnet upgrades and new ribbons.
“I’m so happy with these microphones. They have been absolutely fab to use over the past few days.
First session in was an acoustic folk duo, I used the B&O BM5 on one of the guitars and it just sat straight into the mix and sounded great. Picked up all the detail of his picking and sounded nice and rounded on the full-on sections. Just the right amount of highs for my taste as well, I normally use a 414 for acoustic and cut some of the top end, but I’ve got a new favourite now.
Also used the B&O for the drums today and it sounded great in the room, I love using room mics on drums and had the beeb reslo’s as a spaced pair about 8 ft away (10ft apart). Seems to always do the trick in the live room and the B&O just in front of the kit at waist hight. Sounded fantastic lovely sustain to the cymbals and picked up the natural ambience of the room.”
MOTM: Gaumont-Kalee Type 1492 ribbon mic
This month’s MOTM is the Gaumont-Kalee model 1492,
Inside, the mic is a fairly conventional figure-8 ribbon mic, but has added baffles both sides of the ribbon, and thick wires run from the top ribbon clamp, giving some blast protection along the way.
Lustraphone Lustrette – dynamic mic
Here is a little Lustrette LD/61 – a charming little egg-shaped desk microphone by Lustraphone.
I picked this one up with a couple of crystal microphones, and for a long time I had wrongly assumed this to be a crystal too. But when I opened it up I found a dynamic capsule and step-up transformer. I should have guessed from the model number – ‘D’ usually means dynamic. In fact it features in a Lustraphone product catalogue that I posted earlier – so I have no excuses!
![]() |
Lustraphone LD/61 inside |
The mic comes in a stylish box, with a picture of the mic, so you know what you’re getting.
The dynamic element looks similar to the one found in the more common C51 model, and it is possibly the same mic in a different package.
…I’m gonna take my Ribbon to the United Nations….
Back in 1954, Bang and Olufsen BM3 ribbon mics were installed in the United Nations building in New York . The mics were chosen for their lack of feedback, and are clearly visible in these video clips of Lester Pearson speaking about the Suez crisis.
![]() |
Lester Pearson speaks into two B&O mics at the UN |
B&O were justifiably proud of their mics being chosen for the UN – here is a document from the time…
And a translation from the Danish….
“As we previously mentioned to you, we have received a message from our US representative, Fenton in NY, that the UN uses our BM3 microphones throughout the UN building in NY. They chose the B&O mic and an American mic because only they, out of several hundred different manufacturer products that were tested, did not give rise to any acoustic feedback in the several hundred loudspeakers that are mounted in the ceiling of the UN general assembly building. Our mic also had an advantage over the US product as it didn’t hide the speaker’s face, which is important with regards to film and TV reporting. The microphones have been in use in the UN since 1st October this year. The newspaper INFORMATION recently had an article with a picture that depicted the Canadian foreign minister , Lester B. Pearson , at the podium in front of B&O microphones when he presented his suggestion for involvement in Egypt. Via our advertising bureau we managed to send out a press release under the title “Danish microphones at the UN podium”, and a whole selection of magazines included the picture and advertisement. We have attached the picture for your information – Next time you see the program AKTUELT in TV with recordings from the UN building, take note of our microphones, they are clearly visible.
“Our American representative has also undertaken an investigation that shows B&O micophones are used at, amongst others:
[Mercury, ABC and Decca]
“We have large orders from Fenton conmpany for microphones and pick-up units, and the advertising that Fenton performs in the American technical journals has the effect that we receive requests from other countries. This has resulted in that we have recently sent 10 samples to Australia and samples to Hong Kong, and other countries are also showing interest.
“Likewise we have significant orders for AC motors from Norway, where we compete with German and English manufacturers, and samples of this product has been sent to other countries.
30th Nov. 1956
100,000 blog views
Bang and Olufsen BM5 grounding issue
Some Bang and Oulfsen BM5 stereo ribbon microphones are prone to hum on one channel. This is because the top half of the mic rotates around a plastic collet ring, but is only grounded through contact to the lower half of the metal body. With time and use, the contact between the two halves becomes loose, and the upper body is no longer grounded properly.
![]() |
B&O BM5 stereo mic |
The problem only occurs with early versions of the mic. Later, B&O recognised the problem and re-designed the mic’s rotating ring giving it an additional metal lip, so that the upper mic rotates around metal, ensuring good grounding contact at all times.
If you have a an early mic, in most cases the hum issue can remedied by improving contact between the parts as follows. Here are some tips, but remember that there is a delicate ribbon inside, so go slowly and if in doubt send it to someone more experienced!
1. Carefully remove the top half of the mic, and loosen the two grub screws at the base with a screwdriver of the correct size. Don’t lose these little screws – if you do then they are M2 thread!
2. Slide off the ring and put the rest of the mic somewhere safe.
3. Flip the ring over and rub over some fine abrasive paper to remove any dirt and oxidation.
4. Gently run the fine abrasive paper around the bottom of the metal tube that will make contact with the lower ring.
5. Replace the lower ring and tighten the screws, making sure that the metal parts are properly aligned and make good contact. You want a close fit between the tube and ring.
6. If that doesn’t work, addition of a strip of copper tape to the plastic collet can improve the electrical contact between the two parts. The tape will eventually wear out if the mic is constantly rotated, but many users tend to keep the same angle for most applications.
SJT, Feb 2014
This is what happens…
RCA 74A and 74B ribbon microphones
Happy 2014!
Here is a lovely pair of RCA junior velocity ribbon microphones awaiting service, a 74A and a 74B. We see a lot of ‘B’ models, but the earlier 74A (left) is quite rare by comparison.
![]() |
RCA 74A (left) and 74B |
Externally, the mics are similar in size and shape, but the 74A has a yoke mount and looks more like a baby 44BX, whereas the 74B has a fixed or swivel mount at the base of the mic. The ‘A’ model also has larger grill holes.
![]() |
RCA 74A (left) and 74B ribbon mics inside |
Inside, the ribbon motor assembly is the same although the mounting arrangements differ. The 74A motor (left) is screwed directly to the frame, whereas the ‘B’ is suspended by four small rubber mounts. The yoke would absorb some vibrations transmitted through the mic stand, and so the rubber parts were possibly introduced to compensate for the loss of the yoke. The earlier transformer has two outputs at 50 and 250 ohms, whereas the 74B transformer also has a high impedance output for public address use.
One can only guess about the reasons for the evolution from ‘A’ to ‘B’ models, but these things usually comes down to performance and economics, with fashion and marketing also playing a part. Losing the yoke might reduce costs, but adding the suspension and the swivel joint would probably balance this, so it is hard to tell.
Both mics need new ribbons!
The amazing Coutant website has a scan of a data sheet for the 74A.
Ribbon mics in action
I am lucky to have many great customers, and some are kind enough to take the time to share their music and other projects. It is always gratifying to see how these mics are used once they go back out into the ‘wild’.
Hewdie is a long-standing customer who was kind enough to send in a copy of his excellent new album. I have serviced many of his ribbon mics over the years and these feature extensively on the recordings – including a B&O BM3, RCA 74B, Lustraphone VR53 and a couple of Beeb Reslos. The album is well worth a listen.
Andy Wright used his Beeb Reslos to record The Kimpton Players in their radio play production of Noel Coward’s “Brief Encounter”. Here is a photo of the Beebs in action…
And here’s how the drums sounded in the final track Stay by Free Manhattan
Have a great Christmas & New year – and good luck with all of your holiday projects.
Stewart
Xaudia
‘The Beeb’ Reslos – also in black!
This batch now have their own metal badge, which looks great. In addition to the usual chrome and hammertone mics, we also have some rather smart looking black microphones, which have a tough powder-coating finish.
The sound is still the same 🙂
I thought this was a switch… but it isn’t!
I had expected the red thing on the rear of this Amperite RB ribbon mic to be a simple on-off switch:
![]() |
Amperite RB – switch on rear |
![]() |
Inside the Amperite – sliding plate, blurry photo 🙁 |
When open, the mic will be a normal figure-8 pattern. Closing the vent will reduce pickup at the rear, and also make the mic sound brighter by reducing the proximity effect.
![]() |
Open and…. |
![]() |
… closed |
The mechanism is not as sophisticated as, for example, an RCA 77DX, but at least they made an early effort to offer engineers a new flavour.
Well done Amperite!
MOTM – Melodium RM6
To remove the mic completely, the connector must be unsoldered and the switch tip removed. Once inside, we see something that looks like the Easter Island statues!
The ribbon is hiding behind the baffles, and the motor requires quite a lot of disassembly before the ribbon can be accessed. The ribbon itself is about 1.8 mm wide, so a bit fiddly to fit. Like most mics of a certain age, half the problem is that the ribbon has become oxidised and stiff, and the other half is small particles of wild iron that that have become stuck between the pole pieces, preventing the ribbon from moving freely.
Removing the strong magnets made cleaning and re-ribboning a lot easier! The transformer and filter inductor are housed in a mumetal can, screwed beneath the motor assembly and above the filter switch.
As usual, the mic sounds best without the high pass filter engaged, although I can imagine it being useful to compensate for proximity effect when close micing some instruments.
There doesn’t seem to be much information about this mic available on-line, but I have scanned an old Melodium catalog featuring the RM6. There is also a French language review of the RM6 over at Audio Fanzine. They seemed to like it, and gave the mic 9 out of 10!
The Dead Zone….
Here is some amusing copy from the box of a Grundig GRM1, a.k.a. Lustraphone VR53. Above the nice diagram of the the figure 8 pattern, it proudly states “There is virtually no sensitivity at right angles to the microphone front, and this we call the “Dead Zone”. Now we know what to call it!
The Xaudia blog has also been a bit of a dead zone in recent weeks, due to lots of repair work coming in. Things are getting back under control, so more microphone related posts and info will be coming soon!
Lustraphone desk mic or speaker?
This was sold as a desk microphone, but it may actually be a small speaker. Or both! It looks very stylish, with tolex covering and brushed nickel finish.
The ‘device’ measures 600 ohms at 1KHz, and 50 ohms at 100 Hz. Inside, the dynamic element looks more like a small speaker than a mic element, although of course the two things are fundamentally the same technology. When wired as a mic it is pretty lo-fi with a narrow bandwidth. And it does transmit as a speaker too. My guess is that it was part of an intercom system and serves both purposes.
Whatever the intended purpose, one can easily imagine this on a gentleman’s desk, so that he could talk to his secretary whilst smoking a pipe and considering important, worldly matters… like this chap!
Microphone Impluse-Response Project (MicIRP)
I have created a new blog called MicIRP, which is a contraction of The Microphone Impulse-Response Project.
MicIRP will run in parallel to the Xaudia microphone blog, and aims to share impulse-response (IR) data from the many interesting old mics from our own collection and that come in for repair
The IR files can be used with convolution reverb programmes or plug-ins such as TL Space or Waves IR1 to simulate the sonic characteristics of the microphones. So they can be considered as filters or tiny spaces to modify your sound.
I have uploaded files for about 35 microphone to get things started, and will be adding many more mics as and when the opportunity arises.
And it is all completely free so have fun!
Stewart
Cadenza microphone patent
Here is a UK patent by Eric Thompson of Simon Equipment Ltd, from 1959, that relates to the Cadenza ribbon microphone: Cadenza Patent
![]() |
Drawing from patent for Cadenza microphone |
The novelty in this patent is that the ribbon is fixed in the middle and clamped at either end. The inventors claim that this allows the two halves of the ribbon to be tuned to slightly different frequencies to give a flatter overall frequency response. I had suspected this for some time, but had never seen it written down! It also has the advantage of supporting the ribbon and giving it some protection against stretching. And here is a photo of the design in real life, from an earlier post.
Upgrades for B&O microphones.
![]() |
Bang and Olufsen BM3 ribbon mic |
Regular readers will be aware that I am a big fan of B&O microphones, and have serviced quite a few of them over the years. Whilst these mics are stylish and look great, the output levels can often be disappointing, restricting use to sources like guitar amps and drums. The low sensitivity is usually due to weak magnets and the fact that the early microphones have an output impedance of 50 ohms – an older standard. With some work we can make these handsome microphones sound as good as they look.
![]() |
B&O BM3 deconstructed |
Firstly, a replacement transformer can be used to convert the microphone’s output impedance. The stock transformer in the early BM2 and BM3 microphones has a ratio of about 1:20, and with the thick wide ribbon gives an output impedance of 50 ohms. Switching to a 1:40 transformer will give an increase of 6dB and raise the impedance to about 200 ohms – Xaudia make such a replacement. With a thinner and lighter replacement ribbon, the output and impedance will both be a little higher.
![]() |
New magnets! |
We also commissioned a batch of custom magnets for BM2, BM3 and BM4 microphones* which greatly increase the magnetic field, and therefore the output level. The magnets in an old BM3 typically have a field strength of 1000 to 1600 Gauss, whereas the replacements give a field of around 6500 gauss – a three or even four fold increase in magnetic field strength, which translates, at least in theory, to a 9dB to 12dB increase in output.
Here are some frequency response plots from three B&O BM3 microphones.
![]() |
B&O BM3 with new ribbon (blue), new transformer (green), and new magnets (red) |
Red = new ribbon, upgrade transformer, new magnets.
Green = new ribbon, upgrade transformer, stock magnets
Blue = new ribbon, stock transformer, stock magnets.
With the full upgrade, the output level is raised by about +18dB, which transforms the mic into a much more versatile recording tool that can be used for acoustic instruments as well as the usual louder sources. If your B&O mic needs a new ribbon, then it is well worth considering a magnet and transformer upgrade at the same time.
*We have similar magnet upgrades for the BM5 and BM6 mics.
Reslosound VMC2 Velocity Moving Coil
![]() |
Reslosound VMC2 |
![]() |
Reslosound VMC2 |
The badge proudly declares that this specimen is a low impedance 15 ohm model.
Reslosound used a fibrous paper to manufacture the diaphragm, and the coil is simply glued to the paper tube at the rear. In fact the technology looks very similar to early speakers.
When I plugged it in, the mic gave a very lo-fi sound – even more distorted than one would expected for this era. On investigation, there were some metallic particles sticking to the diaphragm, preventing it from moving freely. The paper cone had also become detached from the diaphragm.
![]() |
Diaphragm from a Reslo VMC2 |
![]() |
Reslosound VMC2 magnets |
In use, the mic is slightly boxy sounding, with a steep roll off at the bottom end and some dramatic peaks and dips in the response. It very obviously sounds like an early dynamic mic!
![]() |
Reslo VMC with base station |
For comparison, here is a Reslo VMC with announcer’s base station. Note the difference in the grill, with five horizontal slats, as opposed to three vertical.
Reslo microphones in disguise
This one is labelled RVH – the ‘H’ means high impedance output.
I have also seen and serviced RV models with a Philips badge.
![]() |
VOX badged Reslo RB |
The common Reslo RB models were also sold under the VOX and GEC brands. This Vox mic is identical to the Reslo badged model, apart from the badge.
![]() |
GEC badged Reslo RB |
The GEC mics are painted black and given the model number BCS 2378, but it is simply a Reslo
RBS.
A few thoughts about ribbon mic transformers… part 1
![]() |
Film industries ribbon mics |
When describing ribbon mics on this blog, I often note the output impedance of the mic, and possibly the transformer ratio too. Occasionally I receive messages asking how the impedance relates to output level, so here I will try to outline the role that the transformer plays in a ribbon mic. A ribbon mics is a very simple device, and if we consider how it works we will see just how important the transformer is.
In the beginning…. Let there be mics!
![]() |
Tannoy mic – ribbon, magnets and transformer |
In the early days of sound recording with ribbon mics, the destination would usually have been a tape recorder of some kind, with a tube preamplifier to receive and boost the signal from the microphone.
The mic could be connected in two ways: the budget option would be a high impedance connection using an unbalanced screened cable through a capacitor and straight to the tube grid, just like a guitar! The drawback is that unbalanced, high impedance connections are prone to picking up noise, and parasitic capacitance will limit the length of cable that can be used before the higher frequencies become significantly attenuated.
![]() |
Film Industries transformer dissected |
This Is The Modern World
Over the decades, broadcast and recording equipment has become more standardised, and most modern mixing desks and dedicated mic preamps are made to work well with microphones of up to around 600 ohms.
Ribbon microphones tend to have low outputs compared to modern dynamic and condenser mics, so it is advantageous to squeeze out as much level as we can. So, let’s go back to the transformer in our imaginary ribbon mic and re-design it for use in the today’s recording environment. We can keep the same primary winding, but change the secondary winding to one with a higher turns ratio.
![]() |
Xaudia ribbon mic transformers being assembled |
Let’s make it a 1:32 transformer, so now we need to take our 0.3 ohms from the ribbon and primary winding and multiply it by 32 squared, which gives 307 ohms. Once again we need to add the resistance from the secondary winding – in this case the wire is not only longer from the extra number of turns, and also will be thinner because we have squeezed the extra turns into the same space. A typical value would be 20 ohms, which would give us 327 ohms altogether, which most modern preamps can cope with quite happily.
Our output level will now be 32 mV, or 30dB gain with respect to 1 mV. So we have an improvement of +10dB over the 32 ohm transformer.
No Free Lunch
In life, and in physics, we know that you don’t get something for nothing. So are there any drawbacks with increasing the ratio. The higher impedance can increase the resistance noise, so it is important to make sure that the transformer is well designed with a very low DC resistance, particularly for the primary winding. However, the extra 10dB could be the difference between asking 50 dB gain from the preamp, or cranking it up 60 dB gain, where many preamps are becoming noisy.
Ancient and Modern
In most cases, it is worth getting the transformer right and demanding a bit less from the preamp. With vintage ribbon microphones it is very often possible to re-wind the original transformer to a higher ratio to get more output from the microphone. If the original laminations and winding style is used, the vintage tone of the mic can be retained, and overall this can give a stronger signal and a better signal-to-noise ratio into modern equipment.
![]() |
Vintage Ferrograph and Wearite matching transformers |
Another option is to use an impedance matching transformer. Back in the 1950s and 60s, most manufacturers of ribbon mics sold transformers to solve all kinds of matching problems. One example is this line matching transformer from Reslo, which connects a low impedance mic to a high impedance tape recorder. Xaudia make impedance matching transformer boxes with XLR fittings to do exactly the same job in a modern studio.
In part 2 of these ramblings I will discuss the effects of the transformer’s inductance and resistance characteristics.
Xaudia P90 Hexapups
Xaudia now make P90 shaped hexaphonic guitar pickups!
![]() |
P90 sized hexapup stereo pickup, installed in a Fender guitar. |
Something old and something new – STC Coles 4038 and 4050
A good customer brought in his Coles 4050 stereo microphone for show-and-tell, which gave us a good opportunity to compare and contrast with some of the STC-Coles mics from the past.
![]() |
STC4033, 4038 and Coles 4050 microphones |
![]() |
Frequency sweeps of 4050 (top, red & yellow) and 4038 (bottom red) |
We ran a frequency plot of both halves of the 4050, and of the 4038.* Both mics sound very good, and although the old 4038 had a smoother top end roll off, the 4050 had an extended about +6 dB higher output and an extended frequency response. We were also very impressed with how well matched the two 4050 ribbons were – less than ±0.5dB across the range, and mostly much better than that.
The 4038 is prettier though!
* Taken at 30 cm distance. Please note that some of the bumps are due to our test chamber – there are issues with calibration when comparing a figure 8 ribbon with an omnidirection reference mic.
Thanks to John Gooding
Fi-Cord FC1200A tube microphone
This nice Fi-Cord 1200A tube microphone arrived without a power supply… so we built a new one!
The problem with these mics is that they are filled with resin, and it is almost impossible to get inside them. The mic has a Nuvista tube (like the AKG C28c) somewhere deep inside. Thankfully this one was working well so it just needed a new cable and an Xaudia custom power supply….
These mics were designed and built by Calrec, so it should be no surprise that they sound really good! There is a bit more information about Calrec Fi-Cord mics at Saturn Sound.
Thanks to Santiago Ramos
BBC-Marconi Ribbon Microphone Type B
Our microphone of the month for September is this a rare and lovely BBC-Marconi ‘type B’ ribbon microphone. The type B is closely related to the ‘A’ series of mics (AX, AXB and AXBT) which were made from around 1935 onwards. The model B was made from 1937 onwards and used the same motor assembly, but with a smaller (yet still massive) magnet and without the ribbon tension adjustment facility.
![]() |
BBC Marconi type B, side view |
The smaller magnet format allowed the mic to be packaged into a smaller cylindrical body, and these were apparently were often used for outside broadcast, attached to the chest of the broadcaster! One would have to be pretty strong to carry that around all day.
Although this is widely know as the model ‘B’, the nameplate calls it 8559A.
![]() |
BBC Marconi type B badge |
As well as the outer grill, there are two extra windshields inside the mic, which would have protected the ribbon from wind blasts and dirt. These windshields did their job well – in this example, the ribbon is unbroken, but this has oxidised and stiffened over the years and will need to be replaced.
![]() |
BBC Marconi type B ribbon motor |
The magnet and motor assembly are held in place with foam rubber, which has mostly survived the years. The output transformer is hidden behind the magnet. This had a break in the secondary winding, but luckily I was able to unwind it by a single turn and bring the mic back to life.
![]() |
BBC Marconi type B, transformer |
At the rear of the mic, connection to the outside world is made by three screw terminals, and square bulge at the bottom shows the location of the transformer.
![]() |
BBC-Marconi ribbon mic, rear |
Overall, the mic sounds warm and rich, although the metal can gives it a certain ‘boxy’ sound that instantly defines it as a very old microphone!
There is some more info about the BBC-Marconi ribbon mics at the Coutant and Orbem websites.
Thanks to Tom Barwood
The Americans are coming
Here is a trio of American model R331 ribbon mics…
![]() |
American R331 microphones |
![]() |
Is this the DeLorean of microphones? No. |
![]() |
Impedance settings for the R331 |
![]() |
American R331 ribbon motor assembly |
There is a lot more information about the R331, DR330 and DR332 at Coutant.org
Thanks to Myles Davis
Lustraphone Badges in stock!
I see a lot of Lustraphone VR53 mics around that have lost their original badges – like the ones on the left and right. The glue that was used wasn’t great, and they look rather sad without their original nameplate.
![]() |
Replacement Lustraphone badge |
I am delighted to say that we have just taken delivery of some replacement badges for these that look absolutely fabulous. They have a silver logo on a vintage cream background, just like the originals.
![]() |
Lustraphone VR53 with new badge! |
They of course also fit the Grundig, Pamphonic and Mimco badged versions of the VR53, and also some of the small Lustraphone dynamics too.
![]() |
Lustraphone dynamic with new badge! |
The badges are £5 each plus post from the Xaudia website.
(Thanks to Best Badges for their excellent service!)
Ervox R58 – French ribbon mic
Today on the bench we have an unusual microphone from France. I have never heard of this brand!
![]() |
Ervox R58 ribbon mic |
The Ervox R58 is a high impedance ribbon microphone designed for public address or home taping to a reel-to-reel recorder. It is made from a two part cast body, perhaps inspired by the RCA Varacoustic, and is nicely finished in hammertone paint. Paint still covers two of the screws, so I can see that I am the first person to look inside this one, which is always a nice feeling, like unwrapping a present!
![]() |
Ervox R58, rear |
Inside the mic everything looks nice and clean. The motor is built around a sturdy block of clear plastic with a large horseshoe magnet to the rear, and the ribbon itself is a piston-style design similar to those found in B&O and Altec microphones.
![]() |
Inside the Ervox R58 |
Unfortunately the transformer is not working properly – the inductance measures only 14 microhenries, which for an (estimated) 0.2 ohm ribbon would make a HPF filter at around 2KHz… I’m sure it can’t have been designed like that, so one suspects either insulation breakdown and a short, or the laminations have deteriorated with age and lost some permeability.
![]() |
Ervox ribbon motor assembly |
I’m not sure if it is worth the effort of re-winding this one, particularly if the lams are below spec. Luckily we can make a new low impedance tranny for it and bring it back to life.
The previous owner kindly included this scan of a wiring diagram for the mic.
Beebs to Belgium!
We have just shipped this rather lovely set of Reslo microphones to Thomas at Le Lupanar Studios in Belgium. He will be recording a brass section with two of our ‘Beeb’ Reslos, and a pair of upgraded cardioid Reslo CR mics on goosenecks.
His studio is still under construction but Thomas has been making a photo diary of the project – from the pictures so far it will be an amazing facility in a great location! How’s this for soundproofing…
Good luck with the building, and we will watch with interest as it all comes together.
🙂
Reslo Beebs in Organ Action
![]() |
Reslos at St Peter and St Paul Church, Kimpton |
He kindly sent in this brilliant photo, and an .mp3 file too so that we can hear how it sounds!
Organ recording with Beeb Reslos – Andy Wright.
The recording was made with the mics plugged straight into a Tascam DR100 mk 2 and recorded in wav mode, then compressed to mp3 in Soundforge.
In the eighties and early nineties Hyperion Records used the organ to record classical music, including string quartets, piano solo and the Kings Consort doing The Four Seasons. Eventually Luton Airport, about 8 miles away, got too busy!
The Reslo RB mics are perhaps most famous for being used by the Beatles in their Cavern Club days. As a young photographer, Andy was assigned to one of their early gigs, and here are some of those photos at the Daily Mail website.
![]() |
One of Andy’s photos of the Beatles |
Stereo guitar switching box
Carrying on from my previous post….
![]() |
3 channel guitar switch box |
It’s a very simple custom 3 channel foot-switch box, which lets him control each of the bass, treble and rhythm channels separately. I was pleased with how it came out. Hammertone paint always gives things a 1950s industrial look.
Pickup fitting with Bobby and Jemima
I recently installed one of our hexaphonic pickup systems into a a guitar for Matt Shaw, who is one half of Bobby and Jemima.
![]() |
Bobby and Jemima… AKA Charlese and Matt (not sure who is who!) |
Matt provides a large chunk of the music for the act, playing guitar and drums – often at the same time – and he wanted to be able to send bass runs on the lower strings to a bass amp whilst simultaneously playing the melody and lead from the top strings out through a guitar amp. No problem at all!
I fitted a hexapup to the bridge position, wired out to a pair of output jacks, and an additional toggle switch gave the option of sending the G-string to either the bass or treble output. And we put one of our new P90 pickups in the neck position, with its own output for a third amplifier. Now Matt can make a lot of noise with one guitar!
![]() |
Lots of mess during the pickup transplant. |
![]() |
All stripped down and ready for the new pickups |
![]() |
Xaudia’s Meteor coil winder, and lots of wire! |
![]() |
Some fine tuning of the setup |
![]() |
All done! |
Inside the Beyer M360 (again) …
![]() |
Beyer M360 cardioid ribbon mic |
![]() |
Beyer M360 labyrinth (left) and motor. |
The magnet assembly is larger than the standard Beyer motor, in order to accommodate a smooth curved cavity at the rear of the ribbon. This tube curves through 90 degrees and out through a hole in the aluminium base plate. This connects to the inlet of the acoustic chamber, which consists of 25 interconnected tubes that go up and down through the block. There does not appear to be any kind of outlet at the far end, and the tubes are stuffed with string to damp internal reflections.
The mic is really directional, with relatively little pickup from the rear of the ribbon. The back pressure from the sealed rear chamber also has the consequence of making the output brighter and lower than it would otherwise be. These are really very bright sounding for ribbon mics.
Reslo MR1 ribbon mic (MOTM)
The MR1 was an attempt by Reslosound to re-invigorate the classic RB model for a 1970s market, whilst trimming down the cost of manufacturing parts and assembly.
![]() |
Reslo MR1 and RB models |
The MR1 (left) has the same format as the RB, with the ribbon element and magnets housed in a tilting head attached to a cylindrical body that contains the transformer. The grills are now flat, rather than domed, and the custom pivot screw is replaced with a standard hex socket bolt.
![]() |
Reslo MR1 and RB |
The MR1 still usesd Reslo’s custom 3-pin connector, and still makes ground contact through the body only. One assumes that this was to ensure backward compatibility with their older mics and cables, but it seems like madness that they did not take the opportunity to switch to using XLR connectors, which were very well established by this time.
The classic stamped brass badge on the RB is replaced by a printed foil sticker that hides the join between the barrel of the mic and the cast base of the pivoting head. The sticker shouts ‘Reslo MR1’ – note that it no longer says ‘Reslosound’ – in a very trendy 1970’s style font, with fattened letters typical of the era. I am also 1970s vintage, and the label reminds me of watching programmes like Magpie on TV in my childhood!
![]() |
Magpie – classic 70s font! |
The ribbon and motor assembly (top in the picture below) is exactly the same as the RB, but the transformer is smaller. Over time, better understanding gave rise to alloys with higher magnetic permeability, enabling smaller transformers to be made with the same inductance properties. The RB mics used a EE24/25 size core (pictured below the motor). The MR1 has a narrower body and a smaller transformer marked 4414.
![]() |
Top to bottom… Reslo MR1 motor, transformers from RB, MR1 and Xaudia |
Xaudia, as you might expect, make a suitable replacement transformer (bottom) for upgrade and impedance matching duties. 😉
Compared to the RB, I see very few MR1s, and can only conclude that they were not a great success. By the 1970s, good dynamic mics were becoming the first choice for home recording, and professional recording studios would probably favour condenser microphones for many applications. Reslosound Ltd. disappeared sometime in the 1970s, and this must have been one of the last models that they produced.
Lustraphone microphone catalogue
With a typically British quirkiness, the price of the VR65 stereo ribbon is given as 30 Guineas rather than pounds, shillings and pence. A guinea was equivalent to one pound and one shilling, so at about 4 times the cost of the mono VR64, the stereo VR65 was a very expensive mic!
In other Lustraphone related news, I have commissioned a batch of replacement enamel badges for Lustraphone VR53 and other microphones. They will be available through the Xaudia website very soon.
Electro-Voice Microphone Catalogue
In the velocity microphone description I was amused to read that “the woven housing allows the sound to pass through without reflection”. This neglects to mention the whopping magnet located at the rear of the ribbon! All of the dynamic ribbon mics were available in 50, 200, 500 ohm and high impedance models, which reflects the plethora of input types around at that time.
Cadenza Crystal Mics – a mystery solved!
This Ebay auction has solved a little mystery for me!
Cadenza Crystal Microphone |
Cadenza was a British brand remembered primarily for their ‘Rocket’ ribbon microphones. They are still quite common, and I have repaired many of them in the course of my work.
![]() |
Cadenza microphone with ribbon element |
Most of the Cadenza mics are grey or pale blue in colour, and have a removable stand. However, I have come across three or four of these mics with black bases and a fixed stand. These often have a crystal element rather than a ribbon motor, and I and speculated on their origins in a previous blog entry. When I first encountered one of these, I had thought that it was some kind of DIY ‘repair’ job, but having seen more than one, it seemed more likely that they came out of the factory this way.
![]() |
Crystal element in a Cadenza body |
Until now I had never seen an advertisement, manual or box that could confirm the existence of a Cadenza Crystal microphone. The photos in the auction show the original packaging, marked ‘Cadenza Crystal. So this was indeed a Cadenza product, using the same body as the ribbon microphones.
I like the triangular box!
Thanks to Benchmark Collectibles for permission to use this photo.
MOTM: Melodium / Radiodiffusion model R
Here is a rare and magnificent microphone: the Melodium type R (number 12).
There is a bit more about the history of the French national broadcasters here, and it seems that Radiodiffusion Nationale began in 1939 but was subverted by the Vichy government in 1940. It was replaced or perhaps rebranded in 1945 after the end of the war. There is more history here for our Francophonic readers.
Inside, the mic is very similar to the 42B, with the same magnets and motor assembly, but the internal grills are different, using a wider mesh and cloth.
The high pass filter section of the mic is also different to its square cousin. Instead of the three way rotary switch on the 42B, this mic uses a metal bar to bridge a terminal inside the base of the mic, and it just as ‘Music’ and ‘voice’ settings. A hole in the bottom plate lets you see whether the jumper bar is engaged or not. It is a more reliable arrangement, but you need a screwdriver and spanner to make the change. I guess the guys at the radio station did not want the filter to be engaged accidentally, causing them to wonder where the bass had gone!
Remarkably, the ribbon on this one was still intact, and after cleaning the motor the mic sounded very good indeed, with a big bottom end and nice proximity effect to make voices sound richer and fuller.
![]() |
New parts for the old microphone. |
The mic arrived without some parts, so we made replacement brass washers and thumb nuts on the lathe. They look really smart, and in a few months will be a lot less shiny!
![]() |
Melodium 12 side by side with the 42B |
Oktava mod FET biasing
Our good friends at Valley Wood Studios in Leeds had followed one of the popular projects for upgrading Oktava MK319 microphones, which involves changing a handful of resistors and caps, along with the field effect transistor (FET). After the mods one of the mics was about 3dB louder than the other.
This kind of thing is normally due to variations in the FET’s characteristics, and to optimise the modification, it is necessary to adjust one or both of the bias resistors (R7 and R8 in the PDF document). Between them these set the gain of the mic, and the bias point for the FET, which gives the best noise performance.
I often do this by hacking a decade box into the circuit, and in this case we put the mic in our test chamber so that we can tweak and scan as we go along. At the end of the tweaking the pair of mics were well matched, and noise free.
We celebrated with tea and biscuits!
Cadenza Mic Transformers and Mounts
Xaudia now supply drop-in upgrade transformers for Cadenza ribbon microphones.
![]() |
Xaudia transformer (left) and original Cadenza tranny |
The transformer is supplied in a mumetal shielding can of the same dimensions as the original, and slots into the base of the mic below the motor assembly, as shown.
![]() |
Cadenza on a stand! |
And here is a funky adapter that we made for a customer, to mount his Cadenza onto a normal mic stand. It recycles the plastic connector and locking ring from the original tripod mount.
![]() |
Cadenza mic stand adapter |
*Or other impedance values on request.
Reslo RV and UR microphone variations
![]() |
Reslo RV ribbon velocity microphone. |
The RV was one of Reslo’s earliest ribbon microphones – possibly their first production model, although I am not sure if the UR series came before or after. They share parts so it is hard to pin down which one came first.
![]() |
Inside Reslo RV mics |
The two mics shown have the same frame for the ribbon, but the magnets are very different. I believe the mic on the right to be the earliest RV design, or at least the earliest I have come across, and it uses a single cast magnet with quite a complex shape.
![]() |
Reslo RV magnets |
The mic on the left uses two simple horseshoe magnets at the top and bottom, attached to a pair of metal pole pieces, and this really sets the style for all subsequent Reslo ribbons – later models have three magnets but use a similar layout.
The UR model has a similar construction but has a rear mounted transformer. This is effectively blocking the pickup from the rear of the mic, giving it a more cardioid pickup pattern. It seems likely that ‘UR’ stands for Unidirectional Ribbon, although I have not seen any documentation to support this.
![]() |
Reslo UR magnets and rear-mounted transformer |
But the story doesn’t end there. Many of the RVs that I have worked on have a later, smaller motor which is essentially the same as found in the RB model. Keeping common parts with the later models must have kept costs down.
![]() |
Reslo RV mics with different motors. |
Until very recently I had only ever seen 30 ohm versions of the RV and had assumed that they were all low impedance. However, the one on the left, which came in recently, has a high impedance transformer, and measures around 6.5K ohms with the original ribbon.
Reslo mics don’t have serial numbers or dates on them, so it is hard to make a definitive time line for the development, and always if you have any further information we would love to hear from you.
Bang and Olufsen BM5 manual
Here is the manual for the B&O BM5 stereo microphone, in English.
M320 and M360: Beyerdynamic’s ugly ducklings
We have TWO microphones-of-the-month for May. Both are cardioid ribbon microphones from Beyerdynamic. We see a lot of M260 models, but the M320 and M360 are bigger, uglier and much less common too.
![]() |
Beyer M320. Do not stick it in your kick drum! |
The M320 makes good use of plastic for the body, and has all the style of a brick! A Beyer catalogue* from 1965 called it a “heavy-duty dynamic type for show business use”, and the switch allows the use to select ‘music’ or ‘speech’ settings, the latter giving a bass attenuation of 12dB at 50Hz. Because of its appearance and a vague resemblance to the AKG D12, it is tempting to thing that this is designed for inside a bass drum. It is not.
The M320 has the same motor that is found in the M260, but is connected to a large rectangular chamber below the mic via a tube. I have not been brave / stupid enough to cut open the chamber to see what is going on inside, but one assumes a series of interconnected tubes forming an acoustic labyrinth.
![]() |
Beyer M320 inside |
Although the M320 is called ‘heavy duty’, the M360 is much more sturdy, with a metal housing and grill. The catalog calls it a “dynamic unidirectional studio microphone with ultra-modern styling“. Again, it is as elegant as a 1980s Volvo, but at least form follows function in these mics!
![]() |
Beyer M360. Ultra-modern? |
![]() |
… or just ugly? |
The M360 is slightly larger and like the M320 it also has an acoustic chamber below the ribbon motor. I was fully expecting to see the same motor in this mic as is found in the other Beyerdynamic ribbon microphones of the same era, so was suprised to find something quite different. Rather than being assembled from four small magnets glued together, the M260 has a larger cast magnet with two copper coloured pole pieces which may also be a magnetic alloy.
![]() |
Beyer M360 motor |
Although the motor is wider and deeper, it still accommodates the same size of ribbon. And the magnetic field measures around 5000 Gauss, which is similar to a ‘normal’ healthy Beyerdynamic motor. So I am really not sure why this uses a different motor. Perhaps it was an early production run. The transformer and switch (on/off) are housed below the acoustic chamber below the microphone.
In the photo above, the ribbon is fully corrugated, but another specimen (below) had a standard Beyer ribbon, which seems more likely to be the original.
Both mics sound good when working properly, with a cardioid pickup, a relatively flat response and a bit less proximity effect than you would find in a figure-8 ribbon. They use the typical tiny Beyer transformers, which in the case of the M60 at least is wound for a full range response.
*Here is the full Beyerdynamic catalog from 1965, at the excellent Coutant website.
Huge heavy Meico dynamic mic
Here is another big old dynamic microphone, this time made by Meico.
![]() |
Meico Dynamic microphone |
The big ferrous magnet inside the mic bring the weight up to nearly 1.5 Kg!
![]() |
This one is certainly a heavyweight! |
The badge is very cool though, and the star and wings look like it might be inspired by Soviet artwork of the era!
![]() |
Like Mexico, but without the X…. |
According to this eBay seller, the mics were made in Congleton, and they were used as announcer’s mics in boxing matches. I have found nothing to confirm or deny this, so as always if you know more than I do, please get in touch!
But if it fell on your head, then it would certainly be…. a knockout.
(Sorry)
Oktava ML16 ribbon microphone dissected
MOTM – Toshiba Type K multi-pattern ribbon mic
![]() |
Toshiba Model K |
![]() |
Rear of the model K, with pattern control |
Inside the mic, the motor is based around a single strong horseshoe magnet, with the ribbon held between two chunky pole pieces.
Like the RCA 77DX, there is an acoustic labyrinth made from a series of holes with connecting channels, which goes up and down the centre of the mic. Two thick wires take the signal from the ribbon, through the labyrinth, down to the transformer below.
![]() |
Acoustic labyrinth in the middle of the mic |
The pattern control uses a choice of baffles to partly or entirely redirect the rear of the ribbon into the acoustic labyrinth. This turns the mic into a pressure transducer when the rear baffle is closed, giving a more omnidirection pattern.
![]() |
Pattern control on the Toshiba type G. |
It differs from the RCA design: the 77DX has a a cam shaped copper plate that allows the rear vent to be opened by incremental amounts, whereas the Toshiba has three discrete positions, which are labelled…
- N (fully closed – non-directional)
- B (fully open – bidirectional or figure 8), and
- U (a small opening – unidirectional or cardioid)
And in an attempt to beat the Americans, on the bottom of the mic there is a switch for a 6 position variable frequency high pass filter – the RCA77DX only has three!
![]() |
High pass filter switch |
The Bang and Olufsen ribbon microphone family
![]() |
B&O ribbon mics, from left, 2x BM2, 2x BM3, 2x BM6, 3x BM5 stereo |
As far as I can tell, the first commercially available B&O ribbon mic was the BM2 – which begs the question “what happened to the BM1?” There seems to a bit of confusion about this, and possibly there never was a model called BM1. According to Beophile, the first B&O microphone was a dynamic mic called MD1. However, others have listed this as BM1. Numbers 2 to 7 were ribbons and carried the prefix BM, which may have stood for ‘baand mikrofon’ – Danish for ribbon microphone. Although it could also have stood for beomic. The MD8 was also a dynamic.
![]() |
B&O BM2 ribbon microphone |
Regardless of the BM1 (or lack thereof), the BM2 is a good-looking microphone, with a very different look to the later mics. It has a cast metal body and folded, chromed brass grill. The mics were painted in a green-yellow textured paint, which looks better than that sounds! They are usually* 50Ω mics, with an a switch which connects an inductor into the circuit, for a high pass filter. The ribbon is held in a removable frame, which slides out for servicing. (*They can be re-wound for 300Ω, to great effect).
The BM3 and BM4 look very similar to one another, and used an evolution of the motor assembly in the BM2, this time in conjunction with a steel tube body. This design set the style for all their later ribbon mics, and also inspired Speiden and Royer microphones, and a bunch of clones such as this Stellar mic.
![]() |
B&O BM3 microphones |
In the case of the BM3, the ribbon motor frame is larger than the diameter of the tube and sticks out from the sides of the mic, giving it the look of a long face with ears, or perhaps Doctor Who’s Cybermen. It has a three way selector switch which provides M (music – full range), T (talk – HPF) and 0 (off) positions.
![]() |
Motor frame from the BM3, with Xaudia transformer, awaiting a new ribbon |
The BM4 looks the same as the the BM3, but with an additional switch at the rear for selecting 50, 250Ω, or high impedance output. The BM3s were fixed at 50Ω (and benefit from a matching transformer or upgrade). Occasionally you see these badged as “Fentone”, although, oddly enough, they kept the B&O name on the mic too.
![]() |
Fen-tone add showing the BM3 – from Preservation Sound |
The BM5, BM6 and BM7 came later and formed a family of mics. The BM5 is the stereo model, and when rotated to 90 degrees, it is perfect for Blumlein pair recordings. The bottom half of the BM5 was available separately as the mono BM6, and the top was called the BM7, although it could not be used by itself.
![]() |
Standard BM5 stereo set with stand |
The design was an evolution of the BM4, but by this point the ribbon frame and been replaced by plastic mounts, and the cyber-ears have gone. The magnets are also slimmed down, with a semicircular or triangular cut-out, presumably in an attempt to increase the high frequency response. In these mics the body of the mic is made from steel and also acts as the magnetic return path, which helps to increase the output.
![]() |
Insides of a B&O BM6 ribbon mic. Note the pistonic ribbon |
Like all of Bang and Olufsen ribbon mics, the BM5/6/7 family have a pistonic ribbon, which is gently curved in the middle and deeply corrugated at each end. The ribbons were made from Duralum alloy, which contains copper in addition to aluminium, to improve the strength and stiffness. However, the alloy is more prone to corrosion than pure aluminium, and it is quite rare to find ribbons that are in perfect condition.
![]() |
Delux BM5 set in posh wooden box! |
From a technician’s perspective, these later mics are less robust than the BM3/4. To me they feel more of a hi-fi design than one for a busy working studio. Although the sound is excellent, they are delicate in places and some of the plastic parts deteriorate with age, most noticeably the rotating ring in the top part of the mic. The switch tips also have a tendency to come off.
![]() |
Plug for a B&O BM3 microphone |
All the B&O mics used bespoke connectors, which can be hard to find. the BM2, 3 and 4 have a 3 pin connector only found on B&O equipment, whereas the BM5 and 6 used 5-pin DIN connectors but with their own threaded locking ring. The latter can be replaced with a standard bayonet DIN if the cable is missing.
Here are some links to wiring diagrams for some of the mics.
BM3 data sheet
BM4 data sheet
BM6 data sheet
BM7 data sheet
Thanks to Tom Day and Robin Kiszka-Kanowitz for additional information.
Update 1/2/18
Our friends at Extinct Audio now manufacture the BM9 studio ribbon microphone, which shows the influenced of the B&O designs.
Update 4/3/14
We now have upgrade magnets and transformers for all B&O microphones.
Update 22/4/13
Many thanks to Evan Lorden for sharing these photos of his B&O MD1.
Geloso M88 dynamic microphone
Here is a pair of funny little Geloso dynamic microphones, one is in pieces already.
![]() |
Geloso M88 dynamic mics |
The build quality is nice – better than the early Geloso mics which tend to crumble. It has an internal two-bobbin humbucking transformer, to give an output impedance of 250 ohms.
![]() |
Internal transformer for impedance matching duties |
The diaphragm is made from a light plastic for fast response, and they sound nice, if a little light on bass.
![]() |
Geloso M88 diaphragm in good shape |
![]() |
The original unobtanium connector can be converted to XLR |
🙂
Short, stubby and dynamic – The Reslo PGD
Reslos are best known for their ribbon mics, but they made some dynamics too.
![]() |
Short, stubby and dynamic – The Reslo PGD |
The PGD appears to be made of leftover parts from the RV ribbon mics. The base of the mic is the same, complete with swivel mechanism, and the grill looks like a cut down version of the RB too. As usual it uses the annoying Reslo plug.
![]() |
The head on the RGB could be tilted for best pickup of sound. |
![]() |
Reslo PGD – aluminium diaphragm |
Like many early dynamics, it has a pressed aluminium diaphragm, which is heavy and stiff compared to later polymer film designs. Consequently has a quite lumpy response. Here is a frequency plot for one mic – other examples may differ!
![]() |
Frequency sweep for Reslo PGD mic. |
Experiments with Carbon Microphones
They were really simple devices, with small particles of carbon packed into a space between two electrodes and pressed against a plastic, mica, rubber, or wax paper diaphragm. When connected to a battery supply, a current flows through the mic which is modulated as the sound impinging on the diaphragm compresses and releases the carbon particles.
![]() |
Old carbon microphone – unknown manufacturer |
The body of the mic is made of an insulating material, in this case a block of marble. The classic Marconi-Reisz microphone also used marble – this one is clearly a copy of that mic. Others had bodies made of wood, which must have been cheaper to make. Four hooks screwed into the body would have been used to suspend the mic within a metal ring, using springs or rubber rings, like this nice example at the ORBEM website.
![]() |
Old diaphragm and grill from a carbon mic |
After many decades this example is in pretty poor shape: most of the carbon has escaped into the wild, and the diaphragm is cracked and perforated. I wanted to try and get this working again, for fun and as a learning experience.
![]() |
Clean again! |
The first step was to clean everything up in the ultrasonic bath, and the brass terminals were given a scrub. At least it looks better! The carbon will sit in the depression between the two brass terminals.
![]() |
New diaphragm ! |
I made a new diaphragm by stretching a sheet of thick cellophane over the bakelite frame that makes up the front of the mic, and then heated it gently with a hot air gun. The plastic film shrinks and pulls itself tight. It looks neat and has a similar thickness to the original – as far as I can tell.
Then the mic can be re-assembled and filled with new carbon granules. It takes a few goes to pack the carbon, shaking the mic in between each fill.
![]() |
Carbon microphone circuit, from the TFPro website. |
I tried a circuit inspired by the one above, using a battery and transformer. Ideally the transformer should be gapped, or a capacitor used to block the DC, to prevent saturation.
With a new diaphragm and new carbon, the microphone does now pick up sound, and although it is far to noisy for any serious recording, I was pleased just to get that far in my first attempt. As always with microphones, the art is in the detail and I can now at least appreciate some of the design parameters than need to be considered. These include
- Diaphragm material, tension, thickness and stiffness. The diaphragm needs to be thin and compliant enough to vibrate, yet stiff enough to transfer the energy to the carbon granules. Cellophane may perhaps be too flexible, but glass or hard plastic could be too stiff.
- Carbon granule type, size and packing. The carbon needs to be compress reversibly by the diaphragm, otherwise it will pack and stop working.
- Impedance. I noticed that the impedance of the mic dropped from about 10K ohms to 1K ohms on tightening the filling screw. Clearly some pressure on the granules makes a big difference to the impedance, and also made an audible difference to the sound of the mic.
- Terminal size and shape. The contact with the carbon granules will affect the impedance of the mic and the efficiency.
- Circuit. Varying the voltage across the mic made a noticeable difference to the noise level. The transformer should be capable of taking some DC current, or a capacitor used to block the DC. (which is how I did it)
There is also a nice blog post about carbon mics at Preservation Sound.
MOTM: Siemens-Telefunken M201/1 Ribbon
We have seen an influx of weird and wonderful ribbon microphones this month, including a rash of Bang and Olufsens, half a dozen Film Industries mics, and a cardioid Toshiba BK5 copy, so we were spoilt for choice for a Microphone of the Month…. until this came along…
![]() |
Telefunken M201/1 cardioid ribbon microphone |
The Telefunken M201/1 was one of the very first commercial ribbon microphones. It was made by around the early 1930s and would most likely have been used for radio broadcast. These ribbon mics were a big improvement on the carbon microphones that they replaced, but in Germany they were quickly superseded by the new valve condenser microphone technology.
![]() |
Telefunken logo on the M201/1 microphone |
There are very few of these left in circulation – this one is in very nice condition and after a clean and a new ribbon sounds truly excellent, with a strong output not much below a modern dynamic.* After over 80 years, the magnets are still strong with a field on >5000 Gauss in the narrow 2.5 mm gap between the ribbons.
![]() |
Telefunken M201/1 rear |
The M201/1 is constructed around a huge horseshoe magnet, which surrounds the transformer and (presumably) some kind of acoustic labyrinth or wadding to control the pattern. This dictates the shape of the body and gives it an unusual cylindrical aspect. The ribbon sits behind a fine brass grill at the front of the mic. With the rear of the ribbon being obstructed by the magnet, the mic is almost cardioid in nature, becoming more figure of 8 towards the very bottom of the frequency range. Two chrome B-shaped vents sit above and below the ribbon to equalise the pressure behind the ribbon. The output connection is made via a pair of screw terminals hidden behind a circular plate on the rear of the mic.
![]() |
M201 ribbon |
The ribbon itself is long and thin, and the old broken one inside the mic was fully corrugated (the one shown is a replacement). For ‘ease of service’ the ribbon is held in a frame behind the front grill. However, once in place the assembly hides the ribbon pole pieces from sight, which means that alignment is a case of trial and error, which is possibly the only weak part of the design that I have found. With the new ribbon, the mic has an output impedance of around 300 ohms.
![]() |
Telefunken M201 under test |
I did a test sweep of the mic in our little testing chamber.** The mic shows a strong output with good bass response, a little proximity effect below 100Hz, and a graceful roll-off above 6KHz. The noise above 14KHz are likely to be diffraction from the grill and other parts.
This microphone is thought to have been made originally by Siemens & Halske and supplied under various model numbers including the KVM3, SM3 and others, and this rather wonderful example on Martin Mitchell’s excellent microphone blog, which is just called model ‘R’. In German a ribbon mic is called a Bändchen-mikrofon. However, the name plate on this is in English, and perhaps this is the export model, with the R simply for Ribbon. There is a bit more history at Martin’s blog, which is well worth a read.
![]() |
Mitchell’s Siemens type R ribbon microphone |
* Testing against a Shure Beta57, the preamps were on the same gain setting for a comparable output
**Calibration is with an omni measurement mic, so there can be some bumps due to the differences in pattern picking up more or less reflections from the room.
Toshiba Model H mic – RCA BK5 copy
![]() |
Toshiba type H ribbon mic – looks like a BK5 |
The ‘Model H’ is no exception, being almost identical to the RCA BK5 cardioid ribbon in both looks and function. The small format ribbon sits between powerful magnets, in front of an acoustic chamber or labyrinth that takes up the middle segment of the microphone
![]() |
Rotating the base of the mic implements a high pass inductive filter. |
In fact it seems slightly better engineered than the BK5, with a 5 position high pass filter switch that is actuated by rotating the dial at the very bottom of the microphone.
![]() |
Toshiba type H ribbon |
There is some additional electrical screening around the ribbon, but less acoustic baffling in front of it, which may be to give a more ‘open’ sound. In practice the ribbon is more prone to being stretched by air blasts than the RCA model.
Grampian Amplifier Speaker Set
As well as microphones, Grampian made amplifiers and other PA equipment. Here’s an old Grampian amplifier and speaker set.
I found the amp a few years ago in Dave Dee’s junk shop in York. The circuit is actually very similar to a Mullard Twenty, with the addition of a transformer balanced mic input, and several taps on the output transformer for 8 ohm loudspeaker or 100V connection. I have even used this in the past as a mic preamp for recording, for some warm and slightly dirty vocal tracks.
The speaker is a recent purchase found on GroupDIY.com. It has a rather nice and unusual tapered shape, with (no longer very) white vinyl covering. The whole set has a really cool vintage look to it – very different from today’s ubiquitous square black boxes.
I am now using this as a guitar rig – it has a great vintage valve tone with just the right amount of breakup coming from the speakers. There is plenty of volume for recording, but I would hesitate to use it for rehearsals with a modern loud drum kit!
I am unsure of the age of these but I would guess 1950s or early 60s – they don’t appear in Grampian’s 1968 product line, and presumably pre-date that. If anybody knows more, please get in touch.
Hexapup switching
GEC Ribbon Microphone Evolution
Some time ago I posted about GEC models BCS 2370 and 2373, and how they were essentially the same design in different body shapes for different applications.
![]() |
Left to right – unknown, unknown. GEC BCS2370 and 2373 mics. All have the same motor. |
Since then I have come across some other ribbon microphones which may be earlier GEC models, prototypes. They are perhaps rather ugly in style, but I find their functional utilitarian style rather charming.
The two unbadged mics share some parts including a twinaxial connector at the base and rubber yoke mounts. The mic on the left is made of folded steel, whereas the one on the right is brass, with a more open grill.
All four mics are essentially the same design inside. The mic on the far left has a smaller transformer and different brand of magnet, but the pole pieces and ribbon assembly are the same. The mic in the middle of the photograph above is identical inside to the known GEC mics – with the same magnet and transformer and crumbling plastic ribbon mounts.
Drawing from a ribbon mic patent by GEC and Thomas Julian, 1947 |
![]() |
Drawing from BBC-Marconi type AX ribbon mic manual. |
Grampian GR1 & GR2 ribbon mic manuals
Grampian made some fine ribbon microphones, and the GR1 and GR2 were our Microphones of the Month in May of last year. Here’s a scan of the original Grampian GR1/2 manual.
![]() |
Grampian GR1 or GR2 ribbon mic |
The mic also came with a word of caution….
![]() |
Don’t test a ribbon mic with a multi-meter or else… |
I am particularly pleased to see the warning not to use a DC meter on these. Quite often I come across ebay auctions where the seller measures ribbon mics with a multimeter, unaware that the carrier current can bump the ribbon out of the magnetic field and stretch it. 🙁
Grampian also made matching transformers for their mics – we have a few available for sale. Here is the factory drawing for the transformer.
![]() |
Grampian matching transformer wiring. |
I posted some other Grampian documents last November.
Many thanks to Pete Guppy for sending this in.
Melodium documents from 1970s
![]() |
Melodium 78A cardioid dynamic microphone |
Here is a scan of an English language Melodium product catalog for their line of microphones, which (probably) dates from the 1970s. It includes the RM6 ribbon microphone, 76A & 78A cardioid dynamics, and 77A, 79A & 88 omnidirectional mics, along with a range of accessories.
French language data sheet for the RM6.
Many thanks to Santiago Ramos for sharing these.
Thiele Microphones schematics and documents
Thiele, of Liepzig, were one of several manufacturers of tube condenser microphones in post-war Germany, although they are less well known than Neumann, Gefell and Schoeps. Thiele microphones also appeared under the Elektro-Medizin and Wetzel brands.
![]() |
Thiele M4 microphone |
The Thiele M1 (cardioid) and M4 (cardioid and omni) are great looking microphones but feature some frankly bizarre design decisions, most notably the placing of the tube directly behind the capsule, which interferes with the rear pickup whilst simultaneously cooking the PVC on the rear capsule. Of course the manufacturers would never have expected that we would be picking up these mics sixty years on and trying to record with them.
![]() |
Inside a Thiele M4 |
In addition, the power supply was built into the base of the mic which can lead to hum issues despite the on-board potentiometer that acts as a ‘null’. This also means that the mic has two cables running from it – one for power and one for audio. Both mics use two-stage head amplifiers based around an ECC83 tube, and both have unbalanced outputs. Here are the official schematics for the M1 and M4 mics.
![]() |
Thiele M4 microphone circuit |
![]() |
Thiele M1c tube microphone circuit |
The M5 seems to have been the ‘Studio’ version, with an external power supply and output transformer for balanced low impedance operation. I haven’t seen a factory schematic for the M5, but this is a drawing that I traced out from a specimen on the bench.
![]() |
Thiele M5 microphone, inside and out. |
Here are some original sales and technical documents from Thiele, in German.
Thiele sales brochure for M1 and M4
Elektro-Medizin M4 technical document
Elektro-Medizin M4 & M5 product sheet
Many thanks to the Microphone Online Museum for kindly sharing the documents and schematics.
Massive Old Dynamic Microphone – GEC?
We’ve had some website issues this weekend, but everything has been sorted out, so let’s get back on track with another vintage microphone curiosity.
![]() |
Frequency plot for big bronze dynamic microphone! |
MOTM: Bruno – Webster Velotron Microphone
The Bruno Velotron (made by and sometimes badged as Webster) was an oddball microphone that took inspiration from both ribbon and condenser technology. Strips of aluminium foil were attached to an insulated metal backplate, and a voltage applied between the two. As the foil vibrates, the capacitance of the device varies, and a signal is generated. They are notoriously fragile, and there are very few around in working condition.
![]() |
Bruno Velotron microphone |
I found this one on ebay a few months ago and could not resist grabbing it for dissection and possible resurrection. The specimen is in very good cosmetic condition so will look nice in the collection even if it it is beyond repair. But it would be even nicer if we could hear it in action!
Looking inside, the element is marked ‘4½M’ and 2/4/38, which in American would be 4th Feb 1938. The ‘4½M’ may refer to the impedance of the device.
![]() |
Velotron element |
The Velotron requires a polarisation supply and a buffer amplifier to operate – I am not sure if these came with the mic, but the tube amps of the era could easily have been modified to provide this from the high voltage supply. The excellent Coutant.org shows a wiring diagram for a suitable polarisation supply and buffer amplifier…
![]() |
Supply for Bruno microphone – from Coutant.org |
Based on this diagram, I wired a 7205 subminiature tube into one of our tube microphone power supplies, to act as a little amplifier circuit for the mic.
![]() |
Hacking together a power supply and amplifier. |
![]() |
Bruno Velotron – frequency plot |
Altec 670A vs 670B microphones – What’s the difference?
![]() |
Altec 670B (left) and 670A (right) ribbon microphones |
Q. What is the difference between Altec 670A and 670B ribbon microphones?
I had not realised that there was a difference until I re-ribboned this 670A for a client, which gave me an opportunity to compare it to our studio 670B. The two microphones look identical from the outside apart from the label. Both are housed in some kind of blue-grey plastic, and the label hides an impedance switch cryptically marked ‘1’ and ‘2’.
The ribbon in the earlier 670A is twice as wide as the later 670B, measuring 3.8mm and 1.9 mm wide respectively. The narrower gap between the magnets would also give a higher magnetic field, although I forgot to measure that.
![]() |
Altec 670A ribbon and 670B (right) ribbons. |
Both ribbons are the same length, so if the same thickness of foil is used, the 670B ribbon would have (about) twice the impedance of the 670A. This has implications for the transformer design, as a different ratio and different inductance would be required.
A second difference is in how the transformer primary wire is routed. In the 670A (left) the thick wire is routed directly behind the ribbon, which would affect the pickup pattern of the mic. This is redesigned in the 670A and passed to the side of the ribbon.
![]() |
Altec 670A and 670B pattern selectors |
Both mics were ready for new ribbons so I replaced both with 1.8 µm foil and measured the impedances (in position 2). The 670A had an impedance of 600Ω whereas the 670B measured 350Ω, which shows that the transformers are indeed different ratios.
It also suggests that the 670A would have originally been fitted with substantially thicker foil – perhaps 4 or 5 µm. The feel and stiffness of the corroded old ribbon also suggests this to be the case.
Here is a frequency plot of the two mics. The 670A is the red line, and the 670B, in blue has a slightly higher overall output. Both mics sound very good and quite similar in tone despite the differences.
Melodium 93C & 530C measurement microphones
Melodium was a French manufacturer of microphones and other audio equipment, probably best known for their excellent model 42B ribbon mic.
The Melodium model 93C is a small diaphragm condenser measurement microphone that was on the market in the 1970s. Although the data sheet is not dated, the frequency plot is marked 03-73, which pins down the measurement, if not the manufacturer, to March 1973. The specimen on the bench was actually stamped with model number 530C, but seems to be the same microphone.
![]() |
Melodium 530C measurement microphone |
The 93C / 530C needs a 13V to 18V supply to operate, and a battery pack was available.
![]() |
Melodium 530C with battery pack |
The mic is not compatible with phantom power, but a simple converter can be built. In this case it was built into the old battery pack, with an indicator LED replacing the on-off switch.
![]() |
Melodium 530C with modified supply to convert from phantom power |
Once the power is sorted out, the mic is quite sensitive, with a very hot signal which may even need padding for louder instruments. The mic seems nice and flat up to about 8000 Hz – here’s the result from our little test chamber, which doesn’t go much past 10KHz anyway.
![]() |
Frequency plot for Melodium 550C, referenced to Beyer measurement mic |
When I wired this one up according to the manufacturer’s data sheet, I found that the mic was out of phase with our reference mic, and indeed the data sheet claims that the ‘Angle of phase rotation 180C to tension’.
Here is the manufacturer’s data sheet for the Melodium 93C.
Thanks to Santiago Calvo Ramos for sharing.
Ward Beck preamps part 2
With additional holes drilled for XLR inputs and a power switch, the panel is ready for the modules to be screwed in place.
It looks like a neat job once the black printed control panels and all the knobs are back in place – I also added a pair of jack sockets as additional outputs so that I can route the signal to either the front of the unit or the studio patchbay – or both for some parallel compression fun!
The modules are connected to the outside world via 44 pin card connectors at the rear. Although these look daunting, only a few of the connections are needed for our application. Here’s a revised pin assignment with the surplus connections omitted.
In this case I am just using two of the four available inputs – XLRs on the front connect to Mic Input A, and jacks on the rear for line input A. Both sets of outputs (M1 and M2) will be used, one on the front and one on the rear of the case. On the original WBS mixer the modules would have been wired to a fader, but we can bypass this by connecting across the appropriate pins as shown in red. Note that in the schematic for the M480C, the fader inserts are wired from pin T to 10 and from pin 16 to L, which means diagonally across the connector rows.
It seems likely that some other part of the console flips the phase, or less probably that the M480 is differently wired from the M480C – one would expect the modules to be interchangable. Either way, the simple answer is to connect pin T to L and pin 16 to 10, as shown on the pin assignment above.
The hole for the fused IEC power inlet was cut through with an appropriate punch – this gives a neater rectangle than a jigsaw or just drilling and filing, and is quicker too. A dual ±24V bipolar supply is required, and I used a small board left over from an 1176 project. The board from mnats.net uses LM317 and LM337 voltage regulators, and 5Kohm trimmers were used to set the voltages. The modules have on-board filters and regulators to bring the down to ±18V, and their is no audible hum on these modules even at full gain.
Once up and running, the modules sound very nice with plenty of gain. I particularly like the low boost on the EQ, which sounds like it should be useful for beefing up tracks. At the moment many of the pots are rather worn and scratchy, so I next will strip it all down and replace those. It never stops!
MOTM – Lustraphone VR64 ribbonette
Lustraphone was a British manufacturer of audio and hi-fi equipment based on Regent’s Park Road in North West London. They traded from 1942 until sometime in the 1970s, when the company was dissolved. This month’s MOTM is the Lustraphone VR64 pencil ribbon mic, known s the ‘ribbonette’ because of its small size. It was the successor to the VR53. They were also sold under the EAP / Elizabethan brand.
The VR64 is an attractive looking small ribbon mic, with a slightly wider grill at the front than the rear. Like its competition from Reslo and Film Industries, the magnets are positioned to the rear of the ribbon making it an imperfect figure-8 pattern. It was produced in several colours – I have see brushed chrome, blue paint, and grey hammertone examples.
![]() |
Add caption |
I always thought that Lustraphone had one of the coolest logos, a bit reminiscent of The Man From UNCLE TV series. Different models have different styles of badges, either applied as a decal or a sticker.
When working properly, the VR64 sounds rather good, with a higher output and better top end response that the VR53. Like most of the British ribbons of the time, the Lustraphone mics were available with different impedances. The mics come badged with either ‘High’ or ‘Low’ impedance, but that doesn’t always tell the whole story. Two examples pictured here were both marked low impedance. However, one measured 15 ohms and the other 600 ohms, so it is important to know what you have.
The output transformers have a slight quirkiness, in that the bobbin is pushed halfway through the frame of the mic before the laminations are added, which neatly solves the problem of mounting the tranny.
![]() |
Lustraphone VR64 inside |
![]() |
Lustraphone VR64 motor – rear view showing magnets |
I’m not sure if having a layer of insulator between the laminations has any sonic effect, beyond the fact that the transformer has one fewer layer of laminations in the stack, and so a lower inductance and higher cutoff frequency. Probably little or none.
The 15 ohm transformer is made up from 15 turns of 0.85 mm wire for the primary, and about 145 turns of 0.3 mm for the secondary, giving a ratio just under 1:10. This one was re-wound for 300 ohms using the original lams, which gives a better output level into a modern preamp, whilst retaining the vintage character.
![]() |
Lustraphone transformer autopsy |
This example had a quick release mounting system. A bullet shaped part screws onto the mic stand, and then the mic is pushed onto it. Very cunning!
![]() |
Lustraphone quick release mic mount |
![]() |
Lustraphone VR65 stereo ribbon mic |
Lustraphone filed a patent for a stereo ribbon mic with a complicated switching system, to reverse phase and reduce noise, although the only examples I have seen have had seperate outputs for each ribbon, and no switches.
![]() |
Lustraphone VR65 in action |
Reslo LMT line matching transformer manual
Here is a scan of the manual for the Reslosound LMT series of line matching transfomers. If you have one, it might be useful! Many thanks to Lee Ackerly for sharing this.
Edit: link fixed 2nd March 2014
Reslo LTU1 line matching unit manual
When home recording with reel-to-reel tape machines was a popular hobby, back in the 1960s and 70s, many recorders had only high impedance inputs. However, the low impedance microphones of the time could be used with a longer cable without signal degradation, and so most manufacturers offered matching transformers to plug that gap.
Other transformers were also available to match medium and high impedance microphones to low impedance inputs, and so on. But the Low-to-High is by far the most common.
Here is a scanned manual for the Reslosound LTU1 line matching unit, which was used to connect 15Ω to 50Ω ribbon microphones to a high impedance tape deck. This was superseded by the LMT, which is essentially the same thing in a smarter metal can.
![]() |
Reslo impedance matching transformer. |
Film Industries M8 review – Tape Recorder magazine
A Film Industries mic arrived recently, along with a contemporary review from The Tape Recorder Magazine, by A. Tutchings. The level of technical detail the review goes into is impressive, testing sensitivity, proximity, frequency response and measuring impedance across the spectrum. Here it is…
Here is the full scan in PDF format, for download and printing.
Hexapup samples, wiring and technical specs
Here are some wiring suggestions and sound samples for our ‘Hexapup’ hexaphonic pickups
Installation – Mounting the pickup
The hexapup is a standard humbucker size and will fit into most humbucker routed guitars without modification. Please note that the hexapup gives best results in the bridge position, and because it uses strong magnets it not really suitable for use as a neck pickup.
1. Mono pickup
When wired as a conventional mono pickup, the hexapup has a bright single coil tone. The coil arrangement means that it has very good hum rejection (humbucking) properties.
2. Stereo guitar.
The simplest way to connect the hexapup for stereo use is to mount two jack sockets into the guitar, and wire one side of the pickup to each jack. The signal can then be run to two amps or DI boxes for gigging or recording. There are two obvious ways to divide the strings, the pickup can be supplied in either split or spread mode, with spread being the default.
![]() |
Split mode – low strings are sent to one amp, high strings to the other |
Split mode sends the low strings E, A and D to one channel, and the high strings G, B & e to the other, like Neil Young’s stereo guitar. Spread sends alternating strings to each channel, that is E, D and B to one output, and A, G & high-E to the other, which gives a nice spread of frequencies across the stereo image.
Here are some sound samples of the pickup in split mode. As always the stereo image comes across better on headphones than laptop speakers!
![]() |
Spread mode – alternating strings are routed to each channel |
Here is one of the riffs above in stereo ‘spread‘ mode.
In each case the playing is a single guitar, and the recording was made using the DI input of API A2D preamp into protools, processed using Amplitube amp modelling plug-in.
3. Mono / Stereo Jack
4. Stereo guitar with Split / Spread switch.
On request, the hexapup may be supplied pre-wired with a switch to choose either split or spread mode. Here is an easy way of switching between the modes.
The hexaphonic pickup can of course be supplied with six pairs of output wires, which gives a vast range of wiring possibilities. Probably the simplest way is to use a 6 or 7 pin XLR socket for the guitar output, and run this to a breakout box wired to give six separate jacks.
![]() |
Heavily modified Jagmaster with hexaphonic and stereo outputs. |
![]() |
Six channel breakout box for a hexaphonic guitar. |
Here is a sample recording made in hexaphonic mode, with the EA strings panned left, the top B and E to the right, and the D and G strings lower in level and somewhere in the middle. Different amp models (Amplitube) have been used for left and right.
There are some further sound samples of the hexapup in full hexaphonic mode here.
Xaudia Hexapup – Typical specifications
Dimensions
Fits in a standard humbucker route.
70 mm x 39 mm x 20.5 mm deep (25 mm including screw lugs)
Stereo model (3 coils in series)
DC resistance = 5.1 K ohms
Inductance @ 1kHz = 0.9 Henry
Wiring = Red & black, green & white.
Case ground = green/yellow
Red & green = positive, black & white = negative
Hexaphonic model (single coil)
DC resistance = 1.8 K ohms per coil
Inductance @ 1kHz = 0.31 Henry per coil
More Hexaphonic pickup sound samples
![]() |
Xaudia Hexapup |
A hexaphonic pickup lets you record you record the signals from each string separately, either through six amplifiers, or perhaps more sensibly by recording directly through instrument inputs or DI boxes. This gives a lot of creative possibilities.
For example, here’s a G major chord, played lazily from the low strings to the high. This was recorded directly into Protools, with the notes spread across the stereo width.
Adding an amp simulator gives it some body…
With a hexaphonic recording, it is simple to change the timing of individual strings. Imagine that we wanted the chord played tightly, rather than note by note. A quick edit and here it is…
Gmajor – all together
Or perhaps we would prefer to strum from the top to the bottom instead. No problem – we can just shift the notes slightly and we have it …
And by reversing the waveform of three strings and repeating the notes, we get this little ambient loop. A semi-reversed guitar
Now let’s get silly…
… we want to transpose part of a song, but the guitarist has gone to the bar. We can use Autotune on each track to pull each string up by two semitones to play an A major instead. Here’s how it looks on the screen…
And here’s how it sounds!
Auto-tuned Chord – Gmajor to A major
Of course we could have simply pitch shifted the whole chord up to achieve a similar effect – Autotune gives it an interesting glitchy slide texture as it chases the notes
By shifting the G-string up by one semitone rather that two, the chord becomes an A-minor. Now that’s something which can’t be done with simple pitch shifting!
Auto-tuned Chord – Gmajor to A minor!
The possibilities are endless!
Polyphon mechanical music player
This rather wonderful Polyphon type mechanical disc music player was a Christmas gift. Thanks Santa (& Mum & Dad!).
![]() |
Metal disc music player |
Inside the box is a clockwork device very much like a music box, but the music is encoded onto a metal disc with teeth around its outer edge.
The disc is driven by a clockwork device, with a coiled spring providing the power, and a spinning regulator to keep the speed constant.
The disk drives a set of rotating gears, which in turn strike the tines of the comb to produce the sound. Each tine is a different length, and so a different note. The sound is then amplified simply by the resonance of the wooden box.
![]() |
Small polyphon style music discs |
The discs are about the size of a CD, and the musical information is stored in them by punching and bending strips of metal so that they strike the music player. Each disc holds a mammoth 20 seconds of music, approximately. A few of the discs are rather rusty and bent, but the majority of them still play well enough.
![]() |
Rusting gracefully! |
Each disc is ink stamped with a number and the name of the tune. I have discs with numbers beyond 400, so this must have been a popular format with a wide choice of titles.
Here are some sound files for a few of the discs. The sound is pretty and a little creepy at the same time, with all of the mechanical clicks and whirrs. (mono .wav files around 3 Mb each, recorded with a Neumann TLM49 through RFZ KV80/1 preamp).
133 – Bonnie Dundee
143 – Banks of Alan Water
152 – Sally in our Alley
156 – Rock of Ages
189 – In the good old summertime
219 – Liberty Bell March (damaged)
222 – Marching through Georgia
402 – Carmen Polka
My aim is to record and share all of the discs that I have, so check back later for more.
Update….
I found this video on the web, which features the same player. The owner claims that it was made by the Swiss company Thorens in around 1910. One can imagine people taking this kind of music player along on a picnic perhaps, on a sunny summers day!
Happy 2013
Thanks to all of our friends, customers and suppliers who helped to make 2012 another exciting and successful year for Xaudia.
![]() |
Hot-rodded Reslo RB microphones |
In 2012 we repaired 203 microphones for customers, an increase over 2011, and Reslo microphones were again very popular – we serviced 47 of them this year. Once again RCA mics came in second place (23), with AKG and Beyerdynamic in third and fourth.
![]() |
Xaudia – microphones serviced in 2012 |
We sold a further 50 or so refurbished vintage ribbon microphones through our website, including about 25 ‘Beeb’ modifed Reslos. And we also introduced our own low noise ribbon microphone transformers for repairs and upgrades.
2013 looks to be just as exciting – we will be launching a range of guitar pickups, making a few more transformers, and also there will be some tube mic power supplies. And of course we will be here to repair your microphones.
Happy New Year!
Stewart & Jane
Xaudia.com
Racking a pair of Ward Beck M480 preamps – Part 1
![]() |
Ward Beck M480 preamp modules |
I recently acquired this pair of Ward Beck M480 input modules. Ward Beck Systems, or WBS, have a great reputation, and so I am very keen to get these racked up as microphone preamps. The modules have four switchable inputs, and a parametric EQ section too.
I have not yet found a copy of the M480 manual, but the Ward Beck Preservation Society have the manual for the later variant, M480C. The pin assignments look the same although the later ‘C’ revision has some additional features such as a switchable phantom.
The modules are very neat and clean inside, and use 44 pole PCB edge connectors. Luckily I had three gold plated connectors in the parts bin. These were salvaged from some scientific equipment that I pulled from a skip. It pays to recycle… and never throw anything away!
Although the modules are in great shape inside, the front panels and knobs are very dirty from years of sticky fingers. Naughty engineers!
The collet knobs can be removed by popping off the coloured caps, and then loosening the central locking nut. Then the black control panel can be prised away from its glue. In both cases they are destined for a long zap in the ultrasonic bath, which will clean them up nicely.
![]() |
WBS M480 stripped down for racking |
Reslosound and the Incomparable Ferrograph
![]() |
The Incomparable Ferrograph brochure |
Quick-change guitar for pickup testing
One challenge when building prototype pickups is testing them quickly. It is easy enough to make the electrical measurements such as inductance, resistance and capacitance, but they don’t really tell you how the pickup is actually going to sound. Sooner or later they need to go into a guitar.
![]() |
Squier by Fender Jagmaster ready for surgery |
This Squier Jagmaster guitar makes a suitable victim for surgery. It was fairly cheap, the neck is straight and plays well, and the strat-style trem cutout means that I don’t need to remove a huge amount of wood.
The first job it to strip the Jagmaster down, removing the strings, scratch plate and the existing hardware from the front of the guitar, and the tremolo system from the rear. Then off with the neck to keep it safely out of the way when the jigsaw comes to play.
Once everything is out then I measured up and cut two aluminium rails that will act as mounts for the new pickups. These were filed round at the ends to fit the existing routing, and drilled and tapped for mounting.
Then came the dirty work. With a jigsaw I cut through the body to make a humbucker-sized hole. You can see just how thin the wood is between the pickup and the tremolo routings – just a few millimetres.
One more job – the bridge no longer has springs to keep it under tension. A block of wood locks it in place instead. The guitar can now be put back together.
Now the pickup can be fitted from the rear with two screws attaching it to the aluminium rails. Screw terminals are also used to connect the wires to the output sockets for the ultimate quick change experience. A brass plate will cover the mess.
![]() |
Rear of ‘quick change’ Jagmaster with locked tremolo and pickup mount |
Now it takes two minutes to swap a pickup! Time for some rapid prototyping. And here’s the front of the guitar with a hexapup fitted from the rear.
![]() |
Jagmaster with Xaudia pickup fitted. |
Lustraphone VR53 microphone documents
Lustraphone was one of several British companies making microphones back in the 50s and 60s. The catalog includes product sheets for several microphones and also some accessories such as mic stands and matching transformers. I was lucky enough to come across some old Lustraphone catalog pages, which included a product sheet for the VR53 ribbon velocity microphone and several other microphones. The catalog probably dates from 1952 or 1953. Note the four digit phone number!
![]() |
Lustraphone VR53 ribbon mic data sheet front |
![]() |
Lustraphone VR53 ribbon mic catalog, reverse |
Although the catalog mentions 20 ohm and 500 ohm models, I have also seen high impedance models of this mic. The frequency response is claimed to be “substantially maintained to 14000 Hz”. From experience, I would say that ‘substantially’ is used loosely. The BBC have a bit more to say about this mic in their R&D reports.
As well as the VR53, the catalog also includes
VC52 “velodyne” noise cancelling microphone
C48 moving coil microphone
C51 dynamic microphone
C151 telephone microphone
AGC496a – Automatic gain control, which looks to be some kind of tube limiter.
Film Industries M8 XLR mod
![]() |
Film Industries M8 ribbon mic with XLR |
Italian ribbon microphones
Today we took delivery of some interesting microphones from Italy. Here they are with some other resident Italians.
![]() |
Geloso double ribbon, Framez, Do-Re-Mi 351MN, CM, Magneti Marelli MC46, Riem and Meazzi |
From left to right we have ribbon mics by Geloso, Framez, Do-Re-Mi, CM, Magneti Marelli, Riem and Meazzi. On closer inspection it seems as though some of the different brands came from the same factories.
The motor of the Do-Re-Mi mic is the same as the Framez, and the Riem is a skinny version of the Meazzi. We also know from previous research that Framez and Meazzi were related companies. Magneti Marelli made 74B copies under license from RCA.
We know less about the RCA-shaped CM microphone. In fact nothing at all about it, other than it is a fairly standard design, made for public address use.
It seems as though there was once a a thriving ribbon mic industry in Italy, with numerous brands and models, but I don’t know of any modern Italian ribbon mics.
Update: I found this ad for the Riem ribbon microphone, from the magazine Selezione Radio, Feb 1952.
1934 RCA PB90 ribbon mic time capsule
Look what’s on the bench today….
![]() |
RCA PB90 ribbon microphone from 1934 |
This is a beautiful RCA PB90, in complete original condition, but need of a little loving care to bring it back to its former glory. Here’s the output transformer….
![]() |
RCA PB90 Ribbon mic transformer, 1934 |
It’s date stamped 21st September 1934! 78 years old. The mic shares a birthday with Leonard Cohen!
That’s amazing.
Grampian microphone documents
Here are links to some manuals and documents from Grampian Reproducers Ltd.
Grampian DP4 dynamic microphone manual.
Grampian price list from June 1976.
Ribbon mic patents
Here are some more ribbon microphone related patents, both US and British, from the 1930s, 40s & 50s.
The diagram (above) is from one of the patents, and may be the first tube ribbon mic!
Look who is really answering your enquiries…
The Trashcaster Lives!
![]() |
Xaudia ‘Trashcaster’ guitar |
A couple of coats of clear lacquer helps the slide-on decal blend in. But perhaps I should have called it the ‘Nashmaster’. Too late now! The last job was to file the nut to take the narrower gauge Nashville strings, and to do this you really need a proper set of nut files. They are not cheap but I found these ones on ebay for around £40, and they did the job quickly and accurately.
Inside the EF40 vacuum tube
Here’s a broken EF40 pentode tube. I dropped it, so took the opportunity to take a peek inside. The construction is intricate and quite beautiful.
![]() |
Inside the EF40 tube, glass envelope removed |
![]() |
EF40 pentode with screen removed |
![]() |
EF40 with getter, mica insulation and plate removed |
![]() |
EF40 showing grids heaters and cathode |
Vacuumtubes.net have a good description of how tubes work, and this diagram from shows all the parts:
MOTM The Italian Job
I have no idea who made October’s microphone of the month. But it is quite a beast, dwarfing the SM57 that I have used as a geologist’s hammer*.
![]() |
Italian ribbon microphone by an unknown maker |
This one came from Italian ebay, and has a whiff of DIY about it. Except that if it is, the work quality is very high. It could well have been a project for an engineering degree. Or perhaps a prototype from a professional workshop? Some parts of the mic are well thought out, but ultimately it is let down by the transformer and low magnetic field.
The microphone body is based around brass tubing with an imposing chromed grill and chromed bells at each end. The base is fitted with a (horrible) 4 pin CB-radio style plug. The yoke is nicely bent aluminium with a turned base and wingnuts.
![]() |
Italian ribbon mic – motor and magnets |
Inside, four large cylinder magnets are clamped between two heavy blocks of mild steel, and the ribbon motor sits at the centre. There is a hint of the RCA 44BX in this approach, and the ribbon is of similar dimensions to that mic. The ribbon itself is clamped with sturdy brass blocks. These magnets here are not really strong enough for the job and the measured field in the ribbon gap is around 1000 gauss – a bit low really. Perhaps they were once stronger than this.
The transformer has its own internal can for extra screening, and the connections to the tranny primary are made with heavy copper for very low resistance. Good thinking!
![]() |
Ribbon mic transformer |
The transformer itself looks home-made from recycled laminations. Although the thick copper wire for the primary is a sensible choice, the inductance is a rather low 24 microHenries and there is no chance of reproducing a full frequency range. These lams look familiar – I have seen similar ones in Thiele microphones for the power transformer, and also, I think, in Geloso amplifiers
![]() |
Domed end cap of the mic, with striped output leads |
The maker, whoever he was, has used brass, mild and stainless steels, copper and aluminium for the construction. Parts are turned, milled, brazed, folded and domed. It looks more and more like an engineering workshop project designed to showcase the maximum number of skills, and in that respect it does a very good job.
Better laminations or a new transformer would show the true potential of this mic, as would some stronger magnets to boost the field. I will try that!
Melodium 42B rebuilt
A few weeks ago we received this rather forlorn looking box of Melodium bits for service!
![]() |
Melodium 42B stripped down to parts |
The good news was that all the important parts were there, and despite some corrosion, the magnets and the transformer were on good shape, which meant that this vintage gem could be restored to some of its previous beauty.
![]() |
Melodium 42B repaired and re-ribboned |
The mic was stripped down and all the parts cleaned up in the ultrasonic bath. Then the magnets and some other bits were painted to stop the rust returning, and the motor reassembled. Dino (the owner) wanted to retain the vintage look of the mic, so the grills were straightened, de-rusted and then given some clear lacquer rather than being refinished. New grill cloth gives some protection against pops and wind blasts.
Then it was put back together and a new cable fitted with XLR output. And of course a new ribbon. The mic looks pretty damn cool!
Thanks to Dino Jakobsen of The Why Project.
Trashcaster guitar (part 3) – Red or Dead
The paint is just transparent enough to let a little of the grain show through. For a high gloss finish it should be given a few layers of clear lacquer, but I’m aiming for the less shiny look of budget 60s guitars so will probably leave it. The scratchplate is less than mint, and so a perfect body may look a bit incongruous. The replacement chrome control plate came from a Fender Jazz bass, adjusted slightly with a file to take off some pointy edges.
The extant screw holes in the body didn’t fit a standard neck plate, so I’ve used these ferrules and screws from StewMac. They work very well and solve the problem. Also, the original tremolo bridge was missing. I have replaced it with a used hardtail bridge from ebay (£6!), and machined a brass block to fill the hole where the vibrato spring must once have been. Perhaps that will give a little more sustain too.
Oktava MK18 condenser microphone
The Oktava MK18 is the less well known, but more sophisticated older brother of the ubiquitous MK219, which is used and abused by hoards of mic-modders who love to chop and swap grills, capacitors and resistors.
![]() |
Oktava MK18, front view with pattern switch |
In contrast to the cardioid-only 219, the MK18 is a dual diaphragm, multipattern condenser mic, with bass roll off (HPF), a -10dB pad, and pattern selector switches.
![]() |
Oktava MK18 rear view with pad, HPF and rear capsule switch |
It also has a fourth switch with large and small cardioid symbols. This controls the ‘mix’ of the rear capsule, allowing the in-between patterns to be selected, to give hypercardioid and supercardioid response. Clever!
![]() |
Oktava MK18 inside, front view showing components |
The switches are actuated by sprung bits of bent metal, and they make the mic very tricky to reassemble.
![]() |
Oktava MK18 inside, rear view showing PCB traces |
The mic has that typical Oktava quirky build style, with etched PCBs and a small square can output transformer that looks different in size style from the ones in the MK219 and 319. The connector is a push-fit din plug!
Unfortunately this mic is designed to run with 60V rather than 48V phantom power. It will work with a normal phantom supply, but is currently giving erratically output, and may need some small modification to make it behave itself!
Trash-caster parts-caster guitar (part 2)
![]() |
Stripping a badly painted guitar body |
Sanding didn’t work well on this so I used some general purpose paint stripper to remove the paint and start again. Beneath the white were traces of some original red paint.
![]() |
Yuck! |
Trash-caster recycled Nashville guitar (part 1)
I have wanted a Nashville tuned guitar for some time, and saw an opportunity when I found a Jazzmaster / Jaguar style body and neck going cheap on a well know auction site. Time to put a guitar together! I’m calling this the Trashmaster (or Trashcaster?) as it is assembled from reused bits and pieces.
![]() |
Hello Kitty? My pink guitar! |
The guitar parts arrived last week, and although the body and scratch plate looked in good shape, the neck was from a different instrument and played like a cricket bat! The body is a sort of vintage pink – not sure if I like it or not. Well, for £56 all in, one can’t complain too much.
I had a spare neck kicking around from last year’s Telemaster project, which played much better but didn’t quite fit in the body socket either. Judicial application of a plane, fret file and some abrasive paper quickly solved that problem!
![]() |
Things almost fit together, but not quite! |
The scratch plate has two cut-outs for pickups and three switches, and covers most of the guitar’s routing. A metal plate from a Jazz bass covers the rest, and again this almost fits, and a hacksaw and file made some unwanted corners disappear.
The pickup holes are also slightly bigger than standard Strat or Tele single coils, and so custom pickups were made. This was pretty simple – using flatwork boards from StewMac, I cut out boards for the top and bottom of the bobbin, and drilled to make room for the magnets. This board is pretty useful stuff – it feels like cardboard but works like plastic. It drills easily and can even be turned on the lathe!
![]() |
Custom pickups made in the Xaudia workshop |
The board was the glued to Alnico 5 magnets, and then the bobbin wound with 42AWG wire, and finished with string before potting in the wax bath. I put 9350 turns on the first pickup, but suffered a wire break about half way through making the second. Problems can often be turned into opportunities, and so in this case I ended up with a tapped 5000+5000 turn pickup for the neck. I have also been scatter-winding, so this should be interesting!
![]() |
Wiring the guitar with scratch built pickups |
The switches on the scratch plate can thus be used for phase and coil tap duties. Try to be neat with the wiring!
![]() |
Fender-looking Trashcaster, and Telemaster |
So, time to put the guitar for a bit together for a moment and see how it looks. Not too bad, but I’m not so sure I need a pink guitar in my life! More here….
Fostex Frankenphone
The Fostex printed ribbons are rather odd microphones, using a membrane with a metal track suspended in a magnetic field to generate the signal. Although they have a natural figure of 8 response, their sound is more like a moving coil dynamic than a ‘true’ ribbon microphone.
This one was probably once used as a donor mic to fix a broken one – it arrived without a capsule assembly.
![]() |
Fostex printed ribbon mic |
Sadly, Fostex UK were unable to supply a replacement part, so for now at least it has been converted into a Frankenphone ribbon mic.
![]() |
Another Frankenphone! |
I used a spare ribbon frame from a Reslo mic, with a pair of small neodynium magnets glued to the frame, which gave a field of around 6000 Gauss (normal Reslos are around 4000 gauss). The new ribbon assembly fitted neatly into the old mount, needing just two strips of foam to hold it in place.
![]() |
Fostex transformer and switch unit |
The Fostex transformer and filter switch were still present, but were designed for the Fostex printed ribbon capsule, and are unsuitable for a ‘real’ ribbon microphone. I wound a custom 1:34 transformer for the job, which works nicely. The mic has a full range output and sounds pretty good!
MOTM Reslo SR1 studio ribbon
![]() |
Reslo SR1 studio ribbon microphone |
The advertising at the time claimed 30Hz to 20kHz – although doesn’t qualify that with a dB range.
![]() |
Reslo SR1 (top) and RB microphones |
Extra sensitivity comes from using a longer ribbon and an extra magnet, and the mic is consequently about 1/3 as long again compared with the more common RB. By necessity the SR uses a different ribbon frame from other Reslo microphones. The mic below came complete with its original fibreglass stuffing – which protects the ribbon, damps any ringing of the shell, but seems to muffle the sound a little.
![]() |
Inside the Reslo SR1 |
![]() |
Reslo SR1 output connector |
The RB microphones are quite notorious for grounding problems, as the mic body is only grounded through mechanical contact at the plug. The SR1 deals with grounding in a better way. The output socket has a hole drilled in the centre with a small wire pushed down and soldered to one of the lugs (see photo, by the green wire). When the mic is reassembled, the long screw that secures the connector makes firm contact with both the mic body and the central wire, giving a good solid ground. This works well, and I now use this approach to ground troublesome Reslo RBs too.
![]() |
Reslo SR1 transformer, being re-wound |
![]() |
winding arrangement for SR1 transformer |
The SR1 was available in both 30/50 ohm and 250 ohm versions, and used the same laminations and bobbin as the later RB transformers, but with a more sophisticated winding configuration. The SR1 transformer has a 5-winding construction, with two primary windings alternating between three secondary windings.
We can supply reproduction SR1 transformers on request.
Thanks to David Pumple for sharing photos and information. The SR1 advert is from http://reslosound.blogspot.co.uk/.
More Hexaphonic and Stereo Guitars
ElectroVoice EV RE20 vs RE320
Everyone who has worked with me will know that I am a big fan of the EV RE20 / PL20 microphones. Although perhaps most famous as a radio presenter’s mic, they are used throughout studio-land for kick drum, horns and vocals – Thom Yorke from Radiohead is one famous user. In our studio, they are the go-to dynamics for pretty much everything that makes a loud-ish sound – kick drum, toms, bass, guitars, horns, vocals, percussion, organs, science experiments, and so on. We have three, and I could happily use more.
![]() |
From top. EV RE20, PL20, RE320 and another RE20. |
I don’t really like severe EQ’ing, particularly with digital EQ, and so the idea of having an RE20 that is voiced for kick is particularly seductive. So, I was very eager to get my hands on the new EV RE320, which is an RE20-shaped thing that is specifically designed for kick drum. But wait! It is also specifically designed for vocals and instruments. How does that work?
![]() |
EV RE320 switch with kick drum (left) and ‘flat’ settings. |
Whereas the original RE20 has a switch which operates a high pass filter circuit, the switch on the RE320 gives different voices for different applications, giving access to ‘flat’ and ‘notched’ settings.
So, what are the differences between an RE20 and an RE320? The most obvious thing is that the RE320 is very black…. supermassive-black-hole black. in fact. And it comes in a zipped reinforced thing that is a hybrid between a box and a bag. This is a big improvement on the crappy plastic boxes that the RE20 came with, which tend to snap at the first opportunity. The RE320 is also about £150 cheaper than the RE20, and is ‘assembled in China’, whereas the RE20 is ‘made in the USA’.
![]() |
RE320 snug in its little box-bag |
More importantly, what about the sound? Here is a frequency plot of a ‘normal’ RE20, recorded in the Xaudia test chamber at 20 cm from the source. The blue line is the flat setting, and the green is with the HPF switched in.
![]() |
RE20 response (blue) and with the HPF (green) |
I had hoped that the flat setting of the RE320 would be be the same as the RE20, but in fact the new model is brighter and louder. Here is the RE320 in ‘flat’ (red) and ‘kick’ (green) modes, along with the RE20 in blue as a reference….
![]() |
RE20 (blue), RE320 in flat (red) and kick (green) modes. |
The RE320 has a higher output in both positions, and also has a peak around 4 to 6 kHz, which may brighten up some vocals. And there is other stuff going on too! A more revealing way to look at the behaviour of the ‘kick’ position is as a difference plot…
![]() |
RE320 – difference between the flat and kick drum settings. |
This plot shows a complex filter network being applied, with a low shelf boost, a -4dB cut at around 350 Hz, and a +5dB boost at 3.5 kHz.
Despite the differences, the RE320 does sound like it belongs to the same family – in fact it sounds rather similar to an RE20 with a +5dB boost around 4-5 KHz. I guess that makes sense!
Only time will tell if I will love this as much as the RE20, but it is a decent dynamic mic and will certainly find uses. I will report back once I have used these on a real recording session.
Stewart, Xaudia
A typical day at the office
Straightening a dented mic grill
Rogue Cadenzas
I have come across a couple of Cadenza ribbon microphones recently that are not what they seem.
The microphones came from different sources, but both had been modified in the same way. The mods were performed long enough ago that the foam had started to disintegrate.
In both cases the ribbon element has been replaced by a dynamic element. and the mic stuffed with pink foam. Both mics are painted black with a silver top, and in both cases the stand adapter is fixed to the microphone rather than being removable.
![]() |
Rogue Cadenza with dynamic element |
There are clearly a few of these floating around. The stand modification looks well done, and I suppose it is just about possible that this was done at the factory, perhaps as a budget alternative to the ribbon mics, although I have not seen any documents to support that.
So, look out when buying old microphones – what you see is not always what you get.
Caveat Emptor!
MOTM Mystery 74B clone
It is said that imitation is the sincerest form of flattery. If that’s true then the RCA 74b junior ribbon was one of the most flattered microphones ever made!
![]() |
Inside the 74b clone |
![]() |
Rear view with horseshoe magnets |
![]() |
‘real’ RCA 74b microphones inside |
—————-
Update, 13 August 2012
A couple of readers have sent in messages about the provenance of this microphone….
“My friends here in Thailand says the symbol is almost definately Chinese. It is certainly not Thai, Vietnamese or Cambodian. By most stuff here has been made in China since China started making things, so your Saigon theory is still the best.” James Browne, Hungry Ghosts
“Hi Stewart. Sent picture to my factory in H.K, the marking is definitely Chinese,” Andy Hearn, ECM
Hexapup hexaphonic pickups now available.
One of the great things about being a micro-business is that you can act quickly! There is no management structure, no liaising with a marketing or accounts departments – we don’t have them! And best of all, no office politics! This means that if we have a good idea, or even a stupid one, we can do it straight away.
Hexapup in a Gretsch-style ‘toaster’ cover
|
Last month we made a stereo guitar pickup prototype, and it was fairly clear from our customers and comments on forums that a few people might want one. So now, six weeks later, we have a ‘production’ version in a humbucker sized* can – the Hexapup!
![]() |
Hexapup – hexaphonic guitar pickup |
![]() |
Hexapup guitar pickup |
The hexapup is actually made of six small pickups, and can be wired for mono, stereo or hexaphonic output
Mono
When wired as a conventional mono pickup, the hexapup has a bright single coil tone. But it also has hum rejection (humbucking) properties because the coils on one side are reverse wound, with reverse magnet polarity.
![]() |
Hexapup – serial number 002 with 43AWG wire |
Stereo
There are two obvious ways for stereo wiring. Either bottom-and-top, or alternating strings. Put another way, the lowest three strings can be sent to one output, and the highest to the other, so power chords could have one sound, and solos another. Or, the E, D and B strings sent to the left, and A, G & e to the right. This makes for nice stereo width, and is great for multi-tracking chords, and chorus type effects. I have my guitar wired this way!
![]() |
Hexapup being mounted to a customer’s guitar |
Hexaphonic
Each coil can be given its own output, volume and tone control which, with series / parallel and phase options gives a staggering number of combinations. Each string can be sent to a different distortion or delay to get strange new sounds, and could even be auto-tuned or pitch shifted separately – that might be weird. With six outputs, imagination is the only limit!
I’ll be writing a bit more about the technical specs in a couple of days, so stay tuned.
* Actually a little deeper than a normal humbucker, but most guitars have plenty of space.
MOTM: Oktava ML52 (Spot the Difference)
I have a soft spot for Oktava microphones. They look cool, come from Russia, are fairly priced, and everyone has fun modifying them. That’s enough to make the ML52 microphone of the month for June.
Oktava have a long tradition of ribbon microphones dating back (at least) to the ML11 in the 1950s. The ML52 is one of the most recent models, with a slightly odd double-ribbon motor assembly. I had some in to service recently, and noticed something odd….
Here are two ML52s – can you see any differences?
The answer is “Yes”. The bottom mic has a logo and serial number, and an XLR that is machined into the bottom bell. It also has slotted screws rather than pozidrive. The grill spacing is also slightly different, but that is harder to see on the photos.
The transformers are also very different. The right hand one is the mic with the logo, and it uses a toroidal transformer. The left hand transformer can looks typical of the China mics, and is connected to a (pointless) circuit board.
Sound-wise, the mics actually sound quite similar, which goes to show just how much the body and grill influence the sound of these mics. The Chinese one has a longer ribbon and stronger (neodynium) magnets, and has slightly stronger output.
![]() |
Response plot for Russian (Red) and Chinese (Blue) ML52 mics |
Beyer ribbon microphone transformer
This transformer came out of a faulty Beyerdynamic M260.
![]() |
Beyerdynamic M260 transformer |
The mic was giving no output, but the ribbon was OK. The problem turned out to be a short in the primary winding, which gave an excuse to take a peek inside.
I was surprised how roughly the primary coil is wound – it really looks like it has been done by hand. Perhaps it is to minimise parasitic capacitance, although that is not usually such a big problem with low impedance windings as they only have a few turns.
In this case the short was located and the original transformer was repaired, but that is not always possible, and sometimes a rewind or replacement is required.
Some of the Beyerdynamic ribbon mics, such as the M500 and some models of M260 have a ‘built in’ high pass filter. This is done by manipulating the transformer inductance, allowing some of the bass frequencies to pass to ground. Some people like this, but others (including myself) prefer a full frequency response.
![]() |
Xaudia B-series (top) and Beyer transformer (below) |
The Beeb Reslo
Xaudia have a limited number of Reslo RB microphones for sale, with upgrades and modifications inspired by the BBC. We call these “The Beeb.”
![]() |
‘The Beeb’. Modified Reslo microphones by Xaudia |
Back in the 1950s and 60s, the BBC published a number of R&D reports on ribbon microphones. Here’s what they had to say about the humble Reslo RB…
They recommended a number of modifications, which included….
- Swapping the transformer to one with higher primary inductance,
- Conversion from 50 ohm to 300 ohm output,
- Fitting a more open interior mesh,
- Removing the cloth around the ribbon motor,
- And reversing the motor assembly so that the ribbon element is at the front.
Xaudia have recreated these mods and added a few more of our own. “The Beeb” has an XLR output, and new 1.8 micrometer ribbon. We also ultrasonically clean these before re-assembly to remove 50 years of gunk. And we put a (removable) sticker on them, so you know that they are 300 ohm mics.
![]() |
Reslos with XLR upgrade |
We have a very limited number of these mics for sale. Alternatively we can upgrade your own mic to these specifications. Please get in touch for details.
Reverend Stereo Slingshot!
The nice people at Reverend guitars sent me a NOS white scratch plate with routing for 3 P90s, which is perfect for mounting the new pickup alongside the two standard P90s. All I needed to do was drill out a hole for a second output jack.
The open chrome pickup cover was made by modifying a covered one, using a dremel cutting wheel.
It looks (& sounds) pretty awesome!
Upgrade Transformers for Reslos
Those who follow this blog may have noticed a certain amount of Reslo-related activity….
![]() |
Xaudia R-series transformers – Reslo upgrades & repairs |
Our new Reslo upgrade transformers are the result of this work. They are made here in our workshop in York, UK using high quality German laminations and teflon insulated silver plated lead-out wires.
They outperform the original Reslo units in terms of resistance noise and frequency response, giving less noise, an extended bottom end, and better impedance matching into modern equipment.
Typical Characteristics
Primary DC resistance 22 milliohms.
Primary Inductance >620 µH at 1KHz, >2.0 mH at 100Hz.
Frequency range <20Hz to >65 KHz.
Ratio 1:32 (available in 1:12 to 1:40, as required).
Stereo hexaphonic pickup prototype
I have been thinking for some time about a stereo guitar that would spread out the signals from the different strings to a pair of amplifiers, or to stereo inputs for recording. So here is my first attempt at winding a stereo pickup.
In order to get some separation between the strings, I decided to make six mini-pickups and combine them into sets of three. Here are the parts – six bobbins, six steel pole pieces, an Alnico 5 bar magnet, and a home made top board.
Each was a coil of 5000 turns 42 AWG enamel wire, around a steel bar. Three of the coils were wound normally and three reverse-wound as they will sit on magnets of reverse polarity.
![]() |
Winding mini-pickups on the Meteor winder |
These were then arranged in two sets of three, magnetised by a bare of Alnico 5. The hard part is keeping track of the winding direction, the start and end of the wires, and the magnet polarity – so that everything is in phase! Each set of three coils were wired in series, and the E,D & B strings sent to one output, and A,G & E sent to the other. Once done, the parts were glued in place, soldered, and then dipped in the wax bath.
![]() |
Assembled six-coil pickup with magnet |
And then it was mounted in the test guitar – my trusty Reverend Slingshot, with the pickup simply taped in place for a test run. The next job is to mount it properly and put a cover on to hide the mess – the hard bit was finding an undrilled P90 cover, but ebay came to the rescue.
![]() |
Reverend Slingshot with prototype stereo pickup |
So, how does it sound? Here is a little run on the guitar and the screenshot from protools. The recording was made into the instrument input of an API A2D, using the digital output at 24bit, 96 kHz into protools. Then no further processing, other than bouncing to 44.1 kHz, 16 bit.
[The stereo image of laptop speakers is usually pretty awful, so best checked out on headphones!]
As always, the stereo is much better on the .Wav version (5 mb…)
The isolation between the two sets of strings is actually very good – you can hear and see on the screen shot that the two channels are very different, following the two sets of strings. It gives a nice interesting stereo spread with the run on the B-string being panned to the right, and the lower notes played on the A string going left.
Another stereo example is here, along with the separate left and right components.
I imagine this would be good for double tracked guitars with big Pete Townsend style chords – using two amps. Although this is wired for stereo, it could easily be made into a hexaphonic* pickup. I’m not sure what use that would be in the real world, but it would certainly be fun to find out.
Update: Here is the pickup mounted properly in the Reverend guitar
Footnote
*The concept of a hexaphonic pickup is by no means new. The earliest patent reference that I could find to the word ‘hexaphonic’ is in this application by Gibson filed in 1990. This refers to midi pickups and states “The first category usually makes use of a special pickup which is mounted on a normal guitar as is the case in the present invention It is deemed important to retain the guitarness or feel of the instrument and a retrofittable hexaphonic magnetic pickup is utilized….” So the idea of hexaphonic pickups was well understood by that point, and in fact must have been obvious even to the very first pickup winders.
Digging deeper I found this article on polyphonic pickups, in Premier Guitar magazine, which covers the subject in better detail than I ever could.
And here is a story from the Gretsch website about Chet Atkin’s stereo guitar from 1956, which used a split coil to send the three bass strings to one side, and the three treble strings to the other. They applied for patent in 1956, and this was granted in 1960.
Bobbins!
MOTM – Grampian GR1 and GR2
It is time again for microphone of the month, and for May we have these lovely Grampian ribbons.
![]() |
Grampian ribbon mics |
Grampian mics come in a variety of model names and numbers which we will try to decypher. These were made in the 1960s and 70s by Grampian Reproducers Ltd, of Feltham in Middlesex, England.
![]() |
Grampian GR1/L and GR2/L ribbon mics |
The mics are labeled GR (“Grampian Ribbon”), followed by a number and a letter. The GR1 designation was used for the semi-cardioid version, and the GR2 is the ‘normal’ figure-8 pattern. The letter shows the impedance of the mic, set by the output transformer winding. They come in Low, Medium, High, and ‘X’ flavours – the letter codes are as follows:
GR1/L and GR2/L … 30 ohms
GR1/X and GR2/X … 200 ohms
GR1/M and GR2/M … 600 ohms
GR1/H and GR2/H … 50K ohms
Here is a rather wobbly scan of the original Grampian data sheet.
The GR1 usually has a silver grill at the front, and a black one at the rear to show its asymmetry, whereas the GR2 has two silver grills. However, inside there is very little real difference between the two models, and any cardioidness* is imposed by additional foam padding around the rear of the ribbon. This foam usually depolymerises over the 40 years or so since manufacture, and the mics will typically fall apart when opened. If the mics have been stored for a long time they will require careful cleaning and new foam suspension before being put back into use.
The mics have a small thin ribbon, held in a removable plastic frame for ease of service. In that respect they are similar to the Reslos and Film Industries mics with which they undoubtedly competed. Unlike the Reslo and FI mics, the symmetrical magnet arrangement means that the GR2 has a true figure-8 response, and are suitable for Blumlein pair or a side mic in a mid-side array.
The internal transformers have a tendency to break, particularly on the H models which have very thin wires. If the break is in the right place the transformer can be repaired, but a rewind may be necessary.
![]() |
Grampian plugs |
External matching transformers were also available, in case one needed to connect to an input of a different impedance. These are still handy for getting a bit more level out of the 30 ohm models.
These were mid-price microphones when they were made. I have a Grampian price list from June 1976, and the GR1 & 2 microphones were priced at £32.05 (plus tax) in a wooden instrument case, and £27.55 in a cardboard box. This would translate today as £180 to £334 plus tax, which would buy one of the better Chinese ribbons or a Beyer M260.
* I made this word up.
UFO over York
Reslo RB 30 ohm & Hi Z mic wiring
Some Reslo RB mics have a transformer with a split secondary that gives the owner the choice of either a 30 ohm or high impedance output. Often these mics get dismantled and rewired, so here is where the internal transformer wires go….
For a 30 ohm output, yellow is the ‘hot’ output, and should eventually end up at XLR pin 2. White is cold, and goes to pin 3.
The green wire should not be grounded, but this sometimes happens by accident if the plug uses one of the pins for ground. The result is a high impedance path to ground from the output, which can act as a filter and give a weak output and weird frequency response.
Mystery mic motor
One of our readers sent in these photos of an unidentified ribbon mic motor. It looks like an attempt at a cardioid pattern, with the magnet and transformer located behind the ribbon. Presumably the original mic was a circular, end address arrangement.
If you recognise this or have any further information, we would love to hear from you.
Thanks to David for sending this in.
Reslo Black & Red Labels continued…
Last month I wrote a post discussing reslo microphones with red and black labels, and spent some time describing the transformers inside. Since that post I have measured more transformers, and the larger data set is beginning to show some definite trends.
![]() |
Transformers from Black label mics – type 10202 |
Perhaps the most revealing transformer characteristic is the primary inductance. The DC resistance is also important in terms of noise, but seems pretty consistent across the measured transformers – usually around 50 mΩ for the primary and 1.2 ohms for the secondary. DC resistance should depend on the thickness of the wire and the number of turns used for the winding, and this seems to be common to the transformers although occasionally the leads may become oxidised.
Measuring the inductance is a little hazardous as it is dependent on the frequency at which the measurement is made. For most of the transformers I have measured at 1kHz and also 100 Hz, but the first few were just measured at 1kHz. The inductance at 100 Hz is usually around 3 times that measured at 1KHz.
The graph shows the measured inductances at 1kHz and 100Hz when available (circles). The transformers marked with crosses were just measured at 1kHz, and the 100Hz value extrapolated from behaviour of the others.
Another way of looking at the transformer data is the relative cut-off frequency (fc) – the ribbon and transformer primary winding form a high pass filter. Assuming the ribbon has an impedance of about 0.3 ohms, then we can calculate fc. We use the value measured at 100Hz as this is closer to the frequencies of interest.
The transformers have a wide range of inductance / frequency values, but fall broadly into two classes. All but one of the transformers from the black label microphones show fc values of between 20 and 50Hz, whereas the red label ones have a much wider spread. About half of the reds are very similar to the blacks, but the others have a much higher fc value – between 70 and 110 Hz.
Many of the black label transformers are marked “10202”, and are occasionally painted in blue, pink or purple. These are sometimes found in red label mics too. The transformers with lower inductance have a ‘sandwich’ of laminations with darker ones in the centre, and these are often marked “SE 4402”.
![]() |
SE 4402 type Reslo transformers |
So it seems that we are somewhat closer to the truth about the red and black Reslos. The black ones are more consistent, and have a better chance of having a deeper bass response. Some of the red ones are just like the blacks, but about half the reds have a different, lower inductance transformer. These were probably designed for speech, and are not inherently better or worse than the others. However, if you are trying to record the lower frequencies of a bass instrument, or a fat electric guitar, then you may feel that the mics with the lower value for fc are more suited to the task.
We have spare 10202 black label transformers in stock, and also make replacement full range 300 ohm transformers for Reslo RB mics. So if your Reslo doesn’t sound up to scratch, then get in touch!
Steampunk tube mic!
BBC R&D reports on ribbon mics
The good old BBC have made many of their research and development reports available through their website, spanning 1944 through 1996.
1945
The Crosley ribbon velocity microphone.
1953
Lustraphone VR53 ribbon microphone
The design of the PGD and PGS ribbon microphones.
The EMI microphone Type 2351E.
Tannoy microphone Type MD. 422.
1956
Design of the PGD and PGS Ribbon microphone Part 2
1958
RCA BK5
1961
Reslo RB
1965
Beyer M160
(Thanks to Santiago Ramos for sending the links.)
More bad magnets
![]() |
Failed magnets in a T-Bone microphone |
The coating around the magnets had peeled away, allowing the rare earth magnets to oxidise and expand. This process of course destroys the ribbon too. The magnets can be replaced, but may not be worth the expense.
I have seen a few microphones that look like this, and the worrying aspect is that it seems to happen spontaneously, possibly because the coating on the magnets was not of high quality, or perhaps they were scratched or cracked on installation.
Nearly all manufacturers now use neodynium magnets for their microphones, and I fear a epidemic in the future.
MOTM: very old LEM ribbon
April has been hectic! We have been repairing microphones, installing a new coil winder, and developing some new & exciting products. And suddenly it is already the 30th and just time for a very brief MOTM.
This month’s mic is a beautiful and very old French LEM ribbon mic, probably from the 1930s….
![]() |
Very old LEM ribbon mic |
Inside, it is very similar to the smaller Amperite ribbon mics, with a large fibreboard frame supporting the ribbon, and a pair of (rather weak) magnets behind.
![]() |
Old LEM mic deconstructed |
The mic has a classic design, with brass sides, a folded steel grill and a cast steel yoke. These solid-sided microphones look strange now, but I guess the thinking at the time was that figure-8 microphones didn’t pick up sound (or reflections) from the sides, which allowed for a very simple construction. The ribbon itself is positioned right at the front next to the grill, with a metal plate across the magnets at the rear, so there is some attempt at making the mic more directional.
The transformer had failed due to insulation breakdown, but with new magnets, a fresh ribbon and repaired transformer, the mic has a reasonable output and nice vintage tone. And it looks great!
Cadenza mic XLR modification
Cadenza ribbon microphones are quite common, but there seem to be more microphones than there are connectors for them. The mics were originally supplied with an integrated stand & connector, which was ideal for desk recording, but not very effective for hanging over a drum kit.
Reslo black and red label microphones
![]() |
Red and black badges on Reslo ribbon mics. |
Are black label Reslos better, or even different from red ones?
There is a rumour that occasionally appears on the internet concerning the relative merits of Reslosound RB microphones. Some of the mics have red labels, and others have black ones, which has led to speculation that the mics must be different, and one type must sound better than the other.
Normally it is stated that the black badged ones are better. Most rumours have some basis in fact, so let’s investigate!
![]() |
Reslosound RB microphone dissected |
Over the past couple of years I have serviced around 50 Reslo mics, with both colours of badges. Here are some of my empirical observations…
1. The black ones are less common than the red ones, but they are by no means rare. I don’t have exact figures but perhaps 75% are red, and 25% black. I will be keeping note from now on!
Edit 29/11/2013: I wanted to correct this figure as I have seen it regurgitated on ebay a couple of times. Having seen a hundred or so more since I wrote this, I really can’t say that one is more rare than the other. I would probably guess that they are equally common.
2. There are at least three styles of red badges from different periods.
3. Some later mics (red and black) have a white plastic ribbon holder. The older mics have black bakelite holders. This should not affect the sound.
So, the only real differences between the red and black label microphones are the transformers (and possibly the state of the ribbons).
Recently, I had seven 30/50 ohm Reslo RB microphones on the bench, and I took the opportunity to examine the transformers. Although the basic construction is the same, the transformers are quite different in looks, and have different inductance values! Some have a striped core with two metals, the middle often being darker or rusty, suggesting a higher iron content.
![]() |
Reslo transformers (left to right) A, B, D, E, F |
Impedance and resistance values
This is hardly a statistically significant data set, but here goes…
Black labels
A. Lp = 0.463 mH, Rp = 84 mΩ, Ratio = 1:12, fc = 103 Hz (purple)
B. Lp = 0.434 mH, Rp = 56 mΩ, Ratio = 1:12, fc = 110 Hz (pink)
C. Lp = 0.470 mH, Rp = 56 mΩ, Ratio = 1:12, fc = 102Hz
I. Lp = 0.441 mH, Rp = 45 mΩ, Ratio = 1:12, (pink)
Red Labels
D. Lp = 0.533 mH, Rp = 52 mΩ, Ratio = 1:12, fc = 89 Hz
E. Lp = 0.204 mH, Rp = 63 mΩ, Ratio = 1:13, fc = 234 Hz
F. Lp = 0.214 mH, Rp = 63 mΩ, Ratio = 1:13, fc = 223 Hz
G. Lp = 0.454 mH, Rp = 49 mΩ, Ratio = 1:12, fc = 105 Hz
Where Lp is the inductance at 1KHz, and Rp the DC resistance of the primary winding.
The mics are supposed to be 30 to 50 ohms output, and so from the ratio we can estimate the impedance of the ribbon and transformer itself to be around 0.3 ohms. The ribbon impedance and transformer inductance form a high pass filter, and so we can calculate the frequency, fc, at which the bottom end response drops away.* This handy tool means that we don’t have to get out our calculators.
* It must be noted that the inductance of a metal core rises and frequency drops, so the cut-off frequencies will in reality be somewhat lower than these values. However, they should be comparable to one another.
What we can say for now, from our very limited data set, is that the three black label transformers, and two of the red ones, have substantially higher inductances and lower cut-off frequencies than the other two red ones. This difference in bass response is likely to be what some users hear as ‘better’. However, it cannot be said that a red label mic always has less bass response than a black one.
The two transformers with purple paint have higher values than the ones with pink paint!
My feeling is that the later Reslos have ‘better’ transformers than the early mics, and that the colour is more cosmetic than diagnostic. But I shall keep adding to this list as more Reslos come into the workshop, and it will be interesting to see what trends develop.
And finally, if you are reading this and once worked for Reslo (or Grampian), we would love to hear from you.
Update 12 May 2012…
In 1961 the BBC R&D group studied the Reslosound RB microphone and recommended that the transformer be replaced with one of higher inductance. It seems plausible that the later Reslos were revised to use a different transformer following that study. You can read the BBC report here.
Stewart Tavener, Xaudia, First posted 24 April 2012, Latest update 12 May 2012
Marvin the Meteor
We have just installed a second Meteor ME307 coil winder at Xaudia, for rewinding ribbon mic transformers, pickups and making new parts.
![]() |
Meteor ME307 with electronic controller |
![]() |
Marvin the paranoid android from the original TV series of Hitchhiker’s Guide to the Galaxy |
![]() |
Marvin the Meteor coil winder |
Marvin even has a brain, although perhaps not the size of a planet. It has more sophisticated controller than our existing Meteor winder, which just has manual controls and a foot pedal. The newer model has preset adjustable ramp, speed, idle, and also a reverse wind setting, which is very handy and removes much of the human element from the winding. Let’s hope he isn’t bad tempered like his namesake !
Reslos in action 2 – Pete Gardiner
Pete Gardiner is a singer/songwriter and acoustic guitar player based in Newtownards, Northern Ireland and his new album ‘Songs at Sunset’ was produced by Paul Steen, who used a Reslo mic on the vocals alongside a Shure SM7b.
Paul bought one of our Xaudia upgrade transformers for his Reslo RB ribbon microphone, to give the mic an output of around 250 ohms. Paul fitted the transformer himself and used Ward Beck preamps for the recording. Paul said….
“I recorded with the reslo and an sm7b but the final edit ending up being 99% reslo. The sm7b is heavily compressed and dialled in on occasion for choruses etc.”
Kolster Brandes KS651 speakers
![]() |
Kolster Brandes speakers |
![]() |
Kolster Brandes KS651 speakers |
They were made sometime around 1970, and have an unusual but very chic cylindrical design, with mahogan-ish veneer and aluminium and gold trim. The bottom acts a bass chamber, and a horn mounted on the top projects the higher frequencies upwards, giving an omnidirectional behaviour in the horizontal plane.
Inside, there is just a single six inch driver, rated at 15 watts, and a lot of foam padding.
It is always a risk buying used speakers, but they both work perfectly and I am rather charmed by the sound. They rather soften and round the edges of the program material, but maintain a good stereo image. Perfect for relaxing in the evening, and an antidote to a day of precise listening on headphones and studio monitors. Although only rated for 15 watts they are plenty loud enough for home use, and well worth the £40 paid.
Gramophone magazine reviewed these in 1970, and they retailed at £31 when new. They recommend placing them on a shelf, but I really can’t agree with that. They seem perfectly suited to sitting on the floor of an elegant room and filling it with music – because of their omnidirectional behaviour they have a wide ‘sweet spot’, and are very easy to position.
They also make good cat pedestals, apparently!
Xaudia Frankenphone ribbon mic
Here is a nice Frankenphone ribbon mic that I put together from spare parts ….
The mic body was salvaged from a broken SE condenser mic, repainted with some nice hammer finish paint and given one of our shiny brass nameplates.
The ribbon motor frame was an unidentified part that was found in an old Reslo mic, but fitted with new neodynium magnets to give a good strong magnetic field. And the transformer was, of course, wound here at Xaudia.
![]() |
Ribbon motor with new magnets, and transformer |
The microphone is rather nice sounding, with a full bottom, big proximity effect and a and good top end response too, for a ribbon. We’ll be putting it through its paces with Silent Fears at the weekend, along with some other new toys.
MOTM: The Australian
This rather lovely RCA44 style ribbon is our microphone of the month for March. He was found on Australian ebay, and so will be known as ‘The Australian’ until his true identity is discovered!
![]() |
‘The Australian’ Vintage RCA style ribbon mic |
The mic has a chrome plated steel bottom, a steel yoke, and brass grills, painted black. Connection to the rear is via a pair of screw terminals for balanced output, but with no ground connection.
Although the body shape is very similar to an RCA44, the interior is more like the early Harry Olson prototypes, with a single large horseshoe magnet and broad flat pole pieces, giving a magnetic field strength across the poles of around 1000 Gauss.
The transformer is a dual bobbin type, with a primary inductance of 255 µH at 1 KHz, and 770 µH at 100 Hz. The thick primary wire gives a measured DC resistance of 27 mΩ, and the overall turns ratio is 1:50. With a 2.4 micrometer ribbon, the Australian has an output impedance of about 600 ohms.
There is no maker’s name plate, and no sign that there ever was once. However, next to the ribbon there is some writing in pencil. This is a little tricky to capture on film, but it reads “RIBBON 23825 B1154”.
Could this be a clue? Perhaps the 23/8/25 is a date from a previous ribbon installation? Sadly, I don’t think so. 1925 seems a bit too early – although ribbon mics were invented in the 1920s, the RCA PB31 (first commercial ribbon and forerunner to the RCA44A) wasn’t introduced until 1931. It seems more likely that this is a copy or prototype made by a small engineering firm, based around patent drawings.
Sound-wise, the mic has a rich warm tone with a decent output for its age, and the 600 ohm output makes it very usable with modern equipment. The lack of an earth connection makes hum an issue, and I am contemplating adding a third terminal to the rear, if I can find one that matches.
Perhaps it was made by an Australian manufacturer? AWA made copies of RCA microphones, and Zephyr were another Australian company that made some nice ribbon mics. For now it is a bit of a mystery, but we would love to hear from you if you know more about this.
Reslo in action – Lena Swanberg
MOTM – Toshiba ribbon mic
![]() |
Small Toshiba Ribbon mic |
Toshiba are better known these days as a giant manufacturer of consumer electronics goods, so it is perhaps surprising to find a ribbon microphone with their name on. In fact back in the 1960s Toshiba made some pretty decent models, some of which were good copies of RCA mics.
February’s microphone of the month is this little ribbon mic, which lacks a model number, but has been referred to as an RCA74b clone. However, although from the outside it resembles a smaller 74b, inside it is very different.
Beneath the outer grills lies a perforated metal baffle backed by a finer mesh screen, which protects the full length of the ribbon against air blasts and pops. The top and bottom of the shield have a tendency to go ‘ping’ – I could actually hear this ringing when speaking into the mic, so a little bit of sticky foam was used to damp this.
![]() |
Rear of the Toshiba showing transformer and magnets |
From the rear, we can see that the field is suppled by a pair of strong horseshoe magnets glued to the pole pieces, which give a measured field of about 3000 Gauss between the poles. The transformer is a twin core ‘humbucking’ type, in this case wound for high impedance.
Once the inner screen is removed, two features stand out as unusual. Firstly, there are no ribbon clamps! The ribbon is simply glued to the supports, and then soldered to the terminals. The arrangement works well enough, but you only get one go at fixing the ribbon.
![]() |
Toshiba ribbon |
The second interesting thing is the small cross bar that bridges the pole pieces. This is actually glued to both the pole pieces and the ribbon itself, dividing the 3.6 mm wide, 60 mm long ribbon into two sections in a 3:2 ratio. I can imagine two purposes for this – to stop the long thin ribbon from travelling to far, and to minimise overtones from harmonic motion.
I have also seen this ‘node’ on another Toshiba ribbon model, so it does seem like a little trick of theirs. The nearest thing I have seen in other microphones is in the Cadenza mics, where the ribbon is glued to a support half way along.
![]() |
Microphone cleaning |
This mic was rather dirty inside. Lots of little bits of iron were interfering with the ribbons movement, making it sound like it was scraping against the sides – which it was! These were easily cleaned with some sticky tape, but the ribbon had to be sacrificed first.
![]() |
New ribbon in the Toshiba mic |
A new ribbon was fitted – soldering 1.8 μm aluminium foil is a bit tricky, but I got the hang of it after a couple of tries. And gluing the cross bar to the ribbon also requires a steady hand!
Once re-ribboned and reassembled (and fitted with a low impedance transformer), the microphone sounds nice, with a relatively flat response up to around 6KHz, where it begins to roll away.
![]() |
Frequency plot for Toshiba ribbon mic at 35 cm. |
‘Yorkshire Tour’ Stratocaster pickups
I spent Saturday helping my former band-mate Ant make new pickups for his 1983 Fender Stratocaster – the stock pickups were OK but lacked a little warmth, and he wanted something overwound (i.e. more turns than a ‘standard’ strat pickup), to give a hotter, fatter sound inspired by Rory Gallagher’s ‘Irish Tour’ album.
![]() |
Ant makes single coil pickup formers from board and magnets. |
Magnetic fields fall away rapidly with distance, and with a moulded plastic bobbin, there is inevitably a gap between the pole piece and the coil. Instead, we made the pickups in the traditional manner, with board and Alnico-V magnets supplied by the mighty StewMac.com. Although it takes a little time to construct the pickup in this manner, this method does give a better sound, as the copper wire coil is wound directly onto the magnets, with the most intimate contact possible.
The old strat pickup assembly removed |
We made a couple of small tools to help with the assembly. A pair of acrylic blocks were cut to act as spacers between the top and bottom of the pickup, to keep the boards parallel. One of these was drilled to help align the magnets as they were knocked into place. The other tool was a spindle for the coil winder.
![]() |
Knocking in the magnets – a strip of wood protects the magnet from the hammer! |
Once the three bobbins are assembled and glued, it is a simple case of winding the required number of turns onto the former without breaking the wire! The neck and mid pickups were wound with 9000 turns of 42 AWG plain enamel copper wire, and the bridge pickup with 9800 turns, which gave DC resistances of 6.7 kΩ and 7.4 kΩ respectively. 7.4kΩ indicates that around 1300 meters of wire has been wound onto the pickup! For comparison, according to Vintage Guitars Info, the original Stratocaster pickups measured circa 5.8 kΩ to 6.3 kΩ.
![]() |
An assembled pickup – magnets and flatwork – on the coil winder. |
It was interesting to see how the original pickups were wound – they are pretty inconsistent, and one in particular had substantial asymmetry to the coil. Perhaps there is some magic to this, but we suspect that it was just their winder drifting out of alignment and piling up the wire on one side.
Fender Stratocaster pickup, circa 1983. |
Our pickups were a bit neater than that! Once wound, the lead wires are soldered on, and the complete pickups are dipped in the wax bath to stop microphonics, and then magnetised. A pair of very powerful 1 inch circular neodynium magnets were used to magnetise the Alnico 5 pole pieces, and we measured around 900 to 1100 gauss for each of the poles. The middle pickup was reverse wound, and given a reverse polarity, by simply flipping the bobbin over for the winding and magnetisation processes. This gives some humbucking when the mid-positions are selected.
The verdict? “Those pickups are PHAT!! Awesome. Loads more bass!“
![]() |
Back together again – Stratocaster heaven! |
Melodium 42B Stand Adapters
Xaudia is pleased to announce this little gadget…
![]() |
Melodium 42B stand adapter |
Anyone who has ever tried to put a Melodium 42B on a mic stand knows that it is challenge, if the original adapter is missing – which it often is.
![]() |
Melodium 42B with Xaudia stand adapter |
The Melodium 42B can now be securely mounted on a stand. Problem solved!
Altec 438C compressor amplifier
The Altec 436 and 438 series are vari-μ tube compressor-amplifiers that were famously used at Abbey Road in the 1960s, when the Beatles were there. The 438C is the best of these models, in that it has a built in mic preamp, and also control of the threshold and release, which make the compressor a lot more usable.
I have been looking for one of these for some years now, to the extent that I even built one from scratch – but of course without the gorgeous meter. I finally took the plunge and bought this one on US ebay, for (what I considered to be) a fair price.
![]() |
Altec 438C compressor |
Having paid the ransom to release it from customs, I picked it up from Parcel Force today. Happily, it looks to be in good original condition, and it should not be too much of a challenge to get it up and running again.
There is plenty of vintage dust inside…
![]() |
Inside the Altec 438C compressor |
A few things will need to be done. These were built for the US market, and the transformer will need to be swapped to a 240V model. It would also be prudent to swap out the electrolytic capacitors. All the original transformers are present, which is a relief as these are difficult / expensive to find.
The ‘clone’ has been in regular use for years, and it will be interesting to see how the original compares!
![]() |
Home made 438B compressor |
Making a spindle for winding pickups
Next week we will be making a few single coil pickups for Stratocasters, so I quickly made this simple little spindle tool to help with the job. It was machined this from 15 mm brass stock on the new mini-lathe, which arrived earlier this week. Below is the roughly machined spindle, before cleaning.
The pickup bobbin slips onto the 3mm post, supported by the wide shoulder, and is locked in place by a square of flatwork board, screwed into the side. This prevents the pickup from slipping on the spindle, without interfering with the wire as it is wound on. The barrel was turned down to 8 mm to fit the Meteor coil winder, although it could equally well be used on a power drill chuck.
SC2 Mini-lathe
The mini-lathe is here!
Delivery was a little late due to the snow and ice, but it finally arrived on Tuesday. After unpacking and cleaning off the excessive quantities of grease, I made a couple of quick jobs as part of the learning curve – the best way to learn is by doing, even if it involves a few mistakes.
First up was to machine this little spindle to hold bobbins for the coil winder. The spindle is in two parts, and is made from 10mm diameter aluminium rod. The lathe is very handy for making little tools like this.
Then I used the lathe to replace the broken connector on this B&O microphone. The old connector was cut off, the hole widened and threaded to take an XLR output. Finally I can get this mic up and running! 🙂
![]() |
B&O BM3 with XLR output |
The lathe is a useful addition to the workshop, and is already proving its worth. It needs a few tweaks to set it up and take some of the slack out of the slides. Luckily, mini-lathe.com have excellent information and guides to setting up these machines.
Grampian GR1 XLR conversion
At Xaudia, one of the most common enquiries that we get is for replacement cables and connectors for vintage microphones. Very often we can help, but some of the connectors are becoming impossible to find in good condition and at reasonable prices.
One example is the Grampian plug that was used for their GR1 ribbon and other microphones. These connectors are hard to find – they can be obtained by buying a less valuable Grampian dynamic mic, but we have found that the plugs come with various slightly different threads, which means that one plug cannot be guaranteed to fit another microphone. And the connector is not ideal in the first place – it has two prongs and for balanced use the screen of the cable is connected to the plug casing (and therefore the microphone) by pressure only. Grounding issues are therefore common.
There is, however, another approach, which is to dispense with the connector entirely, and replace it with a modern, industry standard XLR connector. This microphone arrived without a plug and with a rather battered and bent connector at the bottom of the mic.
The decision was made to replace it with a silver-plated XLR output, which also solves any grounding issues as the third pin may be connected to the body of the mic.
The old connector was cut off, and the housing threaded to accept the new connector.
The new XLR output is then simply screwed in place… and the mic rewired and put back together.
![]() |
XLR modified Grampian |
Everything works nicely – just plug a standard XLR mic cable and it is ready to record.
Some may see this as vandalism, and perhaps from a collectors point of view, it is. However, the conversion is sympathetic, and it is far better for the mic to be making recordings, than to be languishing in a box unused.
Bang and Olufsen BM2 microphone
Last month we were lucky enough to see this rare and beautiful B&O BM2 microphone pass through the workshop.
According to the BeoPhile.com website, these were made from 1951, and was replaced by the very different looking BM3 in 1962. Although different in appearance, the motor assembly and ribbon are similar in both cases.
The BM2 also has a switchable high pass filter to select between the music and voice modes, and also shares a hard-to-find connector with the BM3 & BM4.
Beyond that, we don’t know a whole lot about it!
Reslo wiring guide
This is the ‘official’ wiring information from the Reslo RB brochure…
As you can see, different models had different wiring conventions and required different colour coded cables. This can cause confusion, particularly if the mic has been separated from its original cable in the 40 or so years since manufacture. The most important thing is to check the mic and cable wiring and make sure that they match!
Unfortunately, grounding the mic by connecting the cable screen to the body of the plug does not work well, and these mics are prone to hum. For the low impedance models, it seems sensible to use pins A and B for the balanced output, and pin C for ground. The ground must also be connected to somewhere to the body of the mic and/or to the shell of the cable.
The dual impedance models are particularly problematic, in that pins B and C were used to select either low or high impedance output. This means that if one pin is used as a ground then one part of the transformer will be grounded and some of the signal lost. It is therefore important to disconnect the high impedance leg inside the mic and rewire to match the cable.
MOTM – RCA Selmer RL1
![]() |
RSA Selmer RL1 microphones |
So what’s in a name? Some of these microphones have two manufacturers’ names on them: RSA is proudly embossed on the aluminium body of the mic, whereas the switch plate reads ‘Type RL1, H. Selmer & Co. Ltd., London, Made in England”. Others have RSA on the switch plate too, although these seem to be less common, and I have only come across one example of this.
According to the Vintage Hofner website, Selmer took over the R.S. Amplifiers Ltd in 1947, and presumably these schizophrenic examples come from around that time, when the new owners were using up the cast casings. They are are made from a big slab cast aluminium, with a chrome grill. They are mounted by a yoke with a switch in the base, and the black paint with bare aluminium stripes gives it a very distinctive Bauhaus* / Art Deco appearance.
![]() |
Inside the RCA Selmer RL1 microphone |
The main body of the mic contains the ribbon motor assembly, hidden inside a cotton bag, and a large iron core transformer with a very thick double (parallel) primary winding. The secondary winding connects to a short length of cable, which goes off to the switch.
One thing to note about these mics is that many of them are designed for a very low impedance. The relatively thick piston style ribbon and low ratio transformer combine to give an output impedance of around 15 ohms (measured at 1kHz), and so they can seem very weak when plugged into a modern preamp. In this case a matching transformer is essential to get a decent level from the mic.
Also, these mics do not generally have a secure earth connections, and may hum unless one is provided. Fortunately, it is a simple job to add a terminal to the inside of the body.
![]() |
Piston style corrugated ribbon. |
In terms of sound, these have a very vintage tone and limited bandwidth, rolling off rapidly above around 4kHz – perfect for an old AM radio broadcast effect.
![]() |
RSA RL1 frequency plot |
The RL1 was eventually replaced by the fully Selmer-ised RL2, which used the same grill insert. The RL2 seems to be a very rare thing indeed.
![]() |
Selmer RL2, from Vintage Hofner website |
* The design school, rather than the goth band. Although either might apply.
Fender Telemaster build
My holiday project was assembling this Telemaster guitar, from parts acquired that I have accumulated over the past six months or so.
![]() |
Fender (ish) Telemaster guitar, Xaudia |
The ‘Telemaster’ is an imagined product that Fender might have made in the 1960s or 70s, but never did – it is essentially a Jazzmaster body with Telecaster hardware. In this case I used a neck with a Strat-style headstock, and added a Fender-badged Bigsby vibrato, simply because I love the Bigsby sound.
The ash body & scratch plate were made and sprayed by John Manuel of Carlisle, who did an amazing job with a nitrocellulose transparent white – it really shows the lovely grain below. He can be contacted through ebay.
The neck and locking tuners were from Vanson guitars. The neck is pretty nice quality, although I did need to rub it down with some very fine abrasive paper to remove a couple of rough spots in the varnish. I found it slightly chunkier in profile than an original Jazzmaster neck.
![]() |
Bigsby with super-tremola upgrade |
One thing that I don’t love about Bigsbys is re-stringing them. The ball ends of the strings have a tendency to slip off the metal posts, which can be very frustrating, and one really needs four hands for the job – to hold the string at both ends, keep in under tension, and turn the tuner! Two things help with this – firstly locking tuners clamp the string at that end, and also I have fitted a Duesenberg super tremola kit, from Rockinger, which replaces the posts with a through-hole system. Much less frustrating!
![]() |
home made telecaster pickup |
The pickups are of course home made, and I tried to get as close to the original Telecaster specs as I could. Rather than using a bobbin/former to wind the coil, the core of the pickups were made using top and bottom ‘flatwork’, glued to Alnico rods. Enamelled wire was then wound directly onto the magnets, which avoids the gap between magnets and wire that is inherent with a plastic former.
The bridge pickup was wound with 8500 turns of 42 gauge wire, and the bridge was reverse-wound with around 6500 turns of 43 gauge, and of course reverse polarity for the magnets. Once wound, the pickups are wrapped with string to protect the delicate coil, and then dipped in wax to stop microphonics. The whole thing is very solid, and rather heavy.
I did briefly consider adding a headstock decal to complete the fake Fender look, but decided that it was too good to give anyone else the credit – so it has a nice Xaudia badge. I am rather proud of it! 🙂
Happy 2012!
2011 was a big year, with lots of changes.
Although we have been fixing ribbon mics for our own studio and a few customers for several years, 2011 was the first year that we went public and began to advertise the re-ribboning service. The mic repairs were moved to their own special room, with a dedicated testing chamber. The other big development was the acquisition of our Meteor coil winder, and the decision to do transformer repairs and re-winds in-house. This has vastly expanded the services that we can offer.
In 2011 we repaired some 186 microphones, along with a few guitars, amplifiers, reverbs, DI boxes and so on.
![]() |
Xaudia – Distribution of microphones serviced in 2012, by manufacturer. |
The various models of Reslosound mics have been the most popular brand – there are still a lot of these around kicking around in Europe, and we serviced 37 of these in 2011. As one would expect, there were also quite a few RCA ribbon mics – 23 passed through our hands this year.
We would like to thank all of our customers for helping to make this such an excellent and fun year, and we look forward to even more exciting things in 2012.
Happy New Year!
Stewart & Jane
Xaudia.com
Microphone of the month – Index of posts
Here is a list of all the Microphone of the Month articles up to the end of 2011.
2010
Sep: Old Czech tube mic
Nov: RCA 77b
Dec: Philips ribbon mic
2011
Jan: Sony FV300 dynamic
Feb: Zephyr 30RA
Mar: Shaftesbury Velodyne
Apr: Framez ribbon mic
May: Melodium 42b
Jul & Aug: GEC BCS 2370 & 2373
Sep: Cadenza ‘rocket’ mic
Nov: Lustraphone ribbon mic
Dec: LEM 305 and 306
Looking back, there are a couple of gaps. October was swallowed up by installation work at York Maze, and June saw the arrival and installation of our coil winding facility, so I found little time for blogging.
I hope to be a little more efficient in 2012!
MOTM – LEM 305 ribbon mics
December’s Microphones of the Month are these impressive art deco-style LEM ribbon mics. LEM are a French manufacturer who still make reporter-style dynamic microphones. They used to make really cool looking ribbons!
![]() |
LEM 305 / 306 microphones |
![]() |
Inside the LEMs |
![]() |
LEM 306 ribbon motor with holes in the pole-pieces. |
![]() |
LEM 305 magnets |
The other obvious difference between the microphones is the transformer, with the older models having a larger, iron core, whereas the newer ones have smaller mu-metal laminations, and these transformers are housed in screening cans.
Sadly all three transformers were faulty – the old rubber insulation around them had become brittle with time and the wires were broken. We were able to re-wind the two, but the third had suffered from an earlier bodged repair attempt, and had to be replaced completely. In this case we took the opportunity to give it a 300 ohm output impedance.
![]() |
LEM transformers in metal screening cans |
![]() |
LEM transformer with larger core |
![]() |
Frequency plots for LEM ribbon microphones, after servicing. |
Update 5/1/15: Thanks to Philippe Le Gourdiol for sending in this picture of his LEM ribbon microphone, which is a low impedance model with a high-pass filter. The filter inductor is located below the motor assembly…
STC 4136 condenser mic – phantom power
Here is a little curiosity. STC are mostly known for making high quality ribbon and dynamic mics, inclduing the much loved 4033 and 4038 models. But they also made condenser mics, and this nice little STC condenser mic came in for service recently….
It is model number 4136, and according to its specification sheet would originally have had its own power supply, which ran on either mains voltage or five 9 Volt batteries. Unfortunately the mic was bought without the power supply. The power would have been supplied to one pin of the XLR connector, ground to another, and (unbalanced) audio to the third. The capsule has a sintered glass, metallised backplate.
In practice, the conversion worked nicely, and despite its age and rough looks, the capsule gave a relatively even response, with a broadly cardioid pattern.
![]() |
Measured frequency response plot for STC 4136 |
Strange Reslo microphone
I found this ribbon / magnet / motor assembly inside a Reslo RBL microphone…
..which is very different from the usual Reslo motor design.
I have never seen this type, and I don’t know if it is an attempt by Reslo to upgrade or modernise the old design, a transplant from another make of microphone, or a good quality DIY repair job. It remains a mystery!
When good magnets go bad
This is the inside of a client’s Avantone dual ribbon microphone, which was in pretty bad shape.
The cause of the failure is still a mystery – perhaps it could be due to a process failure in a batch of magnets, or maybe the mic was exposed to an excessively humid environment.
I have seen other mics with signs of flaking on the magnets, but nothing this serious. Neodynes are still a relatively new magnet technology, and how they will stand up to years of studio use and abuse remains to be seen.
Happily, we were able to bring the mic back to life by replacing the magnets and of course re-ribboning the mic.
T-bone RB500 reribbon & upgrade
Ronnie at Diesel Studios in Italy sent in a pair of T-bone RB500 ribbon mics for service and upgrade. Ronnie asked for some photos of the process, and I thought they would make a nice photo-blog.
Here is one of the mics on arrival…
Inside the body, there is further screening to protect the ribbon, and the transformer sits in a metal can.
One of the old ribbons.
This one is not so great!
New 1.8 micrometer ribbons….
The old transformer has primary DC resistance of 90 milliohms, and 30 ohms for the secondary. Those laminations are not very well packed.
Winding new transformers for the mics.
Potting the transformers in the wax bath keeps the coils and laminations from vibrating….
The finished transformers. We may as well re-use the metal can for some extra screening.
Back together again
Sony C38b stand mount repair
Here’s a fairly low-tech solution to a problem.
The Sony C38b is held by a yoke, and the stand mount contains a pair of rubber diaphragms which provide a little bit of shock absorption for the mic.
With time the rubber ion this one has perished, leaving the mic to flop around, rattle, and – worst of all – fall off the mic stand.
Here is how i fixed one with a strain relief rubber grommet, three rubber rings, and a jack plug bushing. The rubber rings are 23mm OD, 16 mm ID, and are the kind available (at least here in the UK) for fitting metal boxes for a ring mains, to stop the cables rubbing. The grommet measured 14 mm OD, 5 mm ID, with a recessed ridge diameter of 9 mm, and is cut off at the bottom to fit.
Firstly, unscrew the large grey knurled nut and take the mount apart. All the old rubber needs to be cut away. Then push the new strain relief grommet into the centre hole in the large grey knurled nut. Remove the bottom nut from the centre screw that is attached to the yoke, and push this into the centre of the grommet. It should look like this….
Then, pack the barrel of the mount with three rubber o-rings.
I then used a bushing from a Neutrik jack plug and inserted this into the centre.
Finally, push the re-rubbered yoke into the centre, and firmly hand-tighten the knurled nut. It should look like this.
The new assembly doesn’t give as much ‘bounce’ as the original, but it holds well, doesn’t rattle, and most importantly, it doesn’t fall off!
SJT
“Big Al” – old German bottle mic
![]() |
Big old German bottle microphone (flaschenmikrofon) |
This time-capsule condition, stunning bottle mic is a recent ebay find, but we know very little about it! So, if you recognise this one, or have any further information, please get in touch.
In looks, this is very much in the style of an RFT CM7049 or a Neumann CMV3, but doesn’t match any of the models that I am aware of by those manufacturers. The mic stands around 320 mm tall by 80 mm diameter, and is beautifully machined from aluminium, so we’ll call him ‘Big Al’.
The bottom bell is secured by two thumbnuts, which make access to the tube and battery compartment very easy.
The capsule is held in place by a clamping ring with 12 screws, and the diaphragm looks to be either nickel, or some kind of metallised film. It is not possible to get the capsule out of the head without removing these screws – not something I really want to be doing. It is even possible to work out the backplate hole pattern from the dents in the diaphragm.
![]() |
Bottle microphone capsule |
The tube is a Telefunken DAF11 which dates back to the 1940s. I haven’t met one of these before, but the datasheet is available at Frank’s, and shows it to be a diode and pentode in the same shell, with a common heater & cathode.
![]() |
DAF11 tube |
The diode part is not used in this mic. The heater supply is a modest 1.2V at 50 mA, and is designed to run from a battery cell.
![]() |
DAF11 bottle mic schematic |
Stellar RM3 upgrades
This Stellar RM3 ribbon microphone recently came into the Xaudia workshop for a transformer upgrade and new ribbon, which of course gives us a chance to poke around inside and take some photos.
![]() |
Stellar RM3 with new Xaudia transformer and ribbon. The old transformer in in the foreground |
The design closely follows the Speiden / B&O / Royer style of microphones – possibly a little too closely for comfort! Like the B&O mics, the ribbon frame slides out of the top, along with the transformer and lots of synthetic woolly packing. The body forms part of the magnetic return circuit, so it was good to see that this one was made of a magnetic steel, rather than brass or aluminium. In my opinion this is one of the better made of the budget ribbon mics.
As is commonly the case with budget microphones, the design is let down a little by the transformer, which measured 47 mΩ (milliohms) on the primary winding, and 90 Ω for the secondary, with a turns ratio of 1:54. Overall the mic gave a measured output impedance of about 650 Ω, of which over 200 ohms is pure DC resistance from the transformer. And in ribbon mics, resistance equals noise.
The new Xaudia 595/40 transformer (in this case a 1:40 ratio) has DC resistances of 0.02 Ω for the primary and 16 ohms for the secondary – much lower than the stock trannie. Although the lower transformer ratio would be expected drop the output level of -2.6 dB, the thinner, lighter ribbon gives an almost equal but opposite effect, and the output levels before and after are very similar. However, the lower DC resistance of the replacement transformer gives much lower noise, and the larger core allows higher sound pressure levels before the onset of saturation.
MOTM – Lustraphone VR53 (a.k.a. Grundig) ribbon mic.
November’s microphone of the month is a British long-format ribbon that was sold under the names “Lustraphone” and ‘Grundig”.
![]() |
A Lustraphone-badged ribbon microphone in glorious brushed stainless steel finish |
This mic was available in at least three different impedances, and I have come across 30, 200, and high impedance models. Unfortunately the badge often falls off so you don’t always know what you are getting! Most of the models I have seen are finished in a bronze hammerite colour, although there is a deluxe low impedance model which has a gorgeous brushed stainless steel finish. Despite the different badges and finishes, the mics are exactly the same on the inside (transformer aside).
![]() |
Lustraphone ribbon microphones on the bench |
One of the ribbon clamps sits on a spring-tensioned screw thread, which allows fine adjustment of the ribbon tension. This makes tuning the ribbon very straight-forward, and allows the owner a little bit of grace if the ribbon becomes a little stretched over time. This feature should probably be mandatory on all ribbonmics!
![]() |
Grundig badged lustraphone mic, opened up for service |
The magnetic field is supplied by a pair of horseshoe magnets (which unfortunately sometimes age with time, losing their strength). Connection to the rest of the world is made by a balanced three-pin paxolin plug, which are hard to come by now. The middle pin is ground, with the audio on the outer two pins.
![]() |
Rear connector and original plug. |
Fortunately, a male XLR connector can be modified to fit by slicing off part of the barrel.
![]() |
XLR connector modified to fit the mic. |
The long ribbon and motor design gives these mics a full bottom end and a pronounced proximity effect. Here are the frequency plots for three of these mics that we have serviced recently:
![]() |
Lustraphone ribbon mic frequency plots. |
(Thanks to Mark Stevens for additional information).
Update 23/1/12. These microphones were also sold under the brand Pamphonic. One appeared recently on ebay:
The shape of things to come….
MOTM – Cadenza Rocket ribbon mic
Sometimes I see patterns or trends in what arrives on the bench. A year ago it was RCA 74s, and in spring 2011 it was Electrovoice ribbon mics. And then the summer brought Melodium 42bs. Of course these are just statistical anomalies or ‘blips’ in the random noise of what my customers send me to repair, but it does at least suggest ideas for the regular ‘Microphone of the Month’ column.
![]() |
Cadenza microphone set with box, documents and stand |
This month these little Cadenza ribbon microphones are in vogue – these were made by Simon SoundService Ltd in London, and were designed by Eric Tomson, Stanley Kelly Peter Bell. The mics have a very 1950s styling, and are often called ‘rocket’ mics. However, having spoken to a couple of customers, the consensus was that many of these microphones no longer sound as good as they should – or at least as good as they look. The complaints are that they are noisy, with low output.
![]() |
Cadenza mic transformer under the knife |
From a technician’s viewpoint (i.e., my opinion :p), there are a some weak points in the design which all relate to the transformer. Firstly, the ribbon clamps are connected to the transformer simply by winding the wire under a nut and tightening it – really not a reliable long term approach. Secondly, the transformer wires are extremely thin, and half a century later the insulation becomes brittle and tends to break, with disastrous results. It is more common practice to use thick gauge wire for the fly-leads to the primary, to keep resistance and noise to a minimum. And finally, as these thin wires become old and oxidised, the mics become noisy.
![]() |
Cadenza windings – primary (left), and 30 ohm output (right) |
The outer high impedance winding is a very fine gauge (approx. 0.07 mm), below which is a single layer of 0.4 mm wire which makes up the primary. The innermost winding is the 30 ohm output, which is approximately 0.2 mm in diameter. Unfortunately the solvent also damaged the bobbin, and and a replacement was found to make a new transformer using the vintage laminations.
The new transformer has a single 600 ohm output, with thicker gauge wires to give lower resistance. It took some effort but the result is a higher output with a lower noise floor, and the mic is much more usable. I’ll post back with a ‘before’ and ‘after’ frequency plot for comparison.
Reslo transformers vs the WEE monster
This little dinosaur sculpture was made out of waste winding coils, stripped mostly from old Reslo and other microphone transformers. 🙂
So why are we stripping transformer coils?
Some older ribbon mics were originally wound for 30 or 50 ohm output impedance, and tend to give a low output level when connected to modern recording equipment.
Many of these low impedance mics, including Reslo and Tannoy ribbons, can be rewound for a modern 200 or 600 ohm input, raising the output to a more useable level, and avoiding noise from having to crank up the preamps.
![]() |
Bobbin from Reslo transformer with secondary winding removed. |
The old Relso 30/50 ohm transformers have an inner (primary) winding consisting of just 12 or 13 turns of thick (0.8 mm) enamelled wire, and a secondary winding of 152 turns of 0.4 mm wire. The thick wire of the inner winding ensures that the primary resistance is low, which keeps noise to a minimum.
![]() |
Reslo transformer rewound for 600 ohm output |
Re-winding the transformer involves removing the outer winding from the original transformer and replacing it with sufficient turns of a thinner gauge to reach the desired turns ratio and output impedance. Usually the original primary winding can be kept in place. The transformer is then reassembled and dipped in wax to fix the windings and lams in place.
This makes the microphone much more usable in a modern studio – transformers can be would for 250Ω, 600Ω or any other desired output impedance.
Syncron AU7a revisited – Phantom power
A while back I wrote about the Syncron AU7a FET condenser microphones, which are sometimes badged as the Fairchild F22.
In that post I had sketched out the schematic. I have since converted one for a customer to run on phantom power, and spotted a glaring error in the schematic. Here is the revised version…
The transistor is of course a P-channel JFET, and the battery polarity is reversed, giving a positive ground. The batteries are switched off when the plug is disconnected, and the routing through the plug makes tracing a little tricky – that was my excuse anyway.
All of this means that some small modifications are needed for phantom power use, because negative ground is by far easier to implement. Using an N-channel JFET makes things much more straightforward – something like this…
The ‘adjust’ resistor is tweaked for best response to a sine wave applied across the head amplifier, and in this case the result was around 1kΩ. JFETs can vary quite a lot, and it is sensible to adjust this individually for each mic.
I built a small breakout board to supply the required voltages from the phantom power. The board fits neatly in the battery compartment.
The “110K” is again adjusted on the bench to ensure that the voltage is correct under load.
There is one more thing to note – now we have switched to negative-ground and an n-channel device, the output cap needs to be flipped round.
Here’s a measured frequency response plot for the modified mic (the dips at around 150 Hz and 600 Hz are likely to be room modes)…
The microphone works perfectly, and it is nice to hear one brought back to life after all these years!
MOTM: GEC BCS2370 & 2373 ribbon mics
![]() |
GEC BCS 2373 and 2370 microphones |
This pair of rather handsome ribbon microphones by General Electrical Company are our microphones of the month for July & August.
The mic on the left is labelled with the model number BCS2373, and was the ‘studio’ model, with a single layer mesh grill, and thumb screw terminals. Like many early studio ribbons, this one has a 30 ohm output impedance.
On the right is the 2370, with a more robust housing and a curved body. These were probably used as ‘lip’ microphones for sports commentary and broadcasting in noisier environments. Indeed, one of our customers sent in a very nice example that came complete with its original handle.
![]() |
GEC 2370 with handle |
These mics were available with different output transformers for different applications. I’ve seen two examples of the 2370 – one had a 10K ohm output, the other measured 600 ohms impedance.
Although they look rather different from the outside, they are twins under the skin – both have identical motor assemblies, with cylindrical pole pieces attached to a large horseshoe magnet, held in place by the magnetic field along The design of the microphone is described in this patent from 1947. All of the GECs that I’ve seen have held their magnetic field well over time. The only real differences between these mics are the output transformer and the body.
As usual, after all these years they benefit from a good clean and a new ribbon. Particularly as this one arrived with a ribbon made from a fag-packet! Both mics are now working well and should provide some good service for years to come.
* Thanks to Santiago Ramos for additional information.
Addenda – one of these came up recently for sale complete with original box. The owner was kind enough to share this photo of the label.
Reslosound RB manual
Mullard mustard capacitors
Coil winder 3 – guitar pickups
There is no ‘Mic of the Month’ article this month – normal service will resume in July. You can read the archive HERE.
Since the Meteor ME307 coil winder arrived, things have been rather hectic and we’ve been busy getting it working, and having some fun winding transformers, inductors and pickups. The friction wheel / clutch that drives the lateral action was worn, but we were able to get a good used replacement part from Poland, and everything is working well.
Hungry? P-p-p-pickup a P90…
James from Hungry Ghosts came down to the Xaudia workshop for an afternoon, which we spent rolling our own guitar pickups. James wanted a pair of P90s to replace the stacked humbuckers on his ‘Vintage’ guitar, and I was still playing about with options for my Reverend Slingshot.
P90s are pretty simple things. We made the base plates by drilling and tapping a bar of 5mm square mild steel, and two “Alnico-5” magnets were glued to this, side by side, like this.
We wound four bobbins, at 7000, 8000, 8500 and 9500 turns, reverse winding some so that they could combine to give a humbucking effect….
Dipping the magnets in hot wax prevents microphonics, and we rigged up a ‘redneck’ wax potting system using a £10 slow cooker from Tesco. This works really well and I’ll describe it in a separate blog post. That done the pickups could be assembled and wired.
I found some nice deep headed screws which made perfect pole pieces for the pickups. Here is the finished P90…
And the new pickups imbued James’ guitar with a spooky pink glow!
Redneck wax potting bath
We needed a better way of wax potting our pickups and transformers. Here’s what we did on a budget…
![]() |
Redneck wax potting bath for guitar pickups |
It’s a hacked 300 Watt slow cooker, acquired from Tesco for the grand sum of £10, which contains an inner ceramic liner and holds about 3 litres. The probe is simply a cook’s thermometer (£14 from Barnitts of York).
It takes a little while to warm up, but sits at about 90 degrees all day, which is just about perfect for potting. The temperature can be further tweaked by running the bath on a variac.
Here’s a newly dipped transformer coming out of the soup – a mix of bees wax and parafin wax…
Coil winding part 2
The new ME307 coil winder is up and running, and we’re jumping straight in to winding some guitar pickups. The idea was that this should be an easy place to start as they can be made with a single winding, and bobbins, wire etc. are all readily available. There is a big pickup winding community in interweb-land, so help and advice should be available.
The winder in action, with the pickup mounted on a metal plate that we made for the job…
Pickups typically use circa 42 AWG wire (0.0633 mm), which is a very fine gauge and requires care whilst winding and soldering to avoid breakages.
The wire tensioners that came with the winder were a little out of calibration, but with a little practice at setting the correct tension and winding speed, we could easily get 7000 turns onto a P90 bobbin with room to spare. It’s probably possible to get 8000 or 9000 turns with practice, to wind a really hot pickup. Here’s the first winding from the Meteor….
Looks nice! The next step will be to rewind some of the broken microphone transformers that we have accumulated over the past few years. But before that we need to mend the clutch plate, which is slipping.
Our New Coil Winder – Meteor ME307
The ‘new’* Meteor ME307 coil winder has just arrived at the Xaudia workshop, after a 500 mile round trip to collect it…
We are very excited about this as it will expand our repair abilities and let us rebuild and rewind broken microphone transformers and guitar pickups. It has a counter to set the number of turns, foot actuated motor control, and of course the all important set of tensioners to allow the wire to be spooled at the correct tension.
The coil winder was probably built sometime in the 80’s and is built like a tank, with some beautiful Swiss engineering inside. Everything needed a little lubrication and a good clean and, although the machine has clearly seen some years of use, everything is still working perfectly.
![]() |
ME307 internal gears and drive train. |
We hope to be doing our first windings later this week…
Direct Inject!
My friends in The Savoy Ballroom needed some stage DI boxes for their numerous acoustic instruments. They wanted to be able to mute the signal whilst tuning up or switching instruments, so I build these nice little boxes for them.
They are based on Bo Hansen’s easy to make design, but with added bells and whistles – well, a switch, a lamp and an extra output.
Job done – now back to recording!
Transformer assembly line!
This week we have been building lots of little transformer moxes to match vintage 30 ohm ribbon mics to modern mic preamps. Correct impedance matching can deliver a +12 dB increase in level without noise penalty or loss of frequency response, which is welcome for many older microphones. Here is how a Reslo RV microphone behaves with and without the transformer:
![]() |
Frequency response plots for Reslo mic with and without an impedance matching transformer |
They are suitable for many old microphones including the following:
- Reslo RBL and RB 30 ohm models
- Melodium 42b
- Grampian ribbon mics (including GR1/L and GR2/L)
- Cadenza ribbon microphones (wired for low-Z use)
- RSA & Selmer ribbon mics
- STC 4033
- Altec and Western Electric ribbon microphones
Mic of the month – Melodium 42b
![]() |
Evolving Melodium 42b – serial no. in the 1700s, 4300s and 6600s (L to R) |
The Melodium 42B was conceived as a French alternative to the RCA 44 family of microphones, and is in its own way every bit as good as the more celebrated RCA mics. At 32 cm high and 14 cm wide, and weighing 2.65 Kg, the 42b is a huge microphone with a large ribbon (68 mm long by 4.2 mm wide) and big powerful magnets*, to give a strong output with low noise.
We have been lucky enough to have four of these through the workshop, and have had the opportunity to observe some for the finer details that have evolved during the production of these beauties. Over the years the grill of the 42b has been refined, with the holes becoming larger, and a solid unperforated band appearing across the bottom of the microphone. Later microphones have a three pin connector at the rear, whist early models are hard-wired.
The magnet structure has also changed over time – earlier models have U-shaped magnets above and below, whereas the later microphones have four block magnets, arranged in pairs and connected by metal plates to complete the magnetic circuit.
The photo on the left shows the later style of magnets. The transformer and inductor are in the circular metal can below. Some models have a rectangular can, but the transformer and inductor inside are similar, at least in the ones we studied. The transformer has a ratio of 1:14, giving an output impedance of 50 ohms**
There is also a facility to adjust the ribbon tension, which should be mandatory on all ribbon mics!
- 1500 – Small grill holes, fixed cable (no connector), U-magnets with North marked, rectangular transformer case
- 1700 – Small grill holes, fixed cable (no connector), U-magnets, circular transformer case
- 1900 – Small grill holes, fixed cable (no connector)r, U-magnets, square transformer case
- 3400 – Small grill holes, connector, U-magnets (unmarked), rectangular transformer case
- 3700 – Big grill holes, connector, U magnets, rectangular transformer case
- 4300 – Big grill holes, connector, U magnets, rectangular transformer case
- 5100 – Big grill holes, fixed cable (no connector), U-magnets, rectangular transformer case
- 5300 – Big grill holes, connector, U magnets, rectangular transformer case
- 6100 – Big grill holes, connector, U magnets (North is marked), rectangular transformer case
- 6600 – Big grill holes, connector, block magnets, circular transformer case
- 8000 – Big grill holes, connector, block magnets, circular transformer case
The 42b has a three-position switch on the front which is used to select “Speaker”, “Voix”, and “Musique” modes. In the first two positions an inductor is switched in parallel with the output transformer which causes the lower frequencies to be rolled off.
The bottom end boost due to proximity effect is pronounced, even at this distance, and the effect on the sound is very musical when capturing acoustic instruments. Of course sometimes you don’t want or need the proximity boost, and the switch conveniently corrects for this at speaking and singing distances.
If you are lucky enough to come across an old Melodium 42b but are disappointed with the sound, it may well have an oxidised ribbon and will need cleaning. The strong magnets are prone to attracting little shards of iron, which stick to the magnets and interfere with free motion of the ribbon.
* It is worth noting that the magnets on these microphones can fade with time – a healthy 42b should have a magentic field between the pole pieces of around 4000 Gauss. One of our microphones measured at just 1500 gauss and it was necessary to replace the magnets with suitable modern alternatives. If you have a Melodium with a weak output it may be worth having the field measured and the ribbon checked. Xaudia can of course help with all those things.
** For optimum results with modern equipment a matching transformer is recommended.
- Mattéo and Axel at Infernale Machine studios in Beziers, France are both Melodium enthusiasts and there are some good photos and some information in French about servicing and cleaning these microphones on their website.
- George at Kore Studios is also a fan – here is a rather lovely song that was recorded at Kore using a 42b for vocals: East Wind by Ed Laurie.
- The original Melodium brochure is available to download from Professor Stan Coutant’s excellent website.
Meazzi and Framez ribbon mics revisited
April’s MOTM was a nice old Framez ribbon mic, and its chunky Meazzi sister also made an appearance. Here’s the article… and here are the microphones:
I’ve had the opportunity to compare these in the anechoic box – here’s how they look (click to enlarge).
![]() |
Frequency plots for Meazzi and Framez mics |
The Meazzi has an overall flatter frequency response, but in both cases there is a significant peak around 4KHz, which should add attack to recorded percussion and clarity & presence to vocals. The Framez is slightly more sensitive in the mid range, but falls away somewhat below 150 Hz.
Whilst revisiting these mics, it is worth looking at the Meazzi’s perforated backplate resonator, which contributes to the pickup pattern and frequency response.
(Nb. Both microphones were fitted with 1.8 micrometer ribbons and wired for low impedance.)
Summer is here, and it is Reslo season.
Another typical day at the Xaudia studio & workshop…
Outside the studio …. flowers, blue sky and cows.
And inside, in the basement workshop…. a Reslo production line!
We see a lot of these little British microphones. The original ribbons are quite thick and have an unusual ‘square wave’ corrugation. Very often these have oxidised and become noisy, and after 50 years they usually benefit from a clean and a fresh ribbon.
Microphone of the Month – Framez ribbon microphone.
April’s microphone of the month (MOTM) is this glamorous shiny blue ribbon microphone by Framez (not to be confused with Framus!)
This has no model or serial number, but is probably from later 1950s or early 60s. Framez were an Italian brand related to Meazzi – according to one source the name is a contraction of Fratelli Meazzi (trans. Meazzi Brothers), which does sound plausible. Framez / Meazzi also made some cool oddball guitars, and were associated with Wandré Pioli. Fetish guitars have much more information about these guitars.
Back to the microphone! This looks very much like a copy of the RCA 74b ‘junior’ microphone, but us physically somewhat smaller. And it is a pretty good microphone in its own right. The magnets have retained their strength over the years, measuring a healthy 4500 gauss between the pole pieces. It has a hefty transformer with taps for both low and high impedance, making it suitable for both recording and PA use.
This one arrived with a thick flat ribbon – probably a DIY ‘kitchen foil’ repair. With a proper 2.5 micrometer ribbon installed, and the mic rewired for balanced, low impedance operation, the sound is clear with a strong output, just lacking a little of the low end proximity boost that you find with many ribbon microphones. The ‘low’ impedance tap is 1:45 ratio, which gives around a 450 ohm output with the 2.5 micron ribbon.
I’m actually very impressed with this little microphone, and it looks great too!
Strange things you find inside mics, part 2
A few months ago I wrote this blog post about the strange things that I had seen inside ribbon microphones. In those cases the ‘strange things’ in question were put in there deliberately by previous owners or techs trying to repair or improve the microphone.
Since then I have come across a couple of microphones which contained even weirder things – insects!
Before modern foams, felted wool was widely used in microphones for shock mounts, wind shields and the like. Unfortunately, moths love this stuff too.
DYNAMICKÉ MIKROFONY
MOTM: Shaftesbury Velodyne Supreme

As you may know, I study quite a lot of vintage ribbon microphones. In general these are simple devices, with just a ribbon, motor, magnets and output transformer . The details and quality of the parts may vary, but most have the same mode of operation. But just once in a while something surprising comes along. Like this Shaftesbury Velodyne Supreme microphone, which is a ribbon microphone with a twist.
The output of a ribbon mic will scale in proportion to the length of the ribbon, at least up to a point. The idea behind the Velodyne was to give increased output by using a super-long ribbon. Normally that wouldn’t give you as high an output as it should, because of ‘rippling’, or other incoherent vibrational modes. But by fixing the ribbon in multiple places they claim to avoid this problem. The microphone was sufficiently novel at the time for the inventors to apply for protection.
Well that’s the theory. In practice the microphone has one giant ribbon that goes round corners, and each length of ribbon has a ‘node’ in the middle, so in total it has 8 elements, each at 45 mm x 4 mm. So 360 mm of vibrating ribbon!
What is more, the microphone has no transformer! I guess the designer thought it had enough impedance already and did not need one.
I wonder how well it worked? Sadly we may never know. The ribbon is broken in many places, and is glued down, so it will net be an easy thing to replace. I’m still struggling over whether to try and get this working or not. I suspect it really ought to be left in its historic condition, but I am curious about how it would have sounded.
Postscript: History shows that this design was not a success. Whether this was for sonic or economic reasons, we can only speculate, but Shaftesbury appear to have abandoned the concept. Their later ribbon microphones were a much more conventional affair, like this Shaftesbury RT model – ribbon, magnets and transformer.
Mic of the Month – Zephyr 30RA high impedance ribbon mic
February’s MOTM is a ribbon microphone made by Zephyr, of Australia. It’s nice to see a microphone that begins with the letter Z!
The mic has a very “retro sci-fi” look, with hammerite paint and a punched metal grill. The name plate reads “High fidelity velocity microphone type 30RA, but despite the misleading model number, the mic is actually a high impedance mode, and the output transformer is marked “50K’.
The magnets are still healthy on this one, kicking out around 2500 Gauss between the pole pieces. The ribbon is 2.5 mm wide and 28 mm long, similar in scale to a Reslo RBL or Grampian microphone.
The back of the ribbon element is covered in lots of felt, to stop air blasts and brighten the mic for vocal use. Removing some of this opens the sound up a bit. This beast was probably intended for use with a home tape recorder, and would have worked very nicely in that application.
The ribbon itself is mounted on a removable plastic saddle, which makes servicing very simple. Which is a good thing, because this one is stretched. This idea is also seen on Reslo and other microphones.
With a new ribbon, and a suitable impedance-matching buffer, the microphone sounds rich and full – well worth the time spent to get it up and running again.
New workshop part 2: Construction Time Again
After a morning with glue and a staple gun, sticking acoustic foam to the soft walls, our new microphone testing chamber is up and running. Here are a couple of photos….
The chamber is hooked up to pink noise and swept-sine equipment, and can collect a frequency plot in a matter of seconds. I’m still working on validation, testing different speakers and mics for best performance, but the facility is already proving its worth.
New workshop! (part 1)
It’s been a quiet month so far for blogging, but a busy one at Xaudia.
We’ve spend the last week building a new microphone workshop in the basement below the studio, including an ‘anechoic’ isolation booth for mic testing. Ralph & Jane have been helping out with building and painting.
Here’s the empty room, waiting to realise its potential:
Wall going up…
A door, window and a slap of paint
Isolation booth and test and measurement area…
And with the test gear going in:
The door on the left is an isolation / semi-anechoic box for testing mics or punishing drummers. The sound treatment is on order.
Anyway, loads left to do….
Thread Adapters for RCA, Sony and other microphones
![]() |
RCA to modern mic stand thread adapter |
A few months ago I was trying to find some thread adapters for a customer with an old RCA junior ribbon microphone, who wanted to use it with a modern standard 5/8″ microphone stand. Most suppliers were charging around $25 dollars, plus post and the inevitable import and handling duties.
So we decided to make some.
These fit most of the ‘big’ vintage RCA microphones, including the 44, 74b and 77 ranges, and also are perfect for Sony professional mics, including the C38b, FV300 and C48 microphones. They also fit Syncron AU7A / Fairchild F22 microphones, and several other American and Japanese microphones with a large thread.
Update:
These are now for sale on the Xaudia website priced at £6.00.
If you want one, please get in touch.
Mic Of The Month: Sony F-V300 Dynamic microphone
![]() |
Sony F-V300 and C38b microphones |
This unusual Sony microphone (left) looks like the younger brother of a C38b (right) or maybe a C48 condenser mic, and shares the same high build quality and some hardware components with these mics. But in actual fact this is a high quality cardioid pattern dynamic microphone, model F-V300.
Inside, the microphone is very simple, with just a capsule in the top compartment, and the on/off switch and transformer wired to a printed circuit board below. The fixed grey output cable looks to be the same type as found on the C38b.
The capsule is suspended from 8 small springs to act as an internal shockmount, which seems to work well, in conjunction with the yoke, to acoustically decouple the microphone element.
This example has some traces of foam around the element, indicating that an internal windshield has at some time been removed.
The label states that the mic is nominally of 1kΩ impedance, although in practice seems lower than this and it has no problems driving standard low-Z microphone preamps. The output is strong and clear across the range, and the output is similar in level and detail to a healthy EV RE20, although with a more pronounced proximity effect.
As far as we know, this microphone was only marketed in Japan, but if you have any information to confirm or deny this, or in fact any information about this mic at all, please let us know!
UPDATE 22/2/11
This microphone has become a bit of a favourite for guitar cabs – it seems to have just the right amount of proximity boost for that application, giving clear and solid presence to the lower end. It also makes a decent tom mic.
Strange things you find inside ribbon mics (part 1)
Microphone ribbons are generally made from very thin metal foil, and aluminium is the ideal material as it is very light but also very conductive. The output of the microphone is inversely proportional to mass, and so a thicker, heavier ribbon will give a lower output, and a thin light ribbon will be more sensitive. Many manufacturers use something typically around 0.0001 inch or 2 microns in thickness. The ribbon is also typically corrugated either along the full length to prevent lateral motion, or at the ends to give a ‘piston’ style of ribbon. Well, that is how it should be.
However, ultra-thin aluminium is hard to get hold of, and the non-specialist may be tempted to make repairs using materials that are more readily available. Here are some things I have found inside microphones masquerading as ribbons – needless to say they were all replaced with good quality aluminium foil of an appropriate thickness!
1. Cigarette Paper.
This microphone actually worked, to an extent! It at least made a sound. The ribbon was made from an old fag packet.
Cigarette packs used to come lined with paper-backed foil – I’ve never been a smoker so I don’t really know why, but I imagine for freshness or something. The foil is thin and already textured – it just needs to be separated from the paper. Actually this last part seems to be optional, and sometimes bits of paper are still attached, making the ribbon heavy and noisy.
1.b I’ve heard that chewing gum wrappers were also used for redneck ribbons, if you want a minty fresh microphone.
1.c Here’s a lovely example of cigarette paper being used for a ribbon in an old GEC microphone.
2. Kitchen Foil
Kitchen foil is easy to handle, yet much too thick to make a decent ribbon. But that doesn’t stop people trying. This is a common ebay trick… the ribbon looks in good condition, but when the mic arrives the output is low and sounds crunchy.
3. Sweet Wrappers
Plastic coated foil or metallised plastic, like that found in sweet wrappers is an interesting innovation, but is generally too heavy and has too high a resistance to make a decent ribbon. Also the plastic doesn’t conduct. This microphone gave almost no signal, and it isn’t hard to see why.
Microphone of the Month – Philips Ribbon Mic
This old microphone by Philips came from a seller in Egypt – I have a vision of it being used back in the 1940s and 50’s, broadcasting out in the desert, near the Pyramids and Sphinx….
The mic was in pretty bad shape and in need of a full restoration. The ribbon was broken, and it was missing a yoke and several other parts. However, it’s a pretty interesting microphone and so gets to be our microphone of the month for December.
This microphone appears to be based closely on Harry F. Olson’s drawings in early patents and presented in the Journal of the Society of Motion Picture Engineers, back in 1931.
The magnetic field is provided by one large permanent barrel magnet. This microphone had a measured field of about 1200 Gauss between the poles, with ribbon dimensions of 5.5 mm wide by 67 mm long.
The original ribbon – sadly very oxidised – was of the piston type, with corrugations at each end and a flat section in the middle region. On closer inspection, the ribbon appears to have been designed for in-field replacement: each end is terminated in a thicker, silver-plated fold of foil, with a hole drilled for ‘easy’ mounting (easy being a relative term in this case). The ribbon is held in place with two brass clamps, each mounted held in place with a singe screw. The disadvantage of using a single screw rather than a pair for the ribbon clamps is that the clamp has a tendency to rotate as it is tightened, which can distort or wreck the ribbon. The clamps are soldered to wires which run to the transformer primary, and these wires are doubled (or tripled) in each case, presumably to keep resistance noise to a minimum.
With a rewire and a new (corrugated) ribbon the microphone works and sounds rather full and rich. However, the output transformer is wound for high impedance output, and won’t drive a standard mic preamp – so the microphone benefits from using an active buffer or an impedance matching transformer. Hum is also an issue with this, despite the massive brass housing.
I haven’t seen another one like this – either in life or on the web. If you have any further information on this, I’d love to hear from you.
Fun with magnets and an Electrovoice V1 velocity ribbon mic
Here’s an early Electrovoice velocity ribbon mic, model V1. These are great looking microphones, but the early versions are rather crudely made and this one, like many others, suffered from low output due to weakened magnets.
Bob Crowley has a few things to say about these mics – not all of them nice!
The motor of this model is based on a single cylindrical permanent magnet, clamped to a pair of metal plates which make up the pole pieces of the assembly. Because of the positioning of the magnet, the magnetic field is uneven, with a significant difference in field between the top and bottom of the motor assembly. In our example we found that the field varied from around 700 gauss at the bottom to 1000 gauss at the strongest point. This is very low for a ribbon mic, and, along with the oxidised ribbon is responsible for a low, noisy output.
Fortunately, we have sourced some very powerful cylindrical N42 neodynium magnets of a suitable size and shape, which are a perfect replacement for the original weak magnet.
With the new magnet the field is increased by a factor of around four, to about 3000-3200 gauss, a much healthier figure which should lead to an increased output and much improved signal-to-noise performance.
Now it’s time to cut a new ribbon, reassemble the microphone, and do some listening tests. In the meantime, we made a rather attractive bracelet from some of the spare magnets.
Mic of the Month – RCA Junior ribbon mics
October was a bad month for blogging – I was busy with the haunted house sound installation, and this was compounded by a fault with my Macbook, which took the Apple repair centre three weeks to find and fix, a long time to track down a faulty cable. With a microphone, that would be the first thing to check! Amongst all the chaos I completely forgot to do the ‘mic of the month’ column.
Back in the real world, I have chosen the RCA Junior ribbon for November’s Mic of the Month. This is because they seem popular at the moment, and we’ve seen four at the workshop for service or repair. The fun thing about this family of microphones is that they vary somewhat in construction, so it is possible to compare and contrast versions from different eras. They tend to be a bit more affordable than the bigger RCA 44 and 77 mics, but still have a good tone that is very usable in a modern studio, especially if the ribbon is in good condition and the transformer is healthy and wired correctly.
The ‘Junior’ was created as a budget version of the RCA44, with a similar motor assembly but smaller magnets and housing. The most commonly seen models are the ‘black badge’ and ‘red badge’ versions, and these are actually quite different inside – the black badge model has a 3.0 mm x 55 mm ribbon, whilst the red badge version I examined has a wider, 4.5 mm ribbon and a stronger magnetic field.
The output transformers on these microphones can be set for 50 Ohm, 250 Ohm or 10KOhm output impedance, and it is worth checking that the mic is wired correctly to get the best performance with modern studio equipment. Normally that will be the 250 ohm setting.
Finally, some RCA mics were actually made in Europe, and it would seem that some appear under different names. The microphone on the left is badged as ‘Magneti Marelli, Milano, Italy’ but is almost identical to the black badge RCA 74b. The only difference is that the Magneti has an alternative transformer, but still with high and low impedance options. The sound is every bit as good.
We’d love to hear from anyone who knows more about the Magneti Marelli microphones and their relationship with RCA.
(Thanks to Jules at DADA Studios in Belgium and Jørn Christensen at Rodeløkka Studio in Norway.)
Microphone of the month – Old Czech tube mic: Tesla?
This is the first ‘Microphone of the Month’ blog, featuring classic or unusual microphones. Hopefully I’ll manage to find time each month for this!
Without the original power supply we can only speculate on the operating voltages. However, a B+ supply of 90V would be a good place for experiments to start – this would give a voltage on the capsule of around 60, and a sensible current through the tube circuit.
Tube mic circuits – Connecting the capsule 2
Last week’s technical article talked about different methods of connecting a condenser capsule to the grid of a tube amplifier, in order to build a tube mic. In this part we consider how to connect a capsule with two diaphragms in order to get a multi-pattern mic.
First let’s examine the different pickup patterns available. There are three extremes: Omni, where the microphone hears sounds equally in all directions. Cardioid (heart shaped*), where sensitivity is greatest in the direction in which the microphone is pointing, falling off to a null point behind. And Figure-of-Eight, with equal (but opposite) pickup in front and behind, and null pickup to the sides. To complicate things further, the pickup pattern may depend upon the frequency, and some mics will have good directionality at higher frequencies, but become less directional as the frequency drops.
But what if we want a microphone with selectable pattern? This can be achieved by arranging a pair of cardioid capsules back-to-back, and combining there signals in different ways. We’ll call these capsules front and back, although of course they could be pointing in any direction. If we require a cardioid signal, we just take the front capsule and for omnidirectional pickup, we mix both signals equally. If we want figure of eight, we subtract the output of the rear from the front: where the signals overlap at the sides of the microphone, they cancel each other out producing null points. Other patterns such as hyper-cardioid and super-cardioid may be considered as in-between positions of these extremes.
So, what is the best way to achieve this practically in our hypothetical tube microphone? Two of the earliest commercial mics with more than one pattern were the Neumann U47, which offered cardioid and omni, and the U48, with cardioid & fig. 8. Let’s look at the U47, as this is probably the simplest way to combine the two capsules.
In the U47 the front diaphragm is grounded through a 100 Meg grid resistor, and the backplate of the microphone’s dual diaphragm is polarised with about 60V, providing the potential difference required. The rear diaphragm is connected to a switch. When the switch is open, the rear capsule is left floating and only the front cardioid diaphragm is active. When the switch is closed, the rear capsule adds its contribution to the front, making an omnidirectional microphone.
What about the U48? We have seen above that if we require figure of 8 instead of omnidirectional, we must subtract, rather than add, the sounds from the rear. To do this we must invert the polarity of the rear diaphragm by reversing its relative charge. So, rather than grounding the rear diaphragm, we must raise the potential by 60V** above the backplate, and 120V above the front capsule! This is easily achieved by using the HT supply to the anode of the tube, but creates another problem. We can’t simply connect the two diaphragms because they are now at different potentials, and so a blocking capacitor must be used. The circuit looks like this:
Finally, to make the microphone have variable pattern, we simply need to make a supply that is adjustable from 0V to 120V, and apply that to the backplate. Alternatively, the signal may be taken from the backplate, through a capacitor to the tube grid. The Neumann-Gefell UM57 does it exactly this way, with the pattern selector in the power supply.
*Really more kidney shaped, and in some languages this is the word used.
** In fact the U48 operates around 50V / 100V.
Tube mic circuits – Connecting the capsule part 1.
Even in the simplest of tube microphone circuits, there are different approaches to connecting the microphone capsule to the tube. Let’s use a single-sided microphone capsule as our starting point.
The capsule behaves as a variable capacitor, changing its capacitance in response to changes in air pressure (i.e. sound). In order to generate a signal, the capsule needs to be polarised by some voltage, creating a difference in potential between the diaphragm and the back plate. This is the first decision that needs to be made – should the polarising voltage be applied to the diaphragm or the capsule backplate?
In the circuit shown on the left, the backplate of the microphone is polarised at 60V, which is obtained from the B+ supply, via a resistive divider and a small capacitor to stabilise and filter the polarising voltage. The membrane is connected directly to the tube grid, and a high value resistor (Rg, typically 100 kΩ to 1000 kΩ) connects both the grid and the membrane to ground. We have our potential difference across the membrane, and the sensitivity of the mic may be adjusted by increasing and decreasing the polarisation voltage. As the capacitance of the capsule changes in response to sound, a tiny current will flow through Rg, and this signal is amplified by the tube.
An example of this arrangement may be seen in the Neumann Gefell M582.
In some cases the grid resistor may be omitted. In the circuit below, which appeared in an article in Tape Op magazine by Dave Royer, the capsule diaphragm is grounded by grid leakage rather than a ‘real’ resistor. It works perfectly.
This simple arrangement is not possible when the capsule backplate is mechanically (and electrically) connected to the body of the microphone. In this case the diaphragm must be polarised directly.
However, having a voltage of around 60V on the tube grid this would adversely change the operating points of the tube circuit, and so a capacitor must be used to block the DC voltage (left). Some listeners claim to hear the difference between different types of capacitors, and so normally a very high quality type should be used in this position. An additional high value polarising resistor is also required, otherwise the high impedance audio signal would be attenuated through the stabilisation cap.
An example of this method of connection is the Neumann-Gefell CMV563, which is designed to be used with bayonette style capsules such as the M7, M8 and M9.
Sometimes it is the membrane which is connected directly to the body, such as in this Teladi K120. The approach is the same as the circuit above.
Unknown German Prototype Tube Microphone – ‘The Unbekannt”
Unknown German tube microphone |
Here is a recent Ebay find. It’s an unbranded tube microphone, and judging from the components probably from the 1960s, in what was formerly West Germany. We’ve called it the ‘Unbekannt’, which is simply German for ‘unknown’. The amplifier circuit is a 3 stage unbalanced transformerless design, using EF40 pentode and an ECC81 twin triode. The final stage is a cathode follower.
As is so often the case, the microphone has been separated from the original power supply, so it is not possible to say what the exact operating voltages would have been. However, the voltage divider for the capsule polarisation may give us a clue – 2 Meg and 400K would be a simple way of using a 240V supply to put 40V on the capsule.
The metalwork is nicely done, and is comparable to Reissmann, Thiele and Teladi microphones of similar age. It seems too well constructed to be a DIY mic, but the oddball range of parts makes us think that it is some prototype from one of the microphone makers of the era.
Lomo 19a9 tube mic manual
Here is a scan of the original Russian manual for the LOMO 19a19 tube microphone.
The full schematics for the 19a9 have been hard to find, particularly the power supply. I’ve saved those schematics as separate files. Click here to see them. I’ve combined the key components for the microphone circuit in the figure below.

There is a discussion about the microphone here at Group DIY.
Thiele microphone brochure
![]() |
Thiele M5 tube microphone |
![]() |
Theile sales document |
Syncron AU7A microphones Part 2
Last time I wrote about a pair of Syncron AU7A microphones. The capsules were in good condition, but the batteries had leaked, causing corrosion and damage to the circuit. For one of these mics I decided to fit a tube circuit based on a 6205 subminiature tube (5840* would do just as well or better)**.
Syncron AU7A (Fairchild F/22) microphones Part 1
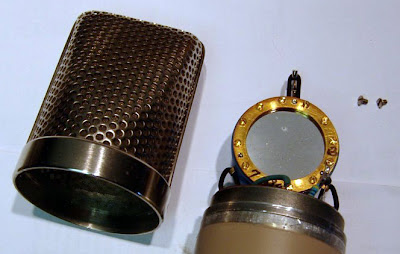
EDIT 21/9/2011 : please note that the schematic posted here contained errors. A revised version is here!
Neumann Gefell UM57 experiments
So what is the effect of ageing of this capacitor? As the electrolyte dries out, the absolute value of the capacitance drops, which will affect the frequency response of the valve amplifier inside the microphone. To simulate this, a capacitance decade box was wired in place of the output capacitor (C3), and the chart below shows how the frequency response changes as the capacitance decreases in 0.2 uF steps.*
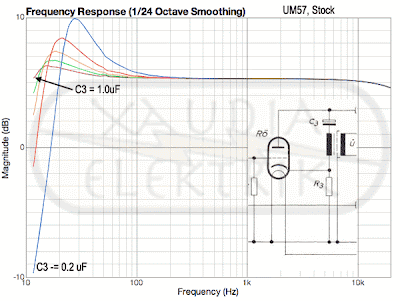
So, having a good quality capacitor here is vital, and the value of this can be used to tweak the bass response if desired. Of course this analysis is just for the tube circuit inside the mic and does not consider the effects of ageing on the capsule itself – that’s a story for another day.
SJT Feb 2010
* Measured using a swept-sine wave from 1Hz to 48KHz.
Recording with the Josephson C720
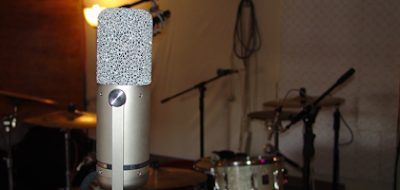
Beyer dynamic transformer data sheet
Gardners Transformers data sheet
Gretsch Atkins SuperAxe circuit
New Toy!
Framus Television
![]() |
Framus Television |
It is quite sad to think that the success of the big American guitar manufacturers (F–, G–, you know who you are!) led not only to some excellent instruments and high standards of construction, but also to the demise of several smaller builders of quality guitars. Cheap imports from the East added to the problem. One such victim was the German manufacturer Framus, who went bankrupt and ceased production at the end of the ’70s. (The company has since been reborn).
Framus made guitars of generally high quality with some interesting features. Here is a 1968 Framus Television semi-acoustic, the shape of which is clearly influenced by Fender’s Jaguar/Jazzmaster (or was it the other way round?) . It has a pleasing asymmetry, with a single f-hole (as far as we can tell, most Televisions had two), three pickups, and a tremolo. The headstock shape is whacky – like a big hand – but we like it. Colour of this one is a beautiful stained carrot-orange-yellow, rather like certain Gretschs – we think they call this ‘aniline yellow’. It has a laminate top and back.
This guitar arrived on the bench with toggle switches in place of the original sliders, as well as a couple of loose wires, which we of course replaced/fixed. The circuit is slightly unusual (which is why it is on this website at all!), so we’ve sketched a circuit diagram to help other owners.
![]() |
Framus Television circuit |
The circuit consists of two parallel output stages each with volume and tone pots (marked T&V in the diagram) , which the player may use to switch between ‘rhythm’ and ‘lead’ settings. This approach predates the days when everyone has booster pedals on the floor, and similar systems are also found on Jaguars and Jazzmasters. In the ‘rhythm’ position, only the neck pickup is active. In the ‘lead’ position any combination of the three pickups may be switched on – the pickups in combination give some audible phase cancellation. There is also a bass cut filter switch. A summary of the switches:
S1 = Bridge pickup on/off
S2 = Middle pickup on/off
S3 = Neck pickup on/off
S4 = Bass cut (lead circuit only)
S5a = Sends neck pickup to rhythm or lead tone/volume circuit.
S5b = Switches between lead and rhythm tone/volume circuits.
As the tone and volume pots are tricky to remove and function well, they were not investigated or measured for value. I think they are just standard.
There’s a good chance that the circuit is similar to Strato Delux models of similar vintage, which also have up to 5 switches. Do let us know if you can confirm or deny this.
G7 microphone
Jakob Erland’s Gyraf G7 DIY tube mic project has proved one of the most popular microphone projects. Several years ago I built a pair of these from scratch, and have since built several variations using different tubes, transformers etc. Below are a few notes on the project.
1. Using a single sided capsule
When using a single sided capsule, the circuit can be simplified somewhat and several parts omitted. The capsule may be wired straight to the tube grid, avoiding use of a coupling cap. Note that this affects the polarity of the mic, so reverse the output wires and be sure to check against an SM57 or similar know microphone. In this arrangement, the backplate polarisation resistor can be lower than 1 gig.
2. Some measured voltages:
I built a version of the microphone by etching Gyraf’s layout. Wired it up and checked some voltages – and found that the supply is rather low under load. I got about 176 Volts without the mic connected, and was down to 136 V with the mic in the loop. Heater supply dropped from 6.3V (set whilst unloaded) to 6.08V. Here are some voltages for reference.
3. Better matching of the capsule polarisation voltages.
Note in the diagram above that one side of the capsule has a slightly higher voltage than the other – no problem in omni or cardioid but noticeable in figure8 mode when recording Blumlein pairs. Here’s a quick fix!